Zawory regulacji przepływu
Zawory regulacji przepływu firmy Parker są komponentami układów zasilania wodą, powietrzem lub olejem hydraulicznym. Są niezbędne do sterowania ciśnieniem, kierunkiem oraz szybkością przepływu w przewodach hydraulicznych i pneumatycznych. Wysoko zaawansowane produkty firmy Parker spełniają wszelkie wymagania i standardy branżowe, a jakością i technologią wykonania wyróżniają się na tle konkurencji.
Zawory regulacji przepływu Parker
W układach automatyki oraz zdalnego sterowania elementem wykonawczym jest zawór do regulacji przepływu. Znajduje zastosowanie w wielu gałęziach przemysłu, w tym ciepłownictwie, systemach wentylacyjnych lub klimatyzacyjnych, a także przemyśle produkcyjnym lub magazynowym. Dostępnych jest wiele typów zaworów, dzielonych ze względu na konstrukcję wykonania, bezpośredniego działania oraz zasilanych energią zewnętrzną. Zawory regulacji przepływu firmy Parker oferują wszystkie typy i możliwości produkcyjne, dostosowane do wymagań danego systemu. Zaawansowana konstrukcja pozwoliła również na wyeliminowanie problemów takich jak kawitacja, hałas i obniżenie ryzyka erozji.
Solidny zawór z regulacją przepływu
Zawór z regulacją przepływu może być zaprojektowany tradycyjnie do umożliwienia przepływu w układzie z punktu wejścia do wyjścia, zatrzymania i przełączenia kierunku przepływu, lub konfiguracyjny do jednoczesnego przejścia przez inną sekcję układu, lub nawet pełniącego funkcję zarówno zaworu jak i siłownika. Tradycyjne zawory proponowane przez firmę Parker umożliwiają swobodny przepływ materiału w jednym kierunku oraz kontrolowany przepływ w kierunku przeciwnym. Bezkonkurencyjna konstrukcja zapewnia prawie całkowite ograniczenie wycieku oraz szeroki wybór rozmiarów w standardzie.
Bezpieczne zawory z regulacją przepływu
W portfolio producenta są też bardziej zaawansowane zawory do regulacji przepływu, z opatentowanymi technologiami kompensacji zużycia uszczelek, lub wspomniane wyżej zawory osiowe, będące jednocześnie zaworem i siłownikiem w układzie. Nieodpartymi korzyściami stosowania tych produktów jest bezpieczeństwo, możliwość optymalizacji procesu oraz trwałość i niezawodność. Należy też zwrócić uwagę na wszechstronność stosowania, wydajność oraz szeroki zakres wartości roboczych temperatury i ciśnienia. Dzięki dostępności wielu konfiguracji i typów zaworów możliwe jest spełnienie wszystkich wymagań w instalacji systemu. Kompleksowa oferta, niezawodność, dostosowanie do wielu branż i możliwość uzyskania doskonałej wydajności przy różnych wartościach ciśnienia i temperatury to idealne rozwiązanie do zastosowań w projektowanym układzie regulacji przepływu.
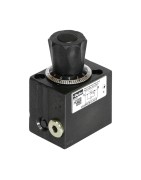
-
Pressure Compensated Priority Flow Control Valves
Priority style pressure compensator flow control valves maintain constant priority flow to one leg of a circuit regardless of any changes in load or inlet pressure. Once the priority flow is satisfied, any excess flow may be used in other parts of the circuit.
The valve consists of a control orifice housed within a spring biased compensator spool. This orifice may be fixed or adjustable. The priority port is normally open while the bypass port is normally closed. As flow enters the inlet port of the cartridge, it passes through the control orifice. A pressure differential is created across the compensator spool. If the inlet flow exceeds the setting of the valve, the force produced by this pressure differential exceeds the spring force and shifts the compensator spool; opening up the bypass port, and bypassing the excess flow. If the load pressure at the bypass port is greater than the load pressure at the priority port, the compensator spool will further shift restricting the priority flow to that of the valve setting. However, caution should be taken if the priority gets blocked so that no flow can pass through the control orifice, the compensator spool will shift, blocking the bypass port and allowing inlet pressure to go to full system relief pressure. It is common to place an external relief valve downstream of the priority flow port to prevent a no flow condition.
Parker offers four styles of Pressure Compensated Priority Flow Controls ranging from 4 to 24 gallons per minute. Parker’s offering is as follows:
J02D3 - 4 gpm rated flow, 6000 psi, and is available with adjustment styles of Screw adjust, Knob adjust, and a Tamper resistant cap. Customers can request specific flow settings. Buna and Fluorocarbon seals available.
