Zawory suwakowe
Parker offers needle valves for positive leak-tight shut-off and regulation of liquids and gases, in a variety of stem types, in both in-line and angle patterns. Several designs are provided for oil and gas processing facilities, along wit
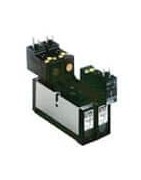
-
Pilot Operated Pressure Reducing Valves
Pilot operated pressure reducing valves are designed for continuous duty applications. Due to their stability and low pressure rise, the pilot operated pressure reducing valves are the best option for setting the pressure of a hydraulic system sub-circuit.
• Spool design provides low hysteresis
• Low parasitic loss
• High pressure capable
• Multiple pressure ranges available for more accurate pressure control
• Adjustable and tamperproof versions available
• All external parts zinc plated
• Hardened, precision ground parts for durability
• “D”-Ring seal standard on Winner's Circle
• Low profile adapter for minimal space requirements
Common circuit applications include: brake release, dual pressure circuits, pilot pressure control and downstream pressure control. -
Direct Acting Pressure Reducing Relieving Valves
Direct Acting Reducing/Relieving valves are applied in a circuit in order to reduce system pressure to the setting of valve to limit the pressure available to a specific branch of a hydraulic circuit. The direct acting function of the normally open valve allows the spool to operate directly against a control spring that is set using the valves internal adjustment setting. As hydraulic pressure is applied to the valve inlet, the spool will shift closed against the spring to limit the pressure that is available to the regulated port to the control setting. The valve will also function as a relief valve to the regulated port in the event of a rise in downstream pressure, protecting the regulated branch of the circuit from pressure spikes. Direct acting reducing/relieving valves are intended or intermittent duty applications with lower duty cycles that will not stress the mechanical operation of the valve. For best performance in the direct acting reducing/relieving valve, the inlet pressure setting should not exceed 1000 PSI (69 Bar) above the reducing valve setting, as high pressure differential could result in instability in the direct acting product. For continuous duty applications or applications where a high differential is required, the pilot operated version of this product should be considered as an alternative solution.
Typical applications are in mobile & industrial equipment, where a branch of the system is intended to operate at a lower setting than high system pressure. Hydraulic functions such as brake circuits, clamping or clutch circuits, suspension systems, street sweepers, or seeding and planting rows in agricultural equipment are common applications for these products.
• Hardened, precision ground parts for durability
• All External parts zinc plated
• Adjustable and tamperproof versions available
• Multiple pressure ranges available for more accurate pressure control -
Zawory redukcyjne i odciążające sterowane pośrednio
Rodzina sterowanych pośrednio zaworów redukcyjnych i odciążających firmy Parker zapewnia doskonałą regulację ciśnienia w zastosowaniach, w których potrzebne jest konkretne ciśnienie regulowane lub otwarcia w celu zapewnienia precyzyjnego działania funkcji wymagających regulowanego ciśnienia do 380 barów (5500 psi) i natężenia przepływu do 150 l/min (40 gal/min). Sterowane pośrednio zawory redukcyjno-odciążające firmy Parker zaprojektowano do kilku zakresów ciśnień, aby zapewnić wyższy stopień kontroli dzięki różnym dostępnym sposobom regulacji. Dodatkowa stabilność uzyskana dzięki sterowaniu pośredniemu sprawia, że zawory te doskonale się nadają do obsługi wrażliwych funkcji, takich jak podnoszenie lub docisk, zaciskanie lub hamowanie w różnych typach maszyn na rynkach mobilnym i przemysłowym.
Rynki:
• Rolnictwo
• Sprzęt budowlany
• Przemysł
• Produkcja
• Urządzenia mobilne
Cechy/zalety:
• Dostępność wielu zakresów ciśnień pozwala na dokładniejszą regulację ciśnienia.
• Kompaktowe rozmiary ograniczają wymagania przestrzenne
• Dostępne wersje regulowane i odporne na ingerencję.
• Możliwość pracy pod wysokim ciśnieniem.
• Wszystkie części zewnętrzne ocynkowane.
Zastosowania:
• Hamulce
• Opaski zaciskowe
• Układy zawieszenia
• Układy podnoszenia/docisku
Dodatkowe informacje techniczne:
Typowe zastosowania to urządzenia mobilne i przemysłowe, w których gałąź układu ma działać przy ustawieniu niższym niż wysokie ciśnienie układu. Funkcje hydrauliczne, takie jak obwody hamulcowe, obwody zaciskowe lub sprzęgła, układy zawieszenia, zamiatarki uliczne, lub rzędy siewu i sadzenia w sprzęcie rolniczym są typowymi zastosowaniami tych produktów. -
Zawory nadmiarowe sterowane pośrednio
Zawory nadmiarowe sterowane pośrednio firmy Parker cechują się stabilną konstrukcją o małym spadku ciśnienia. Przeznaczone są do zastosowań ciągłych przy pracy o niższym poziomie hałasu hydraulicznego. Zawory mają niezawodną i kompaktową konstrukcję i mogą pracować przy ciśnieniu do 420 barów (6000 psi) i natężeniu przepływu do 400 l/min (106 gal/min). Zawory nadmiarowe sterowane pośrednio firmy Parker idealnie nadają się do ograniczania ciśnienia w układzie lub w standardowych zastosowaniach zaworów nadmiarowych w urządzeniach mobilnych i przemysłowych, takich jak urządzenia rolnicze, lotnicze, do przetwarzania odpadów, przemysłowe systemy bloków energetycznych, urządzenia górnicze i inne obwody regulacji ciśnienia płynów przeznaczone do pracy ciężkiej.
