Zawory zwrotne
Parker provides the industry's widest selection of check valves, available in a variety of end connections. Our valves are used in a diverse range of applications, from air and fuel systems to load holding. Our check valves utilize a variet
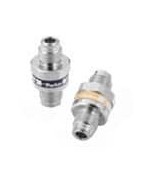
-
Standardowe zawory zwrotne
Solidne grzybkowe i kulowe zawory zwrotne firmy Parker przeznaczone są do najbardziej wymagających zastosowań przy natężeniu przepływu do 303 l/min (80 gal/min) i ciśnieniu do 420 barów (6000 psi) na wielu rynkach, takich jak rolnictwo, budownictwo i produkcja przemysłowa. Zawory mają hartowaną grzybkową lub kulową konstrukcję z gniazdem, która utrzymuje stopień wycieków na poziomie zaledwie 5 kropli na minutę lub mniej, jednocześnie wydłużając okres eksploatacji dzięki ulepszonej charakterystyce zużycia. Ponadto szeroki wybór dostępnych ciśnień otwarcia zapewnia łatwą integrację z układem i niezawodne działanie.
Rynki:
• Rolnictwo
• Sprzęt budowlany
• Sprzęt do transportu materiałów
• Przemysł
• Produkcja
• Urządzenia mobilne
Cechy/zalety:
• Szeroki zakres rozmiarów korpusów, ciśnień zadziałania i natężeń przepływu.
• Niski stopień wycieków — mniej niż 5 kropli na minutę.
• Prosta konstrukcja — wyjątkowa opłacalność.
• Wysoka tolerancja na zanieczyszczenia.
• Wszystkie części zewnętrzne ocynkowane.
Zastosowania:
• Utrzymywanie obciążenia
• Izolacja komponentów
• Zapobieganie przepływowi wstecznemu
• Ochrona antykawitacyjna
• Rynki, na których problemem jest czystość
Dodatkowe informacje techniczne:
Konstrukcja kulowych zaworów zwrotnych firmy Parker obejmuje kulę dociskaną do gniazda przez sprężynę. Blokuje to przepływ w jednym kierunku, ale umożliwia przepływ w kierunku przeciwnym, gdy ciśnienie jest wystarczająco wysokie, aby unieść kulę z gniazda. Ciśnienie, przy którym dozwolony jest przepływ wsteczny, nazywa się ciśnieniem otwarcia. Dzięki zastosowaniu hartowanej kuli i wykańczanego gniazda poziom wycieków wynosi mniej niż 5 kropli na minutę w kierunku blokowania. -
Single Pilot Operated, Pilot to Open Check Valves
Parker’s reliable pilot piston style P.O. check valves are designed for critical applications where safety and load holding is required and flows from 19 to 150 lpm (5 to 40 gpm) and pressures up to 420 bar (6,000 psi) are needed. These valves are available with pilot supply to either the 1st port or 3rd port depending on circuit need, and are generally used in conjunction with linear actuators across several markets within mobile or industrial hydraulics, such as aerials, material handling, and construction where durable and low leak valves are necessary to keep the machinery and operators safe.
Markets:
• Aerial
• Construction
• Material Handling
• Miscellaneous Mobile
Features/Benefits:
• Spherical poppet for low leakage
• Hardened precision ground parts for durability
• “D”-Ring design eliminates back-up rings
• Optional sealed pilot piston
Applications:
• Load holding without fine metering
Additional Technical Insight:
Pilot operated check valves, also known as P.O. checks, are used to lock a cylinder in a holding position with minimal leakage or drift. P.O. check valves that can be opened to allow flow in the reverse direction with an external signal to the pilot port. The valves work best when used in conjunction with a control valve that vents the valve ports to tank when centered. Pilot pressure to open the checks for reverse flow is a ratio of the holding pressure, and are typically 3:1 or 4:1. A 3:1 ratio with a 3000psi load requires a 1000psi signal to the pilot port. -
Cartridge Style Dual Pilot Operated Check Valves
The CPD084P rated at 3000 PSI with a flow rating of up to 5 GPM. The integrated pilot piston has a 3:1 pilot ratio. At rest the internal checks remain seated, blocking flow from exiting the cylinder and locking the cylinder in place. When pressure is applied to either valve port, the check valve will open allowing free flow from the inlet to the actuator port across the check valve. As pressure is applied to shift the cylinder, the internal piston will also shift to mechanically shift open the flow path across the opposite check valve, allowing flow to pass back across the valve in the return direction.
These valves are ideal for load holding applications, where metering conditions are not required. -
Insert Check Valves
Capable of up to 38 gallons per minute, the D1A060 ball type check valve is available in a wide variety of spring sizes from 3 psi to 145 psi. Ii is capable of up to 38 gallons per minute. The D1B125 is capable of up to 132 gallons per minute and has spring sizes from 0 psi to 72 psi. Both of these valves are the perfect solution for high flow, low leakage holding valve applications. -
Pilot Piston Style Dual Pilot Operated Check Valves
Parker’s dual pilot operated check valves are available in pressures up to 5000 PSI and flow rates as high as 50 gallons per minute. The CDP(H) series uses a standard pilot piston and two standard Parker check valves in an assembled body.
At rest the check valves remain seated, blocking flow from entering and exiting the cylinder and locking the cylinder in place. When system pressure is applied to either valve port, the check valve will open allowing free flow from the inlet to the actuator port across the check valve. As pressure builds to shift the cylinder, the internal pilot piston, utilizing a 3:1 or 4:1 ratio, will respond quickly to the system pressure and will shift against the return check. This action mechanically pilots the valve open to allow return flow to pass through the valve from the actuator back to tank. With both ports now open, the valve is unlocked and the hydraulically powered cylinder is free to move. When system pressure is shut off to the valve, the valve will return to the holding condition restricting actuator movement and locking the system in place.
These valves are ideal for load holding applications, where metering conditions are not required. -
Pilot Piston Style Pilot Operated Check Valves
Parker’s single pilot operated (P.O.) check valves are available in pressures up to 5000 PSI and flow rates as high as 50 gallons per minute. The CSP(H) series uses a standard pilot piston and a standard Parker check valve in an assembled body.