FP101 - 8 gpm rated flow with 15 gpm max inlet, 3500 psi, with adjustment styles of Fixed, Knob, and Screw. Nitrile and Fluorocarbon seals available.
J04D3 - 12 gpm rated flow, 6000 psi, and is available with adjustment styles of Screw, Knob, and Tamper Resistant cap. Customers can request specific flow settings. Nitrile and Fluorocarbon seals available.
J1A125 - 24 gpm rated flow, 5000 psi, and is available with adjustments styles of Screw, Knob, and Tamper Resistant. Customers can request specific flow settings. Nitrile and Fluorocarbon seals available.
Pressure compensated priority flow control valves are typically used in meter-in type circuits like steering (mobile equipment) or actuator speed control (industrial equipment) where a fixed displacement pump is being used. -
Pressure Compensators/Control Elements
Inlet flow (upstream of the orifice or flow control valve) is split with one portion going to the compensator port inlet, the other portion passes through the orifice, or flow control valve, to the supply port. As pressure drop across the orifice reaches the selected compensator pressure drop, the higher pressure (pre-orifice) starts to shift the compensator spool into a throttling position. The valve works to maintain a constant pressure drop across the orifice. Using this type of valve allows greater flexibility in design and flows as these valves can flow as much as 40 gallons per minute.
Compensator valves are used in circuits where a constant flow is desired regardless of upstream or downstream loads. As the pressure downstream of the compensator increases, the valve is forced open to maintain the constant pressure drop across the fixed, or adjustable, orifice. Conversely, if the pressure increases upstream of the orifice, the compensator valve will be forced closed to maintain the constant pressure drop across the orifice.
Parker offers two sizes of restrictive type of pressure compensators ranging in flows from 10 gallons per minute to 40 gallons per minute, and pressures up to 3500 psi.
FCR101 - 10 gpm rated flow (38 lpm), 3500 psi. Differential pressure ranges of 40, 80, and 160 psi and is available with Nitrile or Fluorocarbon seals.
FCR161F - 40 gpm rated flow (150 lpm), 3500 psi. Differential pressure ranges of 40 and 160 psi and is available with Nitrile or Fluorocarbon seals.
Pressure compensators can typically be found in applications such as conveyor circuits in saw mills, or lumber yards, steel mills, or cylinder control circuits in steel mills or foundries. -
Pressure Compensated Flow Control Valves
Parker offers a wide range of spool type restrictive pressure compensated flow controls to allow for speed control of motors, cylinders, and rotary actuators. Pressure compensation allows the flow devices to maintain a constant flow even with varying loads and inlet pressures. Tunable and fully adjustable versions are available with screw or knob adjusters that can be made tamper resistant with the addition of an optional cap.
FR101 is a tunable pressure compensated flow regulator which compensates for varying loads and pressures in one direction but in the other direction flow is metered across a fixed orifice but not compensated. In order to allow pressure compensated flow control in one direction and full free flow in the opposite direction, Parker offers an internal check valve in the tunable FC101 cartridge. Because both versions are tunable and not fully adjustable, the valve will need to be specified with the appropriate flow range for the application. Changes in flow rates are achieved by mechanically varying the spring force acting on a spool that has a fixed orifice and metering compensator.
J02E2, J04C2, and J04E2 are fully adjustable pressure compensated flow regulators. In the opposite flow direction they only meter through a fixed orifice and do not compensate. In order to achieve fully adjustable pressure compensated flow control while allowing reverse full flow, the FA101 includes an internal check valve to bypass the compensator and metering orifice.
Typical applications and industries include Accumulator Bleed-off, Motor Speed Control, Cylinder Speed Control, Bleed-Off Flow, Power Units, Oil and Gas, Material Handling, Construction, Drills, Presses, Mixers, Agriculture, Balers, Combines, etc. -
Needle Flow Control Valves
Needle valves offer economical solutions for applications that require basic adjustable control of hydraulic flow. The effective orifice size inside the valve is varied with screw or knob adjustments and the valve can be made tamper resistant with the addition of an optional cap. Shutoff can be achieved when the valve is adjusted completely closed. Once the adjustment is set, the valve acts as a fixed orifice. Like all fixed orifices, any changes in pressure will cause changes in flow. If constant flow is required regardless of system or load pressure, please consider Parker’s pressure compensated flow controls.
Parker’s J02A2, NVH081, NVH101, and J06A2 cartridges are basic 2-port needle valves with fine adjustment options available. The orifice will meter in both directions, but flow from port 2 to 1 is preferred. If unrestricted reverse flow is required, an additional check valve will need to be used with these needle valve versions.