Rynki:
• Przemysł
• Produkcja
• Urządzenia mobilne
Cechy/zalety:
• Wysokie ciśnienie i natężenie przepływu.
• Konstrukcje kulowe i grzybkowe o niskim wycieku.
• Kompaktowa konstrukcja.
• Wewnętrzne filtry.
• Hartowane, precyzyjnie szlifowane części zapewnia trwałość
• Wszystkie części zewnętrzne ocynkowane.
Zastosowania:
• Ogranicznik ciśnienia w układzie
• Przyłącze/upust między przyłączami
• Wychylany upust
• Hamowanie silnikiem
Dodatkowe informacje techniczne:
Ta rodzina zaworów najlepiej nadaje się do układów o pracy ciągłej, w których wymagana jest praca zaworu poza okresami użytkowania przerywanego. Mogą być używane do utrzymywania ciśnienia w układzie przez długi czas. Dodatkowo w systemach, w których mogą występować duże szybkości zmian przepływu, zawory sterowane pośrednio mogą dostosować się do tych zmian bez nadmiernego wzrostu ciśnienia. Ze względu na obszary otwarcia przepływu przez zawór zawory suwakowe będą działać ciszej niż konwencjonalne zawory bezpośredniego działania. Należy również wziąć pod uwagę poziom wycieków, ponieważ suwak ze względu na swoją konstrukcję przepuszcza niewielki wyciek, natomiast zawór bezpośredniego działania nie przepuszcza znaczącego przepływu do momentu osiągnięcia ciśnienia otwarcia. Suwakowych zaworów nadmiarowych nie należy używać do utrzymywania obciążenia. -
Unloading Relief Valves
Parker’s RU101 and M04A4J offer design flexibility by allowing the use of hydraulic components to automatically control pump flow to one or more accumulators. These are low flow pilot valves that can be used to control higher pump flows in fixed displacement or load sense systems.
The RU101 is externally piloted and rated for flows up to 1 GPM and pressures up to 3000 psi. It is typically used with fixed displacement pumps and can directly unload flows up to 1 GPM or be used to pilot a logic element to unload higher pump flows. Once the accumulators are charged to the adjustable or factory preset maximum pressure, the pump will automatically unload back to tank. Due to the differential area design, when the pressure drops to 80% of the RU101 maximum setting, the unloading valve will direct pump flow to the accumulators for recharging.
The M04A4J is internally piloted and is rated for flows up to .53 GPM and pressures as high as 6000 psi. It is typically used with load sense pumps to control accumulator charging. When the accumulators are charged to the unload pressure, the pump’s load sense port is directed to tank allowing the pump to go to its standby pressure. Once the accumulator pressure falls to the M04A4J reload pressure, the pump’s load sense port is fed the accumulator pressure and the pump comes on stroke to charge the accumulator back up to the unload pressure. Controlling only the pump load sense signal allows a small cartridge valve to control a wide range of flows from small to larger displacement load sense pumps.
Parker’s unloading pressure control valves offer design flexibility by allowing in-line mounting with standard line bodies, or integration into more complex custom manifolds. They can also be combined with K04G3 shuttles for use in critical applications that require redundant accumulators such as braking and steering. By hydraulically controlling pump unloading for accumulator charging, there may be no need for solenoid valves, pressure sensors, electronic controls, and the associated wiring. Combining the features of the RU101 or M04A4J with the many other products offered by Parker’s Hydraulic Cartridge Division allows for application specific solutions for some of the most demanding applications, including: Construction, Mining, Industrial Power Units, Oil and Gas, Marine, Material Handling. -
Pilot Operated Sequence Valve with Kickdown
Unlike relief valves which will reset slightly below their pressure setting, Parker’s B04C3 Kick-Down sequence valve will continue to unload pump flow until its supply flow is completely stopped. Two adjustable pressure ranges are standard for 3000 or 6000 PSI maximum operating pressures, and each version is capable of flows up to 42 GPM. Screw, knob, and tamper-resistant adjustment options are available.