At rest the check valve remains seated, blocking flow from exiting the actuator port and locking the circuit in place. When pressure and flow are opened to the valve inlet, the check valve will allow free flow to the actuator. The valve assembly also utilizes an internal pilot piston with a 3:1 or 4:1 ratio. When sufficient pressure is applied to the pilot port, the piston will respond quickly and will shift against the return check. This action mechanically pilots the valve open, unlocking the circuit, to allow return flow to pass through the valve from the actuator back to tank. When system pressure is shut off to the valve, the valve will return to the holding condition restricting actuator movement and locking the system in place.
These valves are ideal for load holding applications, where metering conditions are not required. -
2 Position, 2 Way Normally Closed Poppet Type Manual Valve
Parker’s selection of 2-position, 2-way normally-closed manual poppet valves provide a low leak solution to simple 2-way manually operated circuits. These valves are capable of flows up to 49 lpm (13 gpm) and pressures as high as 210 bar (3000 psi). Parker’s 2-position, 2-way normally-closed manual poppet valves are available with knob, stem, lever, or lock pin manual controls in a normally-closed configurations and are ideal for on/off style applications, such as emergency lift/lower circuits or just simple actuation or motor control on a variety of machinery within the construction, material handling, or industrial markets.
Markets:
• Construction
• Material Handling
• Miscellaneous Industrial
• Miscellaneous Mobile
Features/Benefits:
• Low leak poppet design
• External parts zinc plated
Applications:
• On/off applications
• Emergency lower/actuate applications
Additional Technical Insight:
DL081 is a manually operated 8 GPM (30 LPM) check valve that is rated for 3000 psi (210 Bar) and has leakage rates of less than 5 drops per minute. In the unactuated state oil at port 2 is prevented from exiting port 1. Once the valve is actuated, oil is allowed to pass from port 2 to port 1. Back pressures on port 1 greater than 80 psi (5.5 Bar) will prevent the internal spring from closing the poppet, so care should be taken to ensure port 1 is plumbed back to the reservoir with minimum restriction. Knob, Stem, Lever, and Lock Pin actuators are standard options.
DL101 is a manually operated 13 GPM (49 LPM) check valve that is rated for 3500 psi (240 Bar) and has leakage rates of less than 5 drops per minute. In the unactuated state oil at port 2 is prevented from exiting port 1. Once the valve is actuated, oil is allowed to pass from port 2 to port 1. Back pressures on port 1 greater than 250 psi (17.3 Bar) will prevent the internal spring from closing the poppet, so care should be taken to ensure port 1 is plumbed back to the reservoir with minimum restriction. Knob and Stem actuators are standard options.
Parker’s DL081 and DL101 manual check valves are ideal for emergency lowering applications and for on-off applications where manual actuation is desired to allow flow to return to a reservoir with limited back pressure. -
Check Valve with Thermal Relief
Parker’s D04F2 is a poppet style check valve capable of flows up to 40 gallons per minute. Integral to this valve is a thermal relief valve that protects the circuit from expansion of the hydraulic fluid due to temperature rise. This relief will also act to relieve pressure spikes due to shock. Designers can use Parker supplied pilot spools to create a pilot operated check valve with the thermal relief functions. Common industries where these valve are found:
Forestry
Aerial Lift
Crane
Construction Equipment
Industrial Equipment -
Pilot Operated Check Valve Series CPOM
Pilot operated check valves series CPOM are part of Parker's complete range of sandwich plate valves. They ensure the easy configuration of conventional stack systems.
Depending on the function required, one or two pilot operated check valves are arranged in the ports A and/or B. The free flow direction is always from the valve side to the manifold side.
Function
The check valves open when flowing to the consumer side, where the opposing check valve is hydraulically-mechanically pilot operated simultaneously by a control spool, and thus the return flow is enabled from other consumer sides.
Features
• The valve bodies of the Parker Manapak valve series CPOM are made of steel
• The valve poppet is precisely guided into the steel sleeve and ensures a good seal on the seat
• When the valve poppet is open, the large cross-section allows high flow rates at low differential pressure
• Different control ratios can be chosen with the NG06 and NG10 valves
• Pre-opening for CPOM*HT to achieve smooth opening
Benefits
• Reliable operation in conventional stack systems
• Very good price-perfomance ratio
• Short delivery times -
Throttle Check Valve - Series FM
Double-throttle check valves series FM in NG06, NG10, NG16 and NG25 are part of Parker's complete range of sandwich plate valves and provide high flow at low pressure drop for precise and energy-efficient processes. They ensure an easy configuration of conventional stack systems. Throttle and check valves are located in ports A and B.
Markets:
• Industrial
• Machine tools
Features/Benefits:
• Compact, proven design - ensures reliable operation in conventional stack systems
• Two types of metering needle design (FM2 and FM3) - enable to select the optimum throttle characteristics required to suit the application
• Large bypass check valves - allow high flow at low pressure drop
• Very good price-perfomance ratio
• Short delivery time - no warehousing necessary
• Four sizes:
- NG06 (CETOP 03 / NFPA D03)
- NG10 (CETOP 05 / NFPA D05)
- NG16 (CETOP 07 / NFPA D07)
- NG25 (CETOP 08 / NFPA D08)
Applications:
• Suitable for general hydraulic applications
• Machine tools
Function:
FM2 and FM3 can be used as meter-in or meter-out throttle by changing the mounting position. FM4 can be selected by ordering code as meter-in or meter-out throttle. FM6 is only available as meter-out control.
The throttle check valve can also be used to influence the switching time of pilot operated directional valves. In this case, the valve is positioned between the pilot stage (CETOP 03, NG06) and the main stage (CETOP 05, NG10 up to CETOP 10, NG32). -
Throttle Check Valve - Series ZRD
Throttle check valves series ZRD in size NG06 (CETOP 03) and NG10 (CETOP 05) are part of Parker's complete range of sandwich plate valves. Designed for maximum flow, they ensure the easy configuration of conventional stack systems.