Parker also offers J02B2, FV101, and FV102 needle valves with internal reverse free flow checks in order to reduce manifold size and component quantities. Typical applications and industries include Accumulator Bleed-off, Motor Speed Control, Cylinder Speed Control, Bleed-Off Flow, Power Units, Oil and Gas, Material Handling, Construction, Drills, Presses, Mixers, Agriculture, Balers, Combines, etc. -
Flow Divider/Combiner Valves
Each of Parker’s four flow divider/combiner versions can be used as a divider or combiner depending on the direction of flow. Two inter-locking spools allow for pressure compensated flow division and combination to be proportioned based on the selected ratio and flow range. When port 3 is supplied flow it is divided by a fixed ratio to work ports 2 and 4. For example, if a 50:50 ratio is selected half of the flow will exit port 2 and the other half will exit port 4. If the actuators have the same area or displacement they will operate at the same speed. If different actuator speeds are required, alternative ratios can be selected to supply different flows to each port. Ratios other than 50:50 can allow speed synchronization of two actuators that have different areas or displacements. The flow to each actuator port is proportional to the inlet flow based on the flow division ratio.
When used as a combiner, flow applied to ports 2 and 4 is combined and the total flow exits port 3. The flow from the combiner inlet ports is pressure compensated and the flow ratio determines how much flow is allowed from each port. Just like the divider mode, the combiner mode allows for actuator speed variation or synchronization.
Typical flow accuracy is +/- 10% between ports 2 and 4. When trying to synchronize 2 cylinders or motors, cross-port relief valves or balancing orifices can be used to help maintain tighter synchronization.
Parker’s FDC101, L04A3, L06A3 and L1A300 flow divider/combiners operate in the same manner with each having a different maximum flow and multiple standard ratios and flow ranges. Typical applications and industries include cylinder synchronization, motor synchronization, flow partitioning, transmission differentials, construction, oil and gas, material handling, military, grinders, mixers, drills, snow blowers, etc. -
Priority Pressure Compensators
Parker offers two styles of Priority Pressure Compensators, ranging in flows from 10 to 20 gallons per minute, and pressure capabilities of 3500 psi and 5500 psi. Flow through the external orifice (fixed or variable) enters the supply port and produces a pressure drop across the compensator spool. When the inlet pressure exceeds the initial setting of the valve, the force produced by the pressure differential across the spool exceeds the spring force and shifts the compensator spool to throttle, or restrict, the flow, thus maintaining constant flow through the priority port. The excess flow is bypassed out to the system to be used by another function, or back to the system reservoir. Flow out the regulated port must be maintained for bypass flow to continue. For this reason, common practice dictates a pressure control (relief) be installed in the priority line.
Parker offers the following styles of Priority Pressure Compensators:
FCP101 - Up to 10 gallons per minute priority flow rate (38 lpm), 15 gallon per minute maximum inlet flow (56 lpm), 3500 psi. Available with differential pressure settings of 40, 80, and 160 psi. Nitrile and Fluorocarbon seals available.
FCPH121 - Up to 20 gallons per minute priority flow rate (75 lpm), 25 gallons per minute maximum inlet flow (95 lpm), 5500 psi. Available with fixed (customer specified) or variable differential pressure settings. Adjustments are knob or screw adjust, with a tamper resistant cap available.
Priority Pressure Compensators are used where the design calls for constant flow to a particular segment of the circuit, regardless of upstream or downstream pressure (load) changes. A common application is for speed control on a conveying system. Should the load on the conveyor increase, the pressure increases at the compensator and the valve modulates to maintain the desired pressure differential across the valve. This modulation allows more flow to pass through the valve thus maintaining a constant desired speed. Conversely, should the load on the conveyor decrease, the opposite happens and the compensator modulates, restricting some flow to maintain the desired pressure differential, thus providing constant speed.
Parker Priority Pressure Compensators may be found in steering circuits, conveying systems, lift/lower systems in markets such as mobile/agricultural companies, steel or lumber mills, or off-highway mobile equipment. -
3 Way Flow Control Proportional Valves
Parker’s proportional flow control valves provide electronically variable flow control. Varying coil current will create a proportional flow out to an actuator allowing control of speed, acceleration, and deceleration. AC and DC coil options are available, along with a wide range of connection types. Current Controlled Pulse Width Modulation (PWM) valve drivers are preferred as they adjust for variations in coil temperature and also provide the ability to apply a dither frequency.