B04C3 pilot operated cartridges are normally closed, internally piloted and externally drained. The external drain prevents downstream pressure from having an effect on the valve setting. When inlet pressure at port 1 is lower than the valve’s setting, flow is not allowed to exit port 2. Once the pressure setting is reached, flow from port 1 is unloaded to port 2. The valve does not reset and close until flow is completely removed from port 1. Staying open after the setting is reached creates a requirement for an operator or the system controls to take steps of removing flow before the valve can stop unloading the pump. Functioning in a manner similar to a fuse can provide additional over-pressurization protection and can also help to detect unusual high pressure machine conditions.
Typical Applications include: Machine Tool, Power Units, Presses, Clamping, Forging, Construction, Material Handling -
Pilot Operated Sequence Valve with Reverse Check
B04D3 is an internally piloted and externally drained sequence valve with an integrated reverse free flow check valve. When pressure is below the sequence setting the valve is normally closed. Once the pressure setting is reached the valve is internally piloted open allowing flow to a secondary branch of the circuit. Flow from the secondary branch is allowed to free flow back to the primary branch via the reverse flow check. The external drain should be plumbed directly back to tank to prevent downstream pressure from adding to the sequence setting. Two adjustable pressure ranges are standard for 3000 or 6000 PSI maximum operating pressures, and each version is capable of flows up to 32 GPM. Screw, knob, and tamper-resistant adjustment options are available.
Combining a sequencing function and reverse flow check into a single size 10 cartridge reduces manifold space, complexity and the number of components. The integrated check valve reduces internal drillings and can also allow for multiple double acting functions to be operated with a single directional control valve. Parker’s B04D3 offers design flexibility that can be utilized an many applications including: Clamp and Drill, Machine Tools, Presses, Power Units, Material Handling, Construction, Agriculture, -
Pilot Operated Sequence Valves
SVH081, SVH101, and SVH161 pilot operated sequence valves are internally piloted and externally drained. All three versions are normally closed spool-type valves that prevent flow from passing through the valve until the adjustable pressure setting is reached. When the inlet pressure exceeds the sequence setting the valve is internally piloted open allowing flow downstream to a secondary function. An external drain port plumbed directly to tank ensures that downstream pressure does not affect the pressure setting. Clamp and machine, or unlock and dump, are typical applications since they require one function to happen before another one.
SVH102 and SVH162 are externally piloted and internally drained sequence valves. Both are normally closed and prevent flow from passing through the valve when the pilot pressure is below the pressure setting. When the external pilot source exceeds the adjustable pressure setting, the valve opens allowing flow to go downstream. Back pressure on the downstream port is added to the valve setting due to the internal drain, therefore it is most common to connect the sequenced port to tank. High-Low Pump Unloading is a common application.
SVCH101 is an inline mounted combination of an internally piloted, externally drained sequence valve and a reverse flow check. An SVH101 sequence valve and a CVH103 check valve are incorporated into a single body with SAE-8 work ports and an SAE-6 drain.
Parker’s pilot operated sequence valves have multiple pressure ranges up to 5000 PSI and flow capabilities up to 40 GPM. Fixed, screw, knob, or tamper-resistant pressure adjustment options are available. Typical markets and applications include: Clamp and Drill, Un-Lock and Dump, High-Low Pump Unloading, Industrial Power Units, Machine Tools, Material Handling, Construction, Agriculture, etc. -
3 Position, 4 Way Pull/Push to Shift Spool Type Manual Valve
DMH085 manual 4-way 3-position valves allow for directional control of bi-directional motors, double acting cylinders, and rotary actuators by pushing or pulling an integrated knob which is attached to a spool inside the cartridge. The spool is spring centered and available with multiple neutral position options including closed-center, float-center, tandem-center, and open-center. Multiple spool configurations provide design flexibility for use with fixed or variable displacement pumps, various actuator types, and different load holding approaches. Application engineers are available to help determine the best solution for your system. Typical applications include, hoists, material handling, construction, agriculture, oil and gas, machine tools, presses, forging, power units, grinders, mixers, drills and refuse. -
3 Way Rotary Type Manual Valve
DM103 valves are 3-way manually operated rotary spool type directional control valves. Knob, Finger-Knob and Lever actuators are available. Versions K, LD and FKD are 2-position valves that are actuated by turning the knob or lever a full 90 degrees. LN and FKN versions are 3-position valves which have a closed center condition and can be actuated by rotating the knob 45 degrees in either direction. All versions except K come standard with detents.
Parker’s DM103 series of manually operated valves can be applied as normally open or normally closed and can also be used as selectors. Typical applications include, hoists, material handling, construction, agriculture, oil and gas, machine tools, presses, forging, power units, grinders, mixers, drills and refuse. -
Direct Acting Sequence Valve
Parker’s family of direct acting sequence valves are fast acting and designed for sequenced applications with pressures up to 420 bar (6000 psi) and flows up to 56 lpm (15 gpm) in a variety of sizes. The selection of pressure adjustment styles and piloted or vented controls makes these valves an ideal solution for controlling multiple circuit sections that operate at different pressure settings. Normally-open and normally-closed valves are available in either 2 position 2-way or 2 position 3-way configurations. These direct acting sequence valves can be used within clamping circuits or high/low system applications within several industrial and mobile markets.