The throttle check function can be located in port A or B as well as in A + B. Meter-in or meter-out functionality can be selected by model code. A low flow/high resolution version in NG06 for sensitive shifting time adjustment of pilot operated directional control valves is available on request.
Markets:
• Industrial
• Machine tools
Features/Benefits:
• Compact, proven design that represents our long-term experience in hydraulics - increases reliability
• High flow capacity - optimum efficiency in relation to valve size
• Various functional arrangements - suitable for almost every application
• Short delivery time - no warehousing necessary
• Available in two sizes:
ZRD01 - NG06 (CETOP 03)
ZRD02 - NG10 (CETOP 05)
Applications:
• Suitable for general hydraulic applications
• Machine tools -
Pilot Operated Check Valve - Series ZRE
Pilot operated check valves series ZRE in size NG06 (CETOP 03) and NG10 (CETOP 05) are part of Parker's complete range of sandwich plate valves and ensure the easy configuration of conventional stack systems. They provide maximum flow rates up to 120 l/min and long lifetime. ZRE valves are typically used in combination with spool type directional control valves to enable an almost leak-free positioning of the actuator.
The inlet flow is free while the outlet flow is blocked. Pressure in the inlet line opens the check valve and allows free outlet flow.
Markets:
• Industrial
• Machine tools
Features/Benefits:
• Compact, proven design - ensures reliable operation in conventional stack systems
• High flow capacity - provides optimum efficiency in relation to valve size
• Long lifetime - offers a very good price-perfomance ratio
• Short delivery time - no warehousing necessary
• Available in two sizes:
ZRE01 - NG06 (CETOP 03)
ZRE02 - NG10 (CETOP 05)
• Check function in A, B or A + B
Applications:
• Suitable for general hydraulic applications
• Machine tools -
Direct Operated Check Valve - Series ZRV
Direct operated check valves series ZRV in NG06 (CETOP 03) and NG10 (CETOP 05) are part of Parker's complete range of high-performance sandwich plate valves and ensure the easy configuration of stack systems. ZRV valves have a cartridge type insert to provide zero leakage and high lifetime. The check function can be located in the P- or in the T-port.
Markets:
• Industrial
• Machine tools
Features/Benefits:
• Compact, proven design - ensures reliable operation in conventional stack systems
• High flow capacity - provides optimum efficiency in relation to valve size
• Leakage-free seat - enables improved process accuracy
• High lifetime - offers low whole-life costs
• Short delivery time - no warehousing necessary
• Available in two sizes:
ZRV01 - NG06 (CETOP 03)
ZRV02 - NG10 (CETOP 05)
• Opening pressure 0.5 bar
Applications:
• Suitable for general hydraulic applications
• Machine tools -
2-Way Cartridge Check Valve - Series C1DB
Parker's check valve series C1DB is a ready-for-use functional unit using proven components of the modular Parker DIN cartridge system that are also offered as separate items and therefore easy to mount. This 2-way slip-in cartridge valve features a wide range of options. Furthermore it is particularly suited for a compact manifold block installation.
Markets:
• Industrial
Features/Benefits:
• Cavity and mounting pattern according to ISO 7368 - for quick and easy integration
• 8 sizes NG16 to NG100 - allows extremely variable use
• Complete units - easy to mount
• Wide range of options - suitable for almost every application
• Short delivery time - no warehousing necessary
Applications:
• Suitable for general hydraulic applications
• General presses -
Hydraulically Pilot Operated Check Valve Series SVLB
Parker's hydraulically pilot operated check valve series SVLB in cartridge design are used to shut-off the cylinder. It allows free flow from A to B. The counter-flow direction is blocked. When pressure is applied to control port X, the ring chamber flow from B to A is released.
Features
• Pilot operated check valve
• 5 sizes, NG16 to NG50
• Cavity and mounting pattern acc. to ISO 7368
• Nominal flow up to 1800 l/min
• Pilot control ratio is 6:1
• Optionally with dampening poppet
Benefits
• Reliable cylinder shut-off
• Short delivery times
Function
When no pressure is applied to the X-port, the flow from B to A is blocked, because the pressure in B is also effective on top of the poppet. Pressurizing the X-port relieves the area on top of the poppet to the drain port and allows flow from B to A. The seat design of the SVLB valve series provides leakfree separation of port A and B in the closed position. -
Pilot Operated Check Valve for In-line Mounting - Series RH
The hydraulically pilot operated check valves series RH for in-line mounting are proven components of Parker's check valve product range which ensure a leak-free blocking of the flow and thus a reliable operation. They allow free flow in one direction (B to A), the counter flow is blocked (A to B). By applying pilot pressure the ball can be lifted from its seat and allows flow from A to B.
Most common use:
• Keeping cylinders leak-free in position, when spool type directional control valves are used
• Return line discharge, when return flow exceeds functional limits of directional control valve at differential cylinders
• As hydraulically activated drain or circulation valve
Markets:
• Industrial
Features/Benefits:
• Spring-loaded balI seated valve - enables zero leakage
• Proven, robust design - ensures reliable operation
• Flexible, versatile mounting in any orientation - makes integration easy
• Short delivery time for most variations - no warehousing necessary
• Maximum operating pressure up to 700 bar
Applications:
• Suitable for general hydraulic applications
Function:
The valves are available without and with hydraulic predischarging.
Without pre-discharging
These valves have a ball as valve element, which quickly enables the full flow cross-section proportionally during pilot operation. A metering position in the pilot port dampens the control movement of the pilot spool so that pressure shocks (unloading shocks) are mostly suppressed.
With pre-discharging
For valves with pre-discharging a spherical polished valve spool (seat valve function) is built-in instead of a ball. The additional check valve achieves a pre-opening which provides shock-free unloading of the fluid, especially at high working pressure and large volumes. -
Zawór zwrotny sterowany bezpośrednio z kołnierzem SAE — seria C5V
Zawory zwrotne sterowane bezpośrednio serii C5V firmy Parker zapewniają swobodny przepływ w jednym kierunku i blokują przepływ w kierunku przeciwnym, zapewniając jednocześnie wysokie natężenia przepływu dla optymalnej wydajności. Należą do wyjątkowo różnorodnej gamy zaworów Parker z kołnierzami SAE.