Priority Bypass is the last type of proportional flow control manufactured by Parker. Two sizes are available and the largest version is capable of flows up to 20 GPM (75 LPM.) Priority bypass flow controls are 3-way spool-type valves that consist of an inlet port, a priority port, and a bypass port. When no current is applied to the coil, all inlet flow exits the bypass port. As current is increased the spool shifts allowing a proportional amount of pressure compensated flow to the priority port while bypassing any remaining flow to the bypass port. Bypass flow is not allowed unless the priority ports has achieved the commanded proportional flow rate based on the input current. This allows for a priority of flow to one part of a circuit regardless of varying load conditions in both parts of the circuit. Typical priority applications include braking and steering.
Combined with Parker’s wide range of Coil options, the extensive proportional flow control offering allows for application specific solutions in the most demanding applications and markets including: Power Units, Oil and Gas, Material Handling, Construction, Drills, Presses, Mixers, Agriculture, Balers, Combines, Double Acting Cylinder Control, Bi-Direction Motor Control, Circuit Selectors, Skid-Steers, etc. -
Pressure Compensated Proportional Poppet Valves
Parker Hydraulic Cartridge Systems Division combines Parker’s precision ground poppet and SuperCoil technology with a newly patented integral compensator design, bringing you a flow control product with best in class repeatability and a truly exceptional level of control.
In conditions of varying load, the FAPC series maintains predictable and repeatable performance through the introduction of our new fully integrated compensator. Built directly into the FAPC series valves, the innovative new compensator maintains a tight seal for load holding without any requirement for additional sealing. When open, the compensator responds to changing load conditions independently. With no seal friction to overcome, the FAPC valve maintains the repeatable and predictable performance customers can rely on. This additional feature eliminates the need for complex programming algorithms, and any requirement for an external compensator to improve the operator’s control.
• Excellent metering capability and control throughout the full flow range
• Reduced drift
• Low leak control (less than 5 dpm)
• Modular solution to applied problem
• Low leak compensator, requiring no additional seals, results in very low hysteresis (< 10%)
• Maintains constant flow regardless of load condition
• Patented integrated low leak compensator
How it works:
The FAPC utilizes a control current to proportionally raise and lower a poppet creating a variable orifice allowing flow to pass through from the inlet to the outlet. There is also a low leak integral compensator that responds to load changes in the hydraulic circuit by varying the outlet orifice, metering the flow rate that can be passed through and maintaining constant flow independent of load conditions.
The fully compensated FAPC is rated to flows up to 115 LPM (22 GPM).
Common markets and applications include the aerial markets (boom raise/lower), fork lift (lift/lower) and vehicle lift. -
Proportional Poppet Valves
Parker Hydraulic Cartridge Systems Division combines Parker’s precision ground poppet and SuperCoil technology with a newly patented integral compensator design, bringing you a flow control product with best in class repeatability and a truly exceptional level of control.
Parker’s innovative new flow control product is available in a non-compensated (FAP) format. The FAP series offers repeatable and accurate operation throughout the full control range of the valve. Available in flow ranges from 7 gpm to 31 gpm and pressures up to 3000 psi, the FAP proportional flow control poppet valves come both normally open and normally closed. The FAP utilizes a control current to proportionally raise and lower a poppet creating a variable orifice allowing flow to pass through from the inlet to the outlet.
• Excellent metering capability and control throughout the full flow range
• Reduced drift
• Low leak control (less than 5 dpm)
• Modular solution to applied problem
• Improved control throughout the control range
Common markets and applications include the aerial markets (boom raise/lower), fork lift (lift/lower) and vehicle lift. -
2 Way Flow Control Proportional Valves
Parker’s selection of 2-way flow control proportional valves provide repeatable and precise controls to circuits requiring proportional flow control through a single line in a normally-open or normally-closed configuration. These valves are capable of handling flows up to 227 lpm (60 gpm) and pressures as high as 210 bar (3000 psi). These valves can achieve pseudo pressure compensation in both normally-open and normally-closed versions due to the pressure drop across the spool orifices, but an external compensator can also be used if finer control is required, making these valves ideal for variable applications that need exact control and do not demand the exact same flow every time a function is operated. Parker’s 2-way flow control proportional valves pair well with any Current Controlled Pulse Width Modulation (PWM) valve driver and can be used on a variety of mobile and industrial applications within the agriculture, construction, and manufacturing markets.