Markets:
• Agriculture
• Construction
• Material Handling
• Miscellaneous Industrial
• Miscellaneous Manufacturing
• Miscellaneous Mobile
Features & Benefits:
• Fast response
• Internal mechanical stops limiting spool travel
• Hardened, precision ground parts for durability
• All external parts zinc plated
• Adjustable, fixed, or tamper resistant adjustments available
Applications:
• Dump circuits
• High/low systems
• Sequencing applications
Additional Technical Insight:
Direct acting sequence valves are spool-type devices that allow multiple functions to operate in sequence without the need for solenoid valves, limit switches, or complex control systems. Parker’s B02, B04, and SV10 sequence valves provide design options for 2-position 2-way or 2-position 3-way sequencing with pilot signals and drains provided internally or externally. Externally drained versions are not sensitive to downstream pressure if they are drained to the tank. One or more sequence valves can be used in a circuit to allow multiple functions to operate in a specific order based on pressure. Normally closed and normally open versions are available to allow for design flexibility.
Parker’s B04H4, B04J4, and SV104 series of direct acting sequence valves are Externally Piloted and Externally Drained. The Normally Closed B04H4 is a 2-position 2-way valve that blocks flow in both directions until an external pilot supply pressure overcomes the sequencing setting. B04J4 and SV104 are Normally Open 2-position 2-way valves that allow bi-directional flow until the external pilot supply reaches the sequence setting. All three valves are insensitive to back pressure when their drain line is connected to tank.
Parker’s B04F3, B04G3, B04K4, and SV105 series of direct acting sequence valves are Externally Piloted and Internally Drained. The Normally Closed B04F3 and SV105 are 2-postion 2-way valves that prevent flow from passing from port 3 to 2 until an external pilot supply pressure overcomes the sequencing setting. Once the sequence pressure is reached the valve will open allowing flow from port 3 to 2. B04G3 is a 2-position 2-way Normally Open valve that allows flow from port 2 to 3 until the external pilot pressure reaches the sequence pressure blocking flow from 2 to 3. B04K4 is a 2-position 3-way normally open valve that allows bi-directional flow between ports 2 and 3 until the sequence pressure is met. Once the pilot pressure exceeds the set pressure, port 2 is blocked and flow is allowed from port 3 to port 4. The internal drain causes downstream pressure to be additive to the valves pressure setting, therefore it is most common for the downstream port to be connected to tank.
Parker’s B02E3F and B04E3 direct acting 2-position 3-way sequence valves are Internally Piloted and Internally Drained. Flow from port 2 to 1 is normally open until the pressure at port 1 exceeds the valves setting which closes port 3 and allows flow from port 1 to port 2.
Parker’s SV103 direct acting 2-position 3-way sequence valve is Internally Piloted and Externally Drained. Flow from port 1 to 2 is Normally Closed until the pressure at port 1 exceeds the sequence setting which allows flow from port 1 to 2. Port 3 is a dedicated spring chamber vent which makes the valve insensitive to downstream pressure at port 2.
Please contact Parker Hydraulic Cartridge Division if you have a sequencing application that requires higher flow rates. Pilot Operated Sequence Valves are capable of flows up to 42 GPM. Higher flows up to 130 GPM can be achieved with the use of logic elements and small pilot valves. -
4 Way Rotary Type Manual Valve
DM104 valves are 4-way manually operated rotary spool type directional control valves. Knob, Finger Knob and lever actuators are available. Versions K, LD and FKD are 2-position valves that are actuated by turning the knob or lever a full 90 degrees. LN and FKN versions are 3-position valves which have a closed center condition and can be actuated by rotating the knob 45 degrees in either direction. All versions except K come standard with detents.
Parker’s DM104 series of manually operated valves are perfect for many 4-way directional control applications where manual operation is required. Typical applications include, hoists, material handling, construction, agriculture, oil and gas, machine tools, presses, forging, power units, grinders, mixers, drills and refuse. -
Pressure Compensated Priority Flow Control Valves
Priority style pressure compensator flow control valves maintain constant priority flow to one leg of a circuit regardless of any changes in load or inlet pressure. Once the priority flow is satisfied, any excess flow may be used in other parts of the circuit.
The valve consists of a control orifice housed within a spring biased compensator spool. This orifice may be fixed or adjustable. The priority port is normally open while the bypass port is normally closed. As flow enters the inlet port of the cartridge, it passes through the control orifice. A pressure differential is created across the compensator spool. If the inlet flow exceeds the setting of the valve, the force produced by this pressure differential exceeds the spring force and shifts the compensator spool; opening up the bypass port, and bypassing the excess flow. If the load pressure at the bypass port is greater than the load pressure at the priority port, the compensator spool will further shift restricting the priority flow to that of the valve setting. However, caution should be taken if the priority gets blocked so that no flow can pass through the control orifice, the compensator spool will shift, blocking the bypass port and allowing inlet pressure to go to full system relief pressure. It is common to place an external relief valve downstream of the priority flow port to prevent a no flow condition.