Kołnierze SAE w rozmiarze SAE61 lub SAE62 umożliwiają zamontowanie zaworu C5V bezpośrednio na kołnierzu wylotowym pomp lub na kołnierzu wlotowym siłowników w celu uzyskania bardzo zwartej konstrukcji. Chronią przed uderzeniami ciśnienia z układu.
Rynki:
• Przemysł
Cechy/zalety:
• Sprawdzona, wytrzymała konstrukcja — zapewnia niezawodne działanie.
• Kołnierz SAE61 i SAE62 — umożliwia uzyskanie kompaktowej konstrukcji.
• Maksymalne regulowane ciśnienie 420 barów i natężenie przepływu od 100 do 750 l/min — wysoka wydajność.
• Liczne ustawienia natężenia przepływu i 5 opcji uszczelnienia korpusu — wyjątkowa wszechstronność.
• Hermetyczna sprężyna — zapobiega sztywnieniu.
• Krótki czas dostawy — brak konieczności magazynowania
• Zawory zwrotne sterowane bezpośrednio.
• 4 rozmiary (SAE ¾ cala, 1 cal, 1¼ cala, 1½ cala).
• 3 sprężyny.
Zastosowania:
• Nadaje się do ogólnych zastosowań hydraulicznych -
Shuttle Valve - Series SSR
Parker's solid shuttle valve series SSR is a threaded cartridge valve in size NG06 or NG10 for a wide variety of applications. Since all parts are assembled in one unit, it is easy to mount and thereby ensures a cost-efficient installation.
Markets:
• Industrial
Features/Benefits:
• Little space required - for compact system design
• Easy assembly - saves costly time
• Leak-free - ensures reliable operation
• Short delivery time for most variations - no warehousing necessary
Applications:
• Suitable for general hydraulic applications -
Check Valve - Series SPZBE
The check valves series SPZBE are very functional and robust slip-in cartridge valves providing high flow rates (up to 900 l/min) in relation to the size. They are available in sizes: NG16, NG25, NG32, NG40 and NG50.
The function unit is fixed inside the manifold by a hexagonal plug with slot. The design is based on CE series with same poppet and sleeve. The different mounting cavity has to be considered.
Markets:
• Industrial
• Molding
Features/Benefits:
• High flow rates up to 900 l/min - optimum efficiency in relation to valve size
• Less installation space required - makes integration easy
• Leak-free from port B to A - ensures reliable operation
• Robust design - for long service life even under rough conditions
• Shortest delivery time for most variations - no warehousing necessary
• 4 different opening pressures from 0.1 to 4.0 bar
Applications:
• Suitable for general hydraulic applications
• Injection Molding -
CM Direct Operated Check Valve
Direct operated check valves from the Parker Manapak series CM are in sandwich design for easy configuration of stack systems. Depending on the function required, one or two check valves are arranged in ports P, T, A, and B. Number and flow direction can be selected from the ordering code.
Features:
- The valve bodies of the Parker Manapak valve series CM are made of steel.
- Eight options for the arrangement of the check valve in the body offer a multitude of uses for hydraulic switching.
- The function can be changed by turning the valve.
- CM2 - NG06 (CETOP 03), CM3 - NG10 (CETOP 05) -
2-Way Slip-In Cartridge Valve - Series SVLA
Parker hydraulically pilot operated check valves for subplate mounting series SVLA in size NG06 enable a reliable operation. They complete Parker's wide pilot control range for DIN cartridge valves. By this modular system, many pressure functions are documented. SVLA is also used as pilot valve of the slip-in cartridge check valves series SVLB.
Markets:
• Industrial
Features/Benefits:
• Compact, proven design that represents our long-term experience in hydraulics - increases reliability
• MTTFD value 75 years - ensures long service life
• Short delivery time - no warehousing necessary
• Flow rate maximum 5 l/min
Applications:
• Suitable for general hydraulic applications -
Gwintowane zawory zwrotne — seria RK, RB
Bardzo wytrzymałe zawory zwrotne serii RK i RB firmy Parker zapewniają niezawodną pracę nawet przy wysokim ciśnieniu roboczym (do 700 barów). Przeznaczone są do wkręcania w proste, gwintowane zaślepki przyłączy do linii hydraulicznych. Przyłącze uszczelnione jest o-ringiem na ramieniu 118° we wnęce montażowej. Korpus zaworu dostarczany jest jako całość, ze sprężynową, hartowaną i polerowaną półkulą z nierdzewnej stali łożyskowej wewnątrz. Gniazdo jest również hartowane i szlifowane.
Rynki:
• Przemysł
Cechy/zalety:
• Sprawdzona, solidna konstrukcja — bardzo dobre właściwości użytkowe.
• Zero wycieków w pozycji zamkniętej — niezawodne działanie.
• Krótki czas dostawy — brak konieczności magazynowania
• Dwie odmiany:
– RK: montowane w kierunku zablokowanym,
– RB: montowane w kierunku otwartego przepływu.
Zastosowania:
• Nadaje się do ogólnych zastosowań hydraulicznych -
General Purpose Check Valve - C Series
As a part of the Colorflow® Family, Parker Check Valves have fully guided poppets. Our superior, fully guided poppet design eliminates wobble and erratic travel that can commonly occur with less durable ball check type construction. C Series Check Valves are available from 1/8” to 2”. The standard soft seat poppet on these check valves provide near zero leakage and come standard in sizes up to 1/2”.
The C Series Check Valve port options include ISO 6149, NPT, BSPP, BSPT and SAE. Material offerings are brass, steel and stainless steel. The steel C Series Check Valve comes standard with a black oxide finish.
These check valves can be found in numerous pneumatic, hydraulic or water applications including:
• Food processing
• Construction equipment
• Factory automation
• Power units
• Plastic molding
• Material handling
• Oil and gas
• Die cast
• Machine tools
• Car washes
• Paper mills
• Marine -
Check Sandwich Valve Series CH
Series CH check valves provide free flow in one direction and blocked flow in the reverse direction. The check can be located in the P port or in the T port.