Markets:
• Agriculture
• Construction
• Material Handling
• Miscellaneous Industrial
• Miscellaneous Manufacturing
• Miscellaneous Mobile
Features/Benefits:
• Low hysteresis
• Hardened working parts for maximum durability
• All external parts zinc plated
Applications:
• Applications requiring precise controls
• Variable flow applications
Additional Technical Insight:
Recommended to be used with a Current Controlled Pulse Width Modulation (PWM) valve driver. -
Flow Control Valve, Subplate Mounted Series PC*MS
Manatrol 2 way flow control valves series PM*CS for pressure compensated regulation of the flow. As a consequence of pressure changes, the set value can vary by ± 5 % within the tolerance range. Changes in viscosity and in temperature have the same effect and are to be observed.
The series PC*MS is additionally equipped with a built-in check valve for the return flow. -
2-drogowy zawór regulacji przepływu — seria GFG2
2-drogowe zawory regulacji przepływu serii GFG firmy Parker zapewniają stały przepływ niezależnie od wahań ciśnienia i temperatury. Model GFG można opcjonalnie wyposażyć we wbudowany zawór zwrotny zapewniający przepływ wsteczny.
Rynki:
• Przemysł
• Obrabiarki
Cechy/zalety:
• Natężenie przepływu kompensowane ciśnieniem — precyzyjne wykonywanie ruchów.
• Szeroki zakres różnych natężeń przepływu — umożliwia precyzyjną regulację.
• Krótki czas dostawy — brak konieczności magazynowania
• Przyłącze zewnętrzne (P) do blokowania przepływu z A do B.
• Opcjonalny zawór zwrotny przepływu wstecznego.
• Pokrętło z zamkiem bębenkowym (opcja S).
Zastosowania:
• Nadaje się do ogólnych zastosowań hydraulicznych
• Obrabiarki
Projekt:
2-drogowe zawory regulacji przepływu używane są z trójkątnym ogranicznikiem natężenia przepływu i następującym po nim kompensatorem ciśnienia. Ustawienie natężenia przepływu można zablokować przed nieuprawnionym przestawieniem (opcja S) za pomocą zamka bębenkowego w pokrętle regulacyjnym.
Funkcja:
Medium wpływa przez przyłącze A przez ogranicznik natężenia przepływu. Za ogranicznikiem natężenia przepływu znajduje się kompensator ciśnienia. Krawędzie sterujące tworzą cztery promieniowe otwory w grzybku, które są całkowicie otwarte do przyłącza B w położeniu neutralnym. Opcjonalnie przepływ z A do B można zablokować przez zewnętrzne ciśnienie sterujące wysłane do przyłącza P (opcja X). Można to wykorzystać, aby uniknąć niezamierzonych początkowych ruchów siłowników. Regulacja natężenia przepływu odbywa się za pomocą pokrętła ręcznego o kącie regulacji 270°. -
2-Way Variable Flow Control Valve - Series 2F1C
2-way flow control valves series 2F1C provide pressure and viscosity compensated flow from port A to port B. The counter direction is blocked (standard) or can be open via an integral reverse flow check valve (optional).
Features/benefits:
• 2-way flow control valve
• Subplate mounting according to ISO 6263
• Excellent fine adjustment
• Adjustable response time
• Closed in neutral position
• Optional reverse flow check valve
• 2 sizes, NG10 (3/8“), NG16 (3/4“)
Function
The compensator spool is located in front of the metering spool. The metering spool is closed in the neutral position to avoid undesired initial actuator motion. The oil flow to open the metering spool has to pass a needle valve (not shown in the sectional drawing). The needle valve can be adjusted from the front panel to set the response time of the 2F1C.
The metering spool is adjusted by the main control knob.
The key lock has three positions:
• Lock: Adjustment is locked.
• Adjust: Full adjustment is permitted.
• Trim: Fine adjustment of ±5 % is possible. -
Throttle Check Valve, Subplate Mounted Series FS
Manatrol throttle check valves series FS allow the adjustment of the flow for a defined direction.
A 2 stage needle allows for very exact setting of smaller flow rates with the first 3 rotations of the adjustment knob. After 3 more rotations, the valve is completely open. The valve setting can be locked by a locking screw. -
DUR*L06 2-Way Proportional Flow Control Valve
Proportional flow control valves of the series DUR*L06 are used to generate pressure-compensated flow from A to B. The valve is equipped with a built-in check valve for the return flow.
For meter-in and meter-out control of an actuator a rectifier plate can be used.
Function
When solenoid current is applied, the metering spool opens against the reset spring and the flow is regulated by the pressure compensating spool to port B.
With the aid of the pressure compensating spool, the pressure drop is held constant on the metering window. Thus pressure load changes are compensated, and the oil flow remains constant.