Parker offers four styles of Pressure Compensated Priority Flow Controls ranging from 4 to 24 gallons per minute. Parker’s offering is as follows:
J02D3 - 4 gpm rated flow, 6000 psi, and is available with adjustment styles of Screw adjust, Knob adjust, and a Tamper resistant cap. Customers can request specific flow settings. Buna and Fluorocarbon seals available.
FP101 - 8 gpm rated flow with 15 gpm max inlet, 3500 psi, with adjustment styles of Fixed, Knob, and Screw. Nitrile and Fluorocarbon seals available.
J04D3 - 12 gpm rated flow, 6000 psi, and is available with adjustment styles of Screw, Knob, and Tamper Resistant cap. Customers can request specific flow settings. Nitrile and Fluorocarbon seals available.
J1A125 - 24 gpm rated flow, 5000 psi, and is available with adjustments styles of Screw, Knob, and Tamper Resistant. Customers can request specific flow settings. Nitrile and Fluorocarbon seals available.
Pressure compensated priority flow control valves are typically used in meter-in type circuits like steering (mobile equipment) or actuator speed control (industrial equipment) where a fixed displacement pump is being used. -
Pressure Compensators/Control Elements
Inlet flow (upstream of the orifice or flow control valve) is split with one portion going to the compensator port inlet, the other portion passes through the orifice, or flow control valve, to the supply port. As pressure drop across the orifice reaches the selected compensator pressure drop, the higher pressure (pre-orifice) starts to shift the compensator spool into a throttling position. The valve works to maintain a constant pressure drop across the orifice. Using this type of valve allows greater flexibility in design and flows as these valves can flow as much as 40 gallons per minute.
Compensator valves are used in circuits where a constant flow is desired regardless of upstream or downstream loads. As the pressure downstream of the compensator increases, the valve is forced open to maintain the constant pressure drop across the fixed, or adjustable, orifice. Conversely, if the pressure increases upstream of the orifice, the compensator valve will be forced closed to maintain the constant pressure drop across the orifice.
Parker offers two sizes of restrictive type of pressure compensators ranging in flows from 10 gallons per minute to 40 gallons per minute, and pressures up to 3500 psi.
FCR101 - 10 gpm rated flow (38 lpm), 3500 psi. Differential pressure ranges of 40, 80, and 160 psi and is available with Nitrile or Fluorocarbon seals.
FCR161F - 40 gpm rated flow (150 lpm), 3500 psi. Differential pressure ranges of 40 and 160 psi and is available with Nitrile or Fluorocarbon seals.
Pressure compensators can typically be found in applications such as conveyor circuits in saw mills, or lumber yards, steel mills, or cylinder control circuits in steel mills or foundries. -
Pressure Compensated Flow Control Valves
Parker offers a wide range of spool type restrictive pressure compensated flow controls to allow for speed control of motors, cylinders, and rotary actuators. Pressure compensation allows the flow devices to maintain a constant flow even with varying loads and inlet pressures. Tunable and fully adjustable versions are available with screw or knob adjusters that can be made tamper resistant with the addition of an optional cap.
FR101 is a tunable pressure compensated flow regulator which compensates for varying loads and pressures in one direction but in the other direction flow is metered across a fixed orifice but not compensated. In order to allow pressure compensated flow control in one direction and full free flow in the opposite direction, Parker offers an internal check valve in the tunable FC101 cartridge. Because both versions are tunable and not fully adjustable, the valve will need to be specified with the appropriate flow range for the application. Changes in flow rates are achieved by mechanically varying the spring force acting on a spool that has a fixed orifice and metering compensator.
J02E2, J04C2, and J04E2 are fully adjustable pressure compensated flow regulators. In the opposite flow direction they only meter through a fixed orifice and do not compensate. In order to achieve fully adjustable pressure compensated flow control while allowing reverse full flow, the FA101 includes an internal check valve to bypass the compensator and metering orifice.
Typical applications and industries include Accumulator Bleed-off, Motor Speed Control, Cylinder Speed Control, Bleed-Off Flow, Power Units, Oil and Gas, Material Handling, Construction, Drills, Presses, Mixers, Agriculture, Balers, Combines, etc. -
Flow Divider/Combiner Valves
Each of Parker’s four flow divider/combiner versions can be used as a divider or combiner depending on the direction of flow. Two inter-locking spools allow for pressure compensated flow division and combination to be proportioned based on the selected ratio and flow range. When port 3 is supplied flow it is divided by a fixed ratio to work ports 2 and 4. For example, if a 50:50 ratio is selected half of the flow will exit port 2 and the other half will exit port 4. If the actuators have the same area or displacement they will operate at the same speed. If different actuator speeds are required, alternative ratios can be selected to supply different flows to each port. Ratios other than 50:50 can allow speed synchronization of two actuators that have different areas or displacements. The flow to each actuator port is proportional to the inlet flow based on the flow division ratio.