• Cracking pressure 2.0 Bar (30 PSI).
• Available Sizes:
– CH05 – NFPA D05 / NG10 / CETOP 5
– CH5H – NFPA D05HE / NG10 / CETOP 5H
– CH07 – NFPA D07 / NG16 / CETOP 7
– CH08 – NFPA D08 / NG25 / CETOP 8 -
Pilot Operated Check Valves Series LO
As a part of the Mobile Accessory Family, the Parker LO & LOA Pilot Operated Check valves provide load holding where fluid leakage through the control valve may adversely affect the performance of the system such as clamps, outriggers, and work platforms. Additionally, they can be applied to prevent movement of a load while the pressure source is inactive and a control valve is inadvertently actuated.
A control valve with a free flow (motor) spool should be used on any circuit which includes a Pilot Operated Check. This spool option will prevent unwanted pressure build up between the Control valve and Pilot Operated Check Valve.
• Both versions are available in single and double acting versions.
• Both Models are rated at 3000 PSI with SAE ports. The maximum recommend actuator flow for the LO is 25 GPM. The LOA is rated at a lower 8 GPM actuator flow.
• Standard porting options for the LO are 1/2” NPT and SAE-10.
• Standard porting options for the LOA are 1/4” NPT, 3/8” NPT, and SAE-6. -
PILOT OPERATED CHECK SANDWICH VALVESeries CP
Series CP pilot operated check valves are designed for maximum flow rates. The valves are typically used in combination with spool type directional control valves to ensure leak free positioning of the actuator. The inlet flow is free while the outlet flow is blocked. Pressure in the inlet line opens the check valve and allows free outlet flow.
• High life time.
• Check function in A, B or A + B.
• Available Sizes:
– CP05 – NFPA D05 / NG10 / CETOP 5
– CP5H – NFPA D05HE / NG10 / CETOP 5H
– CP07 – NFPA D07 / NG16 / CETOP 7
– CP08 – NFPA D08 / NG25 / CETOP 8 -
Direct Operated / Hydraulically Pilot Operated Check Valve...
The direct operated and hydraulically pilot operated check valves series C4V are proven components of Parker's check valve product range. The robust valves are almost universally applicable and provide numerous options.
Features
• 3 sizes: NG10, NG25, NG32
• Proven, robust design
• Leak-free seat type cartridge
• Max. pressure 350 bar
• Optionally with position control (pilot operated version)
Benefits
• Versatile
• Good price-performance ratio
• Short delivery times, no storage necessary
C4V direct operated
Direct operated check valves C4V allow free flow from A to B. The counter direction is blocked. The C4V series are equipped with a leak-free seat type cartridge.
Function
The pressure arising in port A lifts the poppet from the valve seat and releases the flow to B. In the counter direction, the spring and the pressure on top of the cartridge hold the poppet onto the seat and block the flow.
C4V pilot operated
Hydraulically pilot operated check valves series C4V also allow free flow from A to B, the counter-flow direction is blocked. When pressure is applied to control port X, the ring chamber flow from B to A is released. Up to four different pilot control ratios are available.
Function
When no pressure is applied to the X-port, the flow from B to A is blocked, because the pressure in B is also in effect on top of the poppet. Pressurizing the X port relieves the area on top of the poppet to the drain port and allows flow from B to A. The seat design of the valve provides leak-free separation of port A and B in the closed position.
Hydraulically pilot operated valves with position control are available on request. -
CHECK SANDWICH VALVE - CM SERIES
Parker’s CM series check valves provide an integral, full flow check valve in the pressure 'P' port, 'A' port, 'B' port, or the tank 'T' port of the directional valve. Reverse flow is blocked. The CM2 and CM3 sizes offer a combination P&T check version.
Markets
• Factory Automation
• Lumber & Wood
• Machine Tools
• Material Handling
• Miscellaneous Industrial
• Miscellaneous Manufacturing
• Miscellaneous Processing
• Molding
• Packaging Machinery
• Plastic Processing
• Primary Metal Refining Process
• Rubber & Tire Processing
• Vehicle Assembly Facilities
Features/Benefits
• Valve bodies are manufactured from steel which provides extra strength and durability for longer life
• Internal hardened steel components also provide longer life
• Positive shut-off is provided by a fully guided poppet and allows full flow in the unchecked position
• Parker CM sandwich style check valves can be used either on the 'P', 'A', 'B', 'T' ports, or combinations
• Large internal flow paths allow high flow at low pressure drop
Applications
• Suitable for general hydraulic applications -
Direct Operated Check Sandwich Valve – CM Series(AP)
Parker direct operated check valves series CM in sandwich design are part of Parker's complete range of sandwich plate valves and ensure an easy configuration of conventional stack systems. Additionally they provide a very good price-performance ratio.
Series CM is available in two sizes, NG06 and NG10. Depending on the function required, one or two check valves are arranged in ports P, T, A, and B. Number and flow direction can be selected from the ordering code.
Markets:
• Industrial
• Machine tools
• Rubber & tire processing
Features/Benefits:
• 8 options for the arrangement of the check valve in the body - multitude of uses for hydraulic switching
• Valve bodies are made of steel - extra strength and durability
• Function can be changed by turning the valve - easy handling
• Short delivery time for most versions - no warehousing necessary
• Two sizes:
- CM2 - NG06 (CETOP 03)
- CM3 - NG10 (CETOP 05)
• Maximum operating pressure 350 bar
Applications:
• Suitable for general hydraulic applications
• Machine tools
• Tire presses -
Pilot Operated Check Sandwich Valve – CPOM Series(AP)
Pilot operated check valves series CPOM are part of Parker's complete range of sandwich plate valves and ensure an easy configuration of conventional stack systems. Additionally they provides a very good price-performance ratio.
Depending on the function required, one or two pilot operated check valves are arranged in the ports A and/or B. The free flow direction is always from the valve side to the manifold side.
Function
The check valves open when flowing to the consumer side, where the opposing check valve is hydraulically-mechanically pilot operated simultaneously by a control spool, and thus the return flow is enabled from other consumer sides.