In combination with the digital electronic module PCD00A-400 the valve parameters can be saved changed and duplicated.
Technical features:
- Low hysteresis
- High reproducibility
- Load-independent oil flow
- Bypass check valve
- Mounting pattern to ISO 6263
- 5 flow rates -
Proportional Throttle Valve Series F5C
Proportional throttle valves series F5C allow to adjust the flow in proportion to the input signal. The combination of the F5C with pressure compensators R5A or R5P serves as a flow control valve - providing load compensated flow. The F5C is offered with two types of response time:
- standard 350 ms at 1 l/min pilot flow
- code A 250 ms at 2 l/min pilot flow
Features:
- Spool type proportional throttle valve
- SAE61 flange
- Maximum flow 380 l/min
- 3 sizes, SAE 3/4“, 1“, 1 1/4“
- Load compensated flow in combination with R5A and R5P -
R5P 3-Port Pressure Compensator
Direct operated 3 way pressure compensators series R5P can be combined with any type of fixed or adjustable flow resistor (throttle) to provide a load compensated flow.
The combination with the proportional throttle valve F5C serves as a compact 3 way flow control unit in SAE flange design. The R5P is typically used as meter-in compensator in front of the flow resistor.
The R5P is additionally equipped with a pressure relief pilot, that controls the compensator cartridge and operates as system pressure relief valve. The R5P*P2 provides a proportional relief function.
Features:
- Seated type 3 way pressure compensator
- SAE61 flange
- 8.4 bar control pressure
- Pressure relief function (optionally proportional)
- With optional vent function
- 3 sizes, SAE 3/4“, 1“, 1 1/4“
- Load compensated flow in combination with F5C -
Zawór regulacji przepływu do montażu w linii — seria F
Zawory regulacji przepływu montowane w linii serii F firmy Parker wyposażone są w precyzyjne lub standardowe iglicowe zawory dozujące do regulacji przepływu oraz konstrukcję zaworu grzybkowego z pełnym prowadzeniem umożliwiającą swobodny przepływ w odwrotnym kierunku. Nasza bezkonkurencyjna konstrukcja zaworu grzybkowego z pełnym prowadzeniem eliminuje bicie osiowe i nieregularny ruch, jakie zwykle mogą wystąpić w przypadku kulowych zaworów zwrotnych. Standardowy grzybek z miękkim gniazdem w tych zaworach zwrotnych zapewnia prawie zerowy poziom wycieków i dostępny jest standardowo w rozmiarach do 1/2 cala. Opcje obejmują zawory dozujące olej i powietrze do układów hydraulicznych i pneumatycznych.
Rynki:
• Automatyka przemysłowa
• Obrabiarki
• Przemysł morski
• Transport materiałów
• Górnictwo
• Przemysł
• Produkcja
• Formowanie
• Przemysł naftowy i gazowy
• Wytwarzanie energii elektrycznej
• Fabryki pojazdów
Cechy/zalety:
• Opcje przyłączy obejmują ISO 6149, NPT, BSPP, BSPT i SAE
• Oferowane materiały to mosiądz, stal i stal nierdzewna
• Dostępna opcja odporna na ingerencję
• Wyjątkowy kolorowy pasek „Colorflow" zapewnia dokładne wizualne wskazanie nastawy.
• Śruba ustalająca blokuje zawór na żądanej nastawie.
Zastosowania:
• Nadaje się do ogólnych zastosowań hydraulicznych -
General Purpose Check Valve - C Series
As a part of the Colorflow® Family, Parker Check Valves have fully guided poppets. Our superior, fully guided poppet design eliminates wobble and erratic travel that can commonly occur with less durable ball check type construction. C Series Check Valves are available from 1/8” to 2”. The standard soft seat poppet on these check valves provide near zero leakage and come standard in sizes up to 1/2”.
The C Series Check Valve port options include ISO 6149, NPT, BSPP, BSPT and SAE. Material offerings are brass, steel and stainless steel. The steel C Series Check Valve comes standard with a black oxide finish.
These check valves can be found in numerous pneumatic, hydraulic or water applications including:
• Food processing
• Construction equipment
• Factory automation
• Power units
• Plastic molding
• Material handling
• Oil and gas
• Die cast
• Machine tools
• Car washes
• Paper mills
• Marine -
PC*K In-Line Pressure Compensated Valve
As part of the Colorflow Family, Parker PC Series Pressure Compensated Flow Control Valves have color rings that provide an accurate visual indication of valve adjustment. The PC Series Pressure Compensated Flow Control valve comes with an adjustable needle or with a factory set fixed flow rate. The adjustable setting can be secured with a standard set screw or a thumbscrew option that does not require additional tools. The PC Series valve is available in 6 sizes from 1/4” to 1 1/4”.