When used as a combiner, flow applied to ports 2 and 4 is combined and the total flow exits port 3. The flow from the combiner inlet ports is pressure compensated and the flow ratio determines how much flow is allowed from each port. Just like the divider mode, the combiner mode allows for actuator speed variation or synchronization.
Typical flow accuracy is +/- 10% between ports 2 and 4. When trying to synchronize 2 cylinders or motors, cross-port relief valves or balancing orifices can be used to help maintain tighter synchronization.
Parker’s FDC101, L04A3, L06A3 and L1A300 flow divider/combiners operate in the same manner with each having a different maximum flow and multiple standard ratios and flow ranges. Typical applications and industries include cylinder synchronization, motor synchronization, flow partitioning, transmission differentials, construction, oil and gas, material handling, military, grinders, mixers, drills, snow blowers, etc. -
Priority Pressure Compensators
Parker offers two styles of Priority Pressure Compensators, ranging in flows from 10 to 20 gallons per minute, and pressure capabilities of 3500 psi and 5500 psi. Flow through the external orifice (fixed or variable) enters the supply port and produces a pressure drop across the compensator spool. When the inlet pressure exceeds the initial setting of the valve, the force produced by the pressure differential across the spool exceeds the spring force and shifts the compensator spool to throttle, or restrict, the flow, thus maintaining constant flow through the priority port. The excess flow is bypassed out to the system to be used by another function, or back to the system reservoir. Flow out the regulated port must be maintained for bypass flow to continue. For this reason, common practice dictates a pressure control (relief) be installed in the priority line.
Parker offers the following styles of Priority Pressure Compensators:
FCP101 - Up to 10 gallons per minute priority flow rate (38 lpm), 15 gallon per minute maximum inlet flow (56 lpm), 3500 psi. Available with differential pressure settings of 40, 80, and 160 psi. Nitrile and Fluorocarbon seals available.
FCPH121 - Up to 20 gallons per minute priority flow rate (75 lpm), 25 gallons per minute maximum inlet flow (95 lpm), 5500 psi. Available with fixed (customer specified) or variable differential pressure settings. Adjustments are knob or screw adjust, with a tamper resistant cap available.
Priority Pressure Compensators are used where the design calls for constant flow to a particular segment of the circuit, regardless of upstream or downstream pressure (load) changes. A common application is for speed control on a conveying system. Should the load on the conveyor increase, the pressure increases at the compensator and the valve modulates to maintain the desired pressure differential across the valve. This modulation allows more flow to pass through the valve thus maintaining a constant desired speed. Conversely, should the load on the conveyor decrease, the opposite happens and the compensator modulates, restricting some flow to maintain the desired pressure differential, thus providing constant speed.
Parker Priority Pressure Compensators may be found in steering circuits, conveying systems, lift/lower systems in markets such as mobile/agricultural companies, steel or lumber mills, or off-highway mobile equipment. -
2 Way Spool Type Solenoid Valve
Parker’s readily available Winners Circle line includes common cavity C08-2 and C10-2 direct acting 2-way, 2-position spool valves.
The DSL082 and DSL102 series of valves are rated for 3600 psi (250 bar.) For applications that require pressures up to 5000 PSI (350 BAR,) Parker also offers the DSH082 and DSH102 valve series. All versions are available normally-open, or normally-closed and can be provided with optional Pull & Release or Push & Twist manual overrides. Direct acting spool valves are fast to respond to coil voltage and will block flow in both directions. Some leakage will be present due to spool clearances so please consider Parker’s 2-way Poppet Valves if leakage less than 5 drops per minute is required. Even though flow is bi-direction, due to flow forces, the preferred flow path is from the side of the cartridge (port 2) to the nose (port 1.)
In addition to the Winners Circle product, Parker also offers the direct acting 2-way, 2-position GS02 series of valves with flows up to 4 GPM (15 LPM) and pressures as high as 5000 PSI. GS02 22 is normally-closed and GS02 27 is normally-open. Both versions are available with optional Push and Release, or Detented Screw-type manual overrides.
Parker also offers a 20 GPM (75 LPM) 3000 PSI (210 BAR) direct acting 2-way, 2-position spool valve for applications that require higher flow rates. The DS162 cartridge valve is available normally-open or normally-closed and comes standard with a Push and Release manual override.
Combined with Parker’s wide range of Coil options which include AC and DC voltages and extensive termination options, the 2-way direct acting spool valve offering allows for application specific solutions in the most demanding applications and markets including: Power Units, Oil and Gas, Material Handling, Construction, Drills, Presses, Mixers, Agriculture, Balers, Combines, etc. -
3 Way Spool Type Solenoid Valve
Parker’s readily available Winners Circle line includes common cavity C08-2 and C10-2 direct acting 3-way, 2-position spool valves capable of flows up to 8 GPM (30 LPM.) The DSL083 and DSL103 series of valves are rated for 3600 psi (250 bar.) For applications that require pressures up to 5000 PSI (350 BAR,) Parker also offers the DSH083 and DSH103 valve series. Normally-open, normally-closed, and selector spool variations are available for all versions and each can be provided with optional Pull & Release or Push & Twist manual overrides. Direct acting spool valves are fast to respond to coil voltage and will allow flow passage between 2 ports while blocking the remaining port. Some leakage will be present due to spool clearances.