Markets:
• Industrial
• Machine tools
• Rubber & Tire
Features/Benefits
• The valve bodies of the Parker Manapak valve series CPOM are made of steel
• The valve poppet is precisely guided into the steel sleeve and ensures a good seal on the seat
• When the valve poppet is open, the large cross-section allows high flow rates at low differential pressure
• Different control ratios can be chosen with the NG06 and NG10 valves
• Reliable operation in conventional stack systems
• Very good price-perfomance ratio
• Short delivery time
Applications:
• Tire presses
• Machine tool -
Hard Seat In-Line Check Valves (up to 5000 psi) - Compact One...
DT Series Check Valves (up to 5,000 psi) have a metel to metal hard seat design with a one piece body and all steel construction. The body is a compact size with a variety of male port end configurations. These are in-line unidirectional valves with standard spring crack pressures of 1, 5, and 65 psi. The DT Series are available in a wide range of sizes for flow capacities up to 100 gpm.
Check valves are important components that are often overlooked when building a fluid system. A check valve can optimize system performance in the following ways:
• Ensure hydraulic fluid flows in only one direction
• Eliminate potential damage from back pressure
• Isolate sections of a system or system components
Basic check valve construction consists of a valve body with an inlet and an outlet port. Inside, a moveable poppet valve is controlled by spring pressure. In most cases the valve is normally closed, opening when the fluid pressure is greater than the spring force (crack pressure), thus allowing the fluid to flow in only one direction. When reverse flow attempts to enter though the outlet the poppet closes and flow through the valve is stopped.
Hard seat check valves utilize a durable metal to metal seal to withstand high flow surges and provide longer service life.
Technical Characteristics:
• Sizes: 1/4” to 1-1/4”
• Material: Steel
• Inlet Port Ends: Male ORB, Male JIC, Male ORFS
• Outlet Port Ends: Male ORB, Male JIC, Male ORFS
• Optional crack pressures available from 1 to 200 psi in 5 psi increments
• Orificed valve option
• Custom shapes and configurations
Note: Some options may not be standard configurations. Please contact the Quick Coupling Division for availability and delivery.
Markets:
• Industrial
• Construction
• Agriculture
• Transportation
• MRO
Features/Benefits:
• Allows the fluid to flow in only one direction, protecting the system from fluid back pressure
• metal to metal hard seat provides longer life and is durable for high flow surges
• Custom shapes and configurations can integrate special features to reduce the number of components and potential leak points in a system
• Optional crack pressures are available on request
• Optional orificed valve allows metered flow when the valve is closed. Orifice bore size is determined by application requirements.
Applications:
• Industrial, mobile, and construction equipment
• Restrictor Check Circuit
• High/Low Pump Circuit
• Slow Advance/Rapid Return Circuit
• Oil Cooler By-Pass Circuit
• Sequence Circuit
• Pilot Pressure Circuit
• Accumulator Circuit -
Soft Seat In-Line Check Valves (5000 psi) One Piece Body,...
CPIFF Series Check Valves (5,000 psi) are soft seat, zero leakage poppet check valves with compact one piece construction. Standard crack pressures are 5, 15, 25, and 65 psi. These valves are available in a wide range of sizes up to 1"", with female fitting ends and flow capacities up to 30 gpm.
Check valves are important components that are often overlooked when building a fluid system. A check valve can optimize system performance in the following ways:
• Ensure hydraulic fluid flows in only one direction
• Eliminate potential damage from back pressure
• Isolate sections of a system or system components
Basic check valve construction consists of a valve body with an inlet and an outlet port. Inside, a moveable poppet valve is controlled by spring pressure. In most cases the valve is normally closed, opening when the fluid pressure is greater than the spring force (crack pressure), thus allowing the fluid to flow in only one direction. When reverse flow attempts to enter though the outlet the poppet closes and flow through the valve is stopped.
Soft seat check valves have an O-ring or similar elastomeric seal between the poppet and body for improved leak resistance. The soft seat design is most compatible with ""clean” systems and is not indented for use in systems that have high surge flow. The seal material dictates the temperature range of the valve.
Technical Characteristics:
• Sizes: 1/4” to 1”
• Materials: Steel, Brass
• Seal Material: Fluorocarbon
• Standard Crack Pressures (psi): 5, 15, 25, and 65
• Port Ends: Female NPSF, Female SAE, Female British Parallel BS 2779
• Optional crack pressures available
• Orificed valve option
• Custom shapes and configurations
Note: Some options may not be standard configurations. Please contact the Quick Coupling Division for availability and delivery.
Markets:
• Industrial
• Construction
• Agriculture
• Transportation
• MRO
Features/Benefits:
• Allows the fluid to flow in only one direction, protecting the system from fluid back pressure
• Soft seated valve creates a leak free seal
• Fluorocarbon seal is standard
• Optional crack pressures are available on request
• Optional orificed valve allows metered flow when the valve is closed. Orifice bore size is determined by application requirements.
• Custom shapes and configurations can integrate special features to reduce the number of components and potential leak points in a system
Applications:
• Industrial, mobile, and construction equipment
• Restrictor Check Circuit
• High/Low Pump Circuit
• Slow Advance/Rapid Return Circuit
• Oil Cooler By-Pass Circuit
• Sequence Circuit
• Pilot Pressure Circuit
• Accumulator Circuit -
Hard Seat In-Line Check Valves (3000 psi) Low Pressure Drop,...
CV Series Check Valves (3,000) psi are in-line unidirectional valves that have a two piece modular design. The larger body results in less pressure drop and increased performance. These check valves have standard spring crack pressures of 5 and 65 psi. The CV Series are available in a range of sizes up to 1"" and flow capacities to 100 gpm.
Check valves are important components that are often overlooked when building a fluid system. A check valve can optimize system performance in the following ways:
• Ensure hydraulic fluid flows in only one direction
• Eliminate potential damage from back pressure
• Isolate sections of a system or system components
Basic check valve construction consists of a valve body with an inlet and an outlet port. Inside, a moveable poppet valve is controlled by spring pressure. In most cases the valve is normally closed, opening when the fluid pressure is greater than the spring force (crack pressure), thus allowing the fluid to flow in only one direction. When reverse flow attempts to enter though the outlet the poppet closes and flow through the valve is stopped.