The PC Series Valve are available with NPT or SAE ports. Material offerings are steel and stainless steel. The steel version comes standard with black oxide finish. These pressure compensated valves can be found in numerous pneumatic, hydraulic or water applications including:
• Food process
• Construction equipment
• Factory automation
• Power units
• Plastic molding
• Material handling
• Oil & gas
• Die cast
• Machine tools
• Car washes
• Paper mills
• Marine -
Precision Needle Valve Series MVI
Series MVI cartridge-type needle valves are designed for installation in a precision-machined cavity made in the manifold of the machine.
These valves provide precise metering control and full shutoff of flow. An o-ring and backup ring installed on the cartridge fully isolate the inlet and outlet ports of the machined cavity from each other.
The exclusive “Colorflow” color-band reference scale on the valve stem is a great convenience and time-saver in setting the valve originally and in returning it to any previous setting. -
In-Line Pressure Compensated Valve Series PC*M
As part of the Colorflow Family, Parker PCM Series Pressure Compensated Flow Control Valves have color rings that provide an accurate visual indication of valve adjustment. The PCM Series Pressure Compensated Flow Control valve comes with an adjustable needle or with a factory set fixed flow rate. The adjustable setting can be secured with a standard set screw or a thumbscrew option that does not require additional tools. The PCMSeries valve is available in 6 sizes from 1/4” to 1 1/4”.
The PCM Series Valve are available with NPT or SAE ports. Material offerings are steel and stainless steel. The steel version comes standard with black oxide finish.
These pressure compensated valves can be found in numerous pneumatic, hydraulic or water applications including:
• Food processing
• Construction equipment
• Factory automation
• Power units
• Plastic molding
• Material handling
• Oil & gas
• Die cast
• Machine tools
• Car washes
• Paper mills
• Marine -
Constant Volume Priority Flow Control ValveSeries CFD
As a part of the Mobile Accessory Family, the Parker CFD Flow Divider divides pump hydraulic oil into two separate flows. One, the pressure compensated Controlled Flow (has Priority), and the other, a usable flow which is in excess of the Controlled Flow. The Controlled Flow rate is determined by the metering spool that is installed.
• The CFD is rated at 3000 PSI and the maximum recommend input flow is 20 GPM.
• The fixed Controlled Flow rate is available in six standard options ranging from 1 to 5 GPM.
• Standard porting options are SAE-10, 1/2” NPT, and 3/4” NPT. -
Priority Type Flow Control Series CFQ
As a part of the Mobile Accessory Family, the Parker CFQ Adjustable Flow Divider divides pump hydraulic oil into two separate flows. One, the pressure compensated Controlled Flow, and the other, a usable flow which is in excess of the Controlled Flow. Once the Controlled Flow demand is satisfied, the compensator spool shifts and passes Excess Flow to port EX. The EX flow can be used in a secondary circuit. Additionally, with the EX port plugged, the CFQ can serve as a 2 port restrictive type pressure compensated flow control.
• The CFQ is rated at 3000 PSI with SAE ports and the maximum recommend input flow is 35 GPM.
• The Controlled Flow rate has 3 adjustable ranges, from 0 to 8 GPM, 0 to 16 GPM, and 0 to 30 GPM, over 90 degree rotation of the adjustment lever.
• Standard porting options are 1/2” NPT and 3/4” NPT as well as SAE-10 and SAE-12.
When flow requirements are met at port “CF”, the compensator spool shifts to deliver excess flow to port “EX” for use in a secondary circuit.
The compensator maintains a constant differential pressure of less than 50 PSI (34.5 bar). With port “EX” plugged, the CFQ serves as a 2-port, pressure-compensated flow control. -
Flow Divider - PD Series
Series PD and PDC accessory valves are pressure compensated flow dividers. They are designed for applications where two separate hydraulic circuits are to be served from a single pump. The valve splits the flow in three ratios between the two hydraulic lines. Flow through the series PD flow divider cannot be reversed. Flow through the PDC flow divider can be combined in the reverse direction and synchronized in both directions.