Parker also offers a 15 GPM (57 LPM) 3000 PSI (210 BAR) direct acting 3-way, 2-position spool valve for applications that require higher flow rates. The DS163 cartridge valve is available normally-open or normally-closed, and can be used as a selector. A Push and Release manual override is standard.
Combined with Parker’s wide range of Coil options which include AC and DC voltages and extensive termination options, the 3-way direct acting spool valve offering allows for application specific solutions in the most demanding applications and markets including: Power Units, Oil and Gas, Material Handling, Construction, Drills, Presses, Mixers, Agriculture, Balers, Combines, Single Acting Cylinder Control, Uni-Direction Motor Control, Circuit Selectors, etc. -
4 Way 2 Position Spool Type Solenoid Valve
Parker’s readily available Winners Circle line includes common cavity C08-2 and C10-2 direct acting 4-way, 2-position spool valves capable of flows up to 8 GPM (30 LPM.) The DSL084 and DSL104 series of valves are rated for 3600 psi (250 bar.) For applications that require pressures up to 5000 PSI (350 BAR,) Parker also offers the DSH084 and DSH104 valve series. Multiple spool variations are available for application flexibility and all versions can be provided with optional Pull & Release or Push & Twist manual overrides. Direct acting spool valves are fast to respond to coil voltage and can quickly re-direct or block flow to actuator ports. Some leakage will be present due to spool clearances.
In addition to the Winners Circle product, Parker also offers a direct acting 4-way, 2-position GS02 series capable of flows up to 5 GPM (19 LPM) and pressures as high as 5000 PSI. GS02 42 comes with one standard spool configuration and optional Push and Release, or Detented Screw-type manual overrides are available.
Parker also offers a 30 GPM (114 LPM) 5000 PSI (350 BAR) direct acting 4-way, 2-position spool valve for applications that require higher flow rates. The DSH164 cartridge valve comes with one standard spool configuration and manual overrides are not available as a standard option.
Combined with Parker’s wide range of Coil options which include AC and DC voltages and extensive termination options, the 4-way direct acting spool valve offering allows for application specific solutions in the most demanding applications and markets including: Power Units, Oil and Gas, Material Handling, Construction, Drills, Presses, Mixers, Agriculture, Balers, Combines, Double Acting Cylinder Control, Bi-Direction Motor Control, Circuit Selectors, etc. -
3 Way Pilot Operated Directional Control Valves
Parker’s three way pilot operated spool valves are used to direct flow alternately from either side of a closed loop transmission for cooling or filtering. With flow ranging from 10 gpm to 24 gpm, and pressures up to 5000 psi, these valves are a versatile solution to many hydrostatic applications.
Parkers DH103 series valve is rated for 10 gpm at 3500 psi. This 3 ported valve is available in both normally open and normally closed orientation. Two versions of the normally open series are available. The DH103A series in its neutral (deactivated) position allow Port 3 open to Port 2, with port 4 blocked. Pilot pressure at Port 1 shifts the spool blocking Port 2, allowing Port 3 to be open to Port 4. The DH103A valve is a vent to atmosphere valve allowing pressure equalization in the spring chamber.
Parker’s DH103B configuration is a normally closed version of the valve. In its neutral (deactivated) orientation, Port 2 is blocked while Port 4 is open to Port 3. When a pilot signal is applied to Port 1, the spool is shifted blocking Port 4, allowing Port 3 to be open to Port 2. Unlike DH103A, the spring chamber is vented to Port 4. Care must be taken to be aware of back pressure in Port 4 being additive to the spring setting.
Parker’s DH103C series is a normally open version, operating like the DH103A series, with the exception of the vented spring chamber.
The DH103 series of valves are available with three switching pressures (40 psi, 80 psi, 160 psi) and Nitrile or Fluorcarbon seals.
Parker’s N04A4 and N04B4 are higher flow versions of the DH103B and DH103C valves. The N04A4 series operation in its neutral (deactivated) position allow Port 3 to be open to Port 4, with Port 2 blocked. When a pilot signal is activated at Port 1, the spool shifts against the spring allowing Port 3 to be open to Port 2, with Port 4 blocked. The spring chamber is vented to Port 4 so care needs to be taken with back pressure at Port 4 additive to the spring setting.
Parker’s N04B4 series operation in its neutral (deactivated) position allows Port 3 to be open to Port 2, with Port 4 blocked. When a pilot signal is activated at Port 1, the spool shifts against the spring allowing Port 3 to be open to Port 4, blocking Port 2. The spring chamber is vented to Port 4 so care needs to be taken with back pressure at Port 4 additive to the spring setting.