Hard seat check valves utilize a durable metal to metal seal to withstand high flow surges and provide longer service life.
Technical Characteristics:
• Sizes: 1/4”to 1""
• Material: Steel
• Inlet Port Ends: Male UNF, Male UN
• Outlet Port Ends: Male UNF, Male UN, Male UNS
• Fitting Styles: Male Flare Inlet to Male Flare Outlet, Male O-Ring Boss Inlet to Male Seal-Lok Outlet
• Fitting O-ring Material: Nitrile
• Optional crack pressures available
• Orificed valve option
• Custom shapes and configurations
Note: Some options may not be standard configurations. Please contact the Quick Coupling Division for availability and delivery.
Markets:
• Industrial
• Construction
• Agriculture
• Transportation
• MRO
Features/Benefits:
• Allows the fluid to flow in only one direction, protecting the system from fluid back pressure
• All steel construction
• Low pressure drop for increased performance
• Poppet valve is heat treated to help prevent galling and damage from shocks and surges
• Optional crack pressures are available on request
• Optional orificed valve allows metered flow when the valve is closed. Orifice bore size is determined by application requirements.
• Custom shapes and configurations can integrate special features to reduce the number of components and potential leak points in a system
Applications:
• Industrial, mobile, and construction equipment
• Restrictor Check Circuit
• High/Low Pump Circuit
• Slow Advance/Rapid Return Circuit
• Oil Cooler By-Pass Circuit
• Sequence Circuit
• Pilot Pressure Circuit
• Accumulator Circuit -
Hard Seat In-Line Check Valves (3000 psi) Up to 2” Size, One...
DC Series Check Valves (up to 3,000 psi) have a metel to metal hard seat design with a one piece body and all steel construction. Both inlet and outlet ports have female end fittings. These are in-line unidirectional valves with standard spring crack pressures of 1, 5, and 65 psi. The DC Series have low pressure drop and are available in a wide range of sizes up to 2"" and flow capacities to 300 gpm.
Check valves are important components that are often overlooked when building a fluid system. A check valve can optimize system performance in the following ways:
• Ensure hydraulic fluid flows in only one direction
• Eliminate potential damage from back pressure
• Isolate sections of a system or system components
Basic check valve construction consists of a valve body with an inlet and an outlet port. Inside, a moveable poppet valve is controlled by spring pressure. In most cases the valve is normally closed, opening when the fluid pressure is greater than the spring force (crack pressure), thus allowing the fluid to flow in only one direction. When reverse flow attempts to enter though the outlet the poppet closes and flow through the valve is stopped.
Hard seat check valves utilize a durable metal to metal seal to withstand high flow surges and provide longer service life.
Technical Characteristics:
• Sizes: 1/4” to 2""
• Material: Steel
• Inlet Port Ends: Female NPSF, Female UNF, Female NPTF, Female UN
• Outlet Port Ends: Female NPSF, Female UNF, Female NPTF, Female UN
• Optional crack pressures available from 1 to 200 psi in 5 psi increments
• Orificed valve option
• Custom shapes and configurations
Note: Some options may not be standard configurations. Please contact the Quick Coupling Division for availability and delivery.
Markets:
• Industrial
• Construction
• Agriculture
• Transportation
• MRO
Features/Benefits:
• Allows the fluid to flow in only one direction, protecting the system from fluid back pressure
• Low pressure drop
• metal to metal hard seat provides longer life and is durable for high flow surges
• Custom shapes and configurations can integrate special features to reduce the number of components and potential leak points in a system
• Optional crack pressures are available on request
• Optional orificed valve allows metered flow when the valve is closed. Orifice bore size is determined by application requirements.
Applications:
• Industrial, mobile, and construction equipment
• Restrictor Check Circuit
• High/Low Pump Circuit
• Slow Advance/Rapid Return Circuit
• Oil Cooler By-Pass Circuit
• Sequence Circuit
• Pilot Pressure Circuit
• Accumulator Circuit -
Soft Seat In-Line Check Valves Up to 2” Size, Steel /...
S6C and 3C Series Check Valves (up to 6,000 psi) are soft seat, zero leakage poppet check valves with a two piece construction. The two piece construction allows for a variety of end fitting combinations.
These check valves have various standard crack pressures and flow rates up to 175 gpm. The S6C & 3C Series valves are available in a range of sizes and steel or stainless steel materials for flow capacities up to 175 gpm.
Check valves are important components that are often overlooked when building a fluid system. A check valve can optimize system performance in the following ways:
• Ensure hydraulic fluid flows in only one direction
• Eliminate potential damage from back pressure
• Isolate sections of a system or system components
Basic check valve construction consists of a valve body with an inlet and an outlet port. Inside, a moveable poppet valve is controlled by spring pressure. In most cases the valve is normally closed, opening when the fluid pressure is greater than the spring force (crack pressure), thus allowing the fluid to flow in only one direction. When reverse flow attempts to enter though the outlet the poppet closes and flow through the valve is stopped.
Soft seat check valves have an O-ring or similar elastomeric seal between the poppet and body for improved leak resistance. The soft seat design is most compatible with ""clean” systems and is not indented for use in systems that have high surge flow. The seal material dictates the temperature range of the valve.
Technical Characteristics:
• Sizes: 1/4”to 2”
• Materials: Steel, Stainless Steel, Brass
• Seal Material: Fluorocarbon
• Standard Crack Pressures (psi): 5, 15, 25, 65
• Inlet Port Ends: Male NPT, Male 37 degree flare, Male Face Seal, Female NPTF, Female SAE, Female British Parallel BS 2779
• Outlet Port Ends: Male NPT, Female NPTF, Female SAE, Male SAE 37 degree Flare, Male Face Seal, Female British Parallel BS 2779
• Optional crack pressures available
• Orificed valve option
• Custom shapes and configurations
Note: Some options may not be standard configurations. Please contact the Quick Coupling Division for availability and delivery.
