Zawory logiczne
Parker logic valves (or logic elements) are screw-in type cartridge valves used in high flow, high pressure applications to control flow, pressure, or direction. These valves are controlled by smaller pilot valves to perform multiple functi
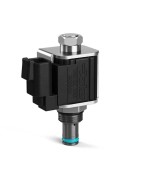
-
Spool Type Logic Element
Spool type logic elements offered by Parker come in four basic variations with multiple sizes for each variation. Different sizes within each variation perform the same, but the larger the size (“_ _”) the more flow the valve is capable of passing. The advantage of using logic element technology is that high flows can be controlled using smaller pilot devices which can lead to more compact and efficient systems. Spool-type logic elements are typically used to control virtually any pressure or flow function since the spool is allowed to modulate. However, spool valves have clearances, so Parker also offers Poppet-Type logic elements for high flow 2-way, 2-position low leak requirements.
The first step to applying logic elements is to determine if the application requires direction, pressure, or flow control. Direction control is typically the simplest due to the fact logic elements are only 2-way devices that can be internally or externally piloted. If pressure or flow control is desired, designers have flexible options that can be implemented by selecting from four basic types of spool-type logic elements. The four types below are grouped together based on whether the valve is normally-open or normally-closed, and internally or externally piloted.
Type 1: _ _SLC2-A and R_ _E3 series are normally closed, external pilot to close cartridges that flow from port 1 to port 2. This simply means that the spool normally blocks flow from port 1 to port 2 due to the internal bias spring. If no external pilot source is applied to the bias spring chamber, via port 3, then flow will pass from port 1 to port 2 at the bias spring pressure setting. When pilot pressure is applied to port 3 it becomes additive to the bias spring setting. Pilot pressure at port 3 needs to be supplied and/or controlled from an external source. Typical high flow functions for these logic elements include pressure reliefs, sequence valves, priority compensation, unloading and load-sense unloading.
Type 2: _ _SLC2-B and R_ _F3 series are identical to Type 1, with the exception of an orifice drilled in the spool allowing pressure from port 1 into the bias spring chamber and port 3, thus providing an internal pilot supply.
Type 3: _ _SLC3-A and R_ _H3 series are normally open, external pilot to open cartridges that flow from port 2 to port 1. This simply means that the spool normally allows flow from port 2 to port 1. If no external pilot source is applied to the bias spring chamber, via port 3, flow from port 2 to port 1 will begin to meter and restrict flow at the bias spring pressure setting. When pressure is applied to port 3 it becomes additive to the spring setting helping to hold the valve open. Pilot pressure at port 3 needs to be supplied and controlled from an external source. Typical high flow functions for these logic elements include restrictive flow control, pressure compensation, and pressure reducing.
Type 4: _ _SLC3-B and R_ _G3 series are identical to Type 3, with the exception of an orifice drilled in the spool allowing pressure from port 1 into the bias spring chamber and port 3, thus providing an internal pilot supply.
Parker’s extensive high flow spool-type logic elements allow for application specific solutions in the most demanding applications and markets including: Power Units, Oil and Gas, Material Handling, Construction, Drills, Presses, Mixers, Agriculture, Balers, Combines, Priority Steering, Priority Braking, High Flow Pressure Compensation, Fixed Pump Unloading, Load-Sense Unloading, Priority Flow Control, etc. -
Poppet Type Logic Element
Parker’s logic valves offer system designers a versatile range of screw-in elements that, when used in the proper combinations, can provide flexible design solutions for many common cartridge valve applications. They offer system designers the advantage of applying cartridge valve technology in applications where the flow and pressure conditions may exceed the limits of typical cartridge valves. Logic valves are essentially high flow poppet or spool elements that are controlled by small pilot devices. They can be used to control flow, pressure, or direction, and when applied in the proper arrangements, can perform multi-task control functions. Parker’s logic valves offer system designers alternative products that can help reduce the size, cost, and complexity of integrated manifold systems.
Poppet type logic valves are 3 ported, 2-way on/off valves that switch flow between port 1 and port 2. The poppet’s on/off action is operated by controlling pilot oil at port 3 of the valve. A small low flow solenoid or pilot valve is an ideal control for this purpose. Parker offers vent-to open and pilot-to-close style poppet logic valves.
Note: Poppet logic valves are an unbalanced 2:1 ratio poppet design. The opening and closing of the poppet is dependent on the force balances on the areas of the poppet at port 1, port 2, and port 3.
Vent-to-open logic valves:
Vent-to-open logic valves are primarily used for unidirectional flow switching applications. The poppet in the vent-to-open logic valve is spring biased to the closed condition. The pilot oil source that operates the logic element is generated internally by direct pressure from either work port 1 or 2, depending on the option chosen. Venting the pilot oil at port 3 allows the valve to open and pass flow between port 1 and port 2 at the bias spring setting. Blocking the pilot at port 3 causes the valve to close. When closed, the 2:1 ratio poppet design provides a positive low leak seal. Because the pilot source is generated internally within the valve, vent-to-open logic valves are best suited for uni-directional applications.
Parker’s 16SLC1-C Vent-to-open logic element is a size 16 valve capable of up to 50 gpm, 3500 psi. Standard spring settings of 50, 75, 100, and 150 psi are available. Manufactured with hardened, precision ground parts for durability, the 16SLC1-C is only available with Polyurethane seals only.
Pilot-to-close logic valve:
Pilot-to-close logic elements are primarily used for bidirectional flow switching applications. The poppet in the pilot-to-close logic valve is spring biased to the closed condition. With no pilot signal at port 3, the valve will open allowing flow in either direction between work ports 1 and 2 once pressure at one of the work ports reaches the biased spring setting. Appling a sufficient externally generated pilot force to port 3 of the valve closes the poppet creating a low leak seal between port 1 and port 2.
2-way, 3-way, and 4-way Directional Control:
Poppet logic valves are typically used to perform high flow directional switching operations using small low power pilot valves to control the sequence of the directional operation.
• A single logic valve can be used to control 2-way, on/off switching.
• Multiple elements in a bridge arrangement can control 3-way or 4-way directional switching.
• Since each logic valve is individually controlled, the timing, sequence, and overlap of directional functions can be controlled very precisely.
• Uni-directional or bi-directional flow can be achieved, depending on the valve selected.
• Flows in excess of 80 gpm can be controlled through a single logic element, and more than one logic valve can be used in parallel to control flow in excess of the rated flow of a single element.
• Poppet construction provides a low leak directional control.
Parker offers a wide variety of pilot-to-close logic elements ranging from 15 gpm to 80 gpm, 3500 psi. Spring ranges of 50, 75, 100, and 150 psi are available. Manufactured with hardened, precision ground parts for durability, these valve are available with Polyurethane seals only.
Common applications for logic elements are directional control valves, creating 2 way, 3 way, and 4 way valves, usually using a solenoid operated cartridge valve. Bridge circuits capable of up to 80 gpm can be controlled with a size 10, low flow directional cartridge valve. Also common are pressure and flow control circuits.
These valves can be found in all markets but most commonly used in mobile construction equipment, aerial devices, cranes, and excavation equipment. Applications include, but are not limited to, boom extension/retraction, outrigger control, winch control, conveying, steering, and auger control.