Series PD and PDC flow dividers will divide the inlet flow to ±10% of the specified outlet flow when used within recommended capacities. In addition, many actuators can displace fluid different from the ratio of the divider. -
Priority Flow Control Series DC25
As a part of the Mobile Accessory Family, the Parker DC25A Adjustable Flow Divider divides pump hydraulic oil into two separate flows. One, the adjustable Controlled Flow (pressure compensated), and the other, Excess Flow which over and above the Controlled Flow. Once the Controlled Flow demand is satisfied, the compensator spool shifts and passes Excess Flow to port EF. The EF flow can be used in a secondary circuit. Additionally, with the EF port plugged, the DC25A can serve as a 2 port restrictive type pressure compensated flow control.
• The DC25A is rated at 3500 PSI and the maximum recommend input flow is 30 GPM.
• The Controlled Flow rate is adjustable from 1 to 26 GPM via 12 detented positions while rotating the adjustment knob over 360 degrees.
• Standard porting options are 1/2” NPT and 3/4” NPT as well as SAE-10 and SAE-12. -
Pressure Compensated ByPass Type Flow Control Valve -Series CFDA
As a part of the Mobile Accessory Family, the Parker CFDA Adjustable Flow Divider divides pump hydraulic oil into two separate flows. One, the adjustable pressure compensated Controlled Flow, and the other, Excess Flow which over and above the Controlled Flow. Once the Controlled Flow demand is satisfied, the compensator spool shifts and passes any Excess Flow to the Excess Flow port. The Excess Flow port is not a work port and must be returned to tank.
• The CFDA is rated at 2500 PSI and the maximum recommend input flow is 20 GPM.
• The Controlled Flow rate is adjustable from minimum to 15 GPM over 6 turns of the adjustment knob.
• Standard porting options are SAE-10, 1/2” NPT, and 3/4” NPT. -
PILOT OPERATED CHECK SANDWICH VALVESeries CP
Series CP pilot operated check valves are designed for maximum flow rates. The valves are typically used in combination with spool type directional control valves to ensure leak free positioning of the actuator. The inlet flow is free while the outlet flow is blocked. Pressure in the inlet line opens the check valve and allows free outlet flow.
• High life time.
• Check function in A, B or A + B.
• Available Sizes:
– CP05 – NFPA D05 / NG10 / CETOP 5
– CP5H – NFPA D05HE / NG10 / CETOP 5H
– CP07 – NFPA D07 / NG16 / CETOP 7
– CP08 – NFPA D08 / NG25 / CETOP 8 -
CHECK SANDWICH VALVE - CM SERIES
Parker’s CM series check valves provide an integral, full flow check valve in the pressure 'P' port, 'A' port, 'B' port, or the tank 'T' port of the directional valve. Reverse flow is blocked. The CM2 and CM3 sizes offer a combination P&T check version.
Markets
• Factory Automation
• Lumber & Wood
• Machine Tools
• Material Handling
• Miscellaneous Industrial
• Miscellaneous Manufacturing
• Miscellaneous Processing
• Molding
• Packaging Machinery
• Plastic Processing
• Primary Metal Refining Process
• Rubber & Tire Processing
• Vehicle Assembly Facilities
Features/Benefits
• Valve bodies are manufactured from steel which provides extra strength and durability for longer life
• Internal hardened steel components also provide longer life
• Positive shut-off is provided by a fully guided poppet and allows full flow in the unchecked position
• Parker CM sandwich style check valves can be used either on the 'P', 'A', 'B', 'T' ports, or combinations
• Large internal flow paths allow high flow at low pressure drop
Applications
• Suitable for general hydraulic applications -
Sandwich Throttle Check Valve - FM Series(AP)
Double-throttle check valves series FM in NG06 and NG10 are part of Parker's complete range of sandwich plate valves and provide high flow at low pressure drop for precise and energy-efficient processes. They ensure an easy configuration of conventional stack systems. Throttle and check valves are located in ports A and B.
Markets:
• Industrial
• Machine tools
Features/Benefits:
• Compact, proven design - ensures reliable operation in conventional stack systems
• Two types of metering needle design (FM2 and FM3) - enable to select the optimum throttle characteristics required to suit the application
• Large bypass check valves - allow high flow at low pressure drop
• Very good price-perfomance ratio
• Short delivery time - no warehousing necessary
• Four sizes:
- NG06 (CETOP 03 / NFPA D03)
- NG10 (CETOP 05 / NFPA D05)
Applications:
• Suitable for general hydraulic applications
• Machine tools
Function:
FM2 and FM3 can be used as meter-in or meter-out throttle by changing the mounting position.
The throttle check valve can also be used to influence the switching time of pilot operated directional valves. In this case, the valve is positioned between the pilot stage (CETOP 03, NG06) and the main stage (CETOP 05, NG10 up to CETOP 10, NG32).