Markets:
• Industrial
• Construction
• Agriculture
• Transportation
• MRO
Features/Benefits:
• Allows the fluid to flow in only one direction, protecting the system from fluid back pressure
• Soft seated valve creates a leak free seal
• Fluorocarbon seal is standard
• Optional crack pressures are available on request
• Optional orificed valve allows metered flow when the valve is closed. Orifice bore size is determined by application requirements.
• Custom shapes and configurations can integrate special features to reduce the number of components and potential leak points in a system
Applications:
• Industrial, mobile, and construction equipment
• Restrictor Check Circuit
• High/Low Pump Circuit
• Slow Advance/Rapid Return Circuit
• Oil Cooler By-Pass Circuit
• Sequence Circuit
• Pilot Pressure Circuit
• Accumulator Circuit -
Fuel Line Check Valves - Low Pressure (250 psi), Full Flow...
2600 Series Check Valves have a spring-loaded, trapdoor style valve. The valve opens when system pressure approaches 1/2 psi to permit full flow with low pressure drop. As system pressure is relieved, the valve closes, retaining fluids upstream.
These in-line check valves are designed with a low crack pressure spring especially for diesel and gasoline engine fuel lines. The 2600 Series are available in two sizes and can be used in low pressure air, liquid or gas systems.
Technical Characteristics:
• Sizes: 1/4”, 3/8”
• Material: Aluminum
• Port Ends: Male NPTF
Markets:
• Construction
• Mobile Equipment
• Truck
Features/Benefits:
• Lightweight corrosion resistant aluminum construction
• Swing style valve allows full flow with low pressure drop
• 1/2 psi maximum crack pressure for use in low pressure air, liquid, or gas systems
Applications:
• Diesel and gasoline engine fuel lines
• Externally mounted oil filters and coolers
• Transmission fluid lubrication lines -
SAE Non return valves
Parker non-return valves with an ISO 8434-2 (Triple-Lok®) or 8434-3 (O-Lok®) connection offer a wide range of sizes, male threads and cracking pressures, making them very flexible.
The principle of a two-part non-return valve with an integrated soft sealing element has been proven by many applications in the market.
This reliability is the reason for its successful use in applications with Triple-Lok® (37° flare) or O-Lok® (O-Ring face seal).
Parker non-return valves are available with Cr(VI)-free surfaces. The broad product range goes from sizes 4 to 24 (6 mm to 38 mm O.D.); UNF, BSPP and metric male threads are available. The cracking pressures are from 0.2 to 6 bar. The maximum flow velocity is 8 m/sec. The nominal pressure PN: Triple-Lok® up to PN 350 bar and O-Lok® up to PN 400 bar.
Markets:
• Automotive
• Defence
• Energy
• Environment
• Industrial
• Infrastructure
• Machine Tools
• Materials Handling
• Mobile
• Oil and Gas
• Power Generation
• Process
• Transportation
• Water
Applications:
• Suitable for general hydraulic applications.
Features/ benefits of SAE non-return valves:
• The precise functioning of Parker SAE non-return valves has been proven a million times over and stands for the reliability of this product range.
• Combined soft and metal sealing – leak-free due to soft sealing at cone and metal-supported sealing at cone – extends the safety of the product and the entire hydraulic application.
• The usage of Parker SAE non-return valves is flexible due to the wide range of cracking pressures available.
• For yet more applications, internal parts in stainless steel with FPM are also available.
• The wide range of male threads also increases the number of potential applications. -
Zawory zwrotne Ermeto DIN
Oferta zaworów zwrotnych marki Parker o ciśnieniu znamionowym maks. PN 420 barów obejmuje wiele różnych wariantów, dzięki czemu jest bardzo elastyczna.
Gama różnorodnych typów zaczyna się od wersji RHD z przyłączem rurowym na obu końcach, następnie są wersje RHV/RHZ z przyłączem rurowym do króćca z gwintem zewnętrznym, RHDI z gwintem wewnętrznym na obu końcach, RVP z kartridżami zaworowymi, aż do wersji I-TL z zaworowymi częściami wewnętrznymi.
Zawory zwrotne są dostępne w wersji ze stali z powierzchnią niezawierającą sześciowartościowego chromu, ze stali nierdzewnej i z mosiądzu. Na życzenie dostępne są uszczelnienia z NBR lub FKM.
Wszystkie zawory zwrotne firmy Parker są zbudowane pod kątem zapobiegania zanieczyszczeniom.
Zawory zwrotne firmy Parker mogą być stosowane do oleju hydraulicznego, trudnopalnych płynów hydraulicznych (z wyjątkiem typów HFC: do typów HFD; niezbędne są uszczelnienia z FKM). Poddane próbie ciśnieniowej powietrzem. Nie nadają się do pary, gazów palnych/wybuchowych ani tlenu.
Rynki:
• Motoryzacja
• Militarny
• Energia
• Ochrona środowiska
• Przemysł
• Infrastruktura
• Obrabiarki
• Transport materiałów
• Mobilny
• Przemysł naftowy i gazowy
• Wytwarzanie energii elektrycznej
• Przetwarzanie
• Transport
• Instalacje wodne
Zastosowania:
• Nadaje się do ogólnych zastosowań hydraulicznych.
Cechy/zalety zaworów zwrotnych:
• Precyzyjne działanie zaworów zwrotnych firmy Parker zostało udowodnione już miliony razy i świadczy o niezawodności tego asortymentu produktów.
• Połączenie uszczelnienia miękkiego z metalowym — szczelność dzięki miękkiemu uszczelnieniu na stożku oraz wsparciu stożka metalem — zwiększa bezpieczeństwo produktu oraz całego hydraulicznego zestawienia.
• Zawory zwrotne firmy Parker zapewniają elastyczność pod względem użytkowania dzięki szerokiej gamie elementów.
• Możliwych jest jeszcze więcej zastosowań, ponieważ dostępne są również części wewnętrzne ze stali nierdzewnej z FPM.
• Wszystkie zawory zwrotne firmy Parker są zbudowane pod kątem zapobiegania zanieczyszczeniom, co oznacza wyższą jakość i niezawodność tych produktów.