Parker’s N04 series of Pilot Operated Directional Valves are available with switching pressures of 73 psi and 145 psi, and are available with either Nitrile or Fluorocarbon seals. -
5 Way/2 Position Pilot Operated Directional Control Valves
N5 cartridge valves from Parker provide design flexibility for high pressure and high flow applications because they are actually 5-ported cartridges. Each version has 3 work ports, 1 Main pilot port, and one spring chamber vent that can sometimes be used as a second pilot / sense port. Each cartridge contains a spool that is offset by a spring to allow a non-piloted flow configuration. Once pilot pressure is applied to port 1, the spool shifts against the spring creating a second flow configuration. Multiple spool configurations, transition types, and switching pressures are available to cover a wide range of applications.
N5A125 and N5A300 cartridge valves have an open transition which connects all 3 work ports together during the shifting of the spool. Both versions operate in the same manner with the key difference being flow rating. The N5A125 is rated for 42 GPM (160 LPM) and the N5A300 is rated for 105 GPM (400 LPM.) They can be used as normally-open, normally-closed and selector directional control valves and in a wide range of pressure and/or flow control circuits. The 5th port spring chamber can be vented to tank or used as a sensing port for applications that require high flow pressure or flow control. Pressure compensation, priority flow control, pressure reducing, pressure relieving, and pressure sequencing are just a few of the applications for these extremely versatile cartridge valves.
N5B125 and N5B300 have the same respective flow ratings and operate in the same manner as the respective N5A125 and N5A300. The key difference is that N5B cartridges have a closed condition transition. Please contact your Parker Application Engineer for assistance selecting the best transition condition for your application.
N5C and N5D are similar in their operation to N5A and N5B cartridges but without the transition conditions and with either all work ports blocked or all work ports open. N5C125 and N5C300 cartridges have spools that are spring offset to a condition where all 3 work ports are open. Once pilot pressure is applied to port 1, all 3 work ports are blocked. N5D125 and N5D300 valves are spring offset to an all ports blocked condition. Once pilot pressure is applied, the spool shifts and all ports are connected together. Flow ratings for both size 125 styles is 42 GPM (160 LPM) and the size 300 styles are rated for 105 GPM (400 LPM.)
Parker’s N5 high flow 3-way 2-position control valve offering allows for application specific solutions in the most demanding applications and markets including: Power Units, Oil and Gas, Material Handling, Construction, Drills, Presses, Mixers, Agriculture, Balers, Combines, Priority Steering, Priority Braking, High Flow Pressure Compensation, etc. -
2 Way Pilot Operated Directional Control Valves
Parker’s R04* series of directional valves are available both normally-open and normally-closed. Flow ranges up to 26 gpm and pressure rating of 6000 psi, these valves are used as a switching valve by sensing pressure in other parts of the circuit.
The R04*3 series valve is a 2 way, 2 position valve that is 3 ported. With port one (nose) of the valve the pilot port, main flow goes through ports 2 and 3. The spring chamber is ported to port three so care needs to be taken making sure this is the low pressure side of the circuit.
When a pilot signal is given at port one, pressure acts upon the spool lifting it against the spring and closing flow from port two to port three. Spring chamber is vented internally out port three. When the pilot signal is removed, the spring acts upon the spool forcing it open to allow flow from ports two to three. Switching pressures of 5 bar and 10 bar are available. This valve is also available in a normally closed configuration.
The R04*4 series valve is a 2 way, 2 position valve that is 4 ported. Like the R04*3 series of valves, this valve received the pilot signal at port 1, shifting the valve against the spring and closing flow from port two to port three. A fourth port is connected to the spring chamber allowing the oil to vent independently of pressure at port three.
The R04 series of valve are used as a high flow directional control valve or unloader valve. Typical markets include, but are not limited to: Aerial lift, fork lift, off-road earth moving contruction equipment, industrial special machinery, conveying systems. -
Spool Type Logic Element
Spool type logic elements offered by Parker come in four basic variations with multiple sizes for each variation. Different sizes within each variation perform the same, but the larger the size (“_ _”) the more flow the valve is capable of passing. The advantage of using logic element technology is that high flows can be controlled using smaller pilot devices which can lead to more compact and efficient systems. Spool-type logic elements are typically used to control virtually any pressure or flow function since the spool is allowed to modulate. However, spool valves have clearances, so Parker also offers Poppet-Type logic elements for high flow 2-way, 2-position low leak requirements.
The first step to applying logic elements is to determine if the application requires direction, pressure, or flow control. Direction control is typically the simplest due to the fact logic elements are only 2-way devices that can be internally or externally piloted. If pressure or flow control is desired, designers have flexible options that can be implemented by selecting from four basic types of spool-type logic elements. The four types below are grouped together based on whether the valve is normally-open or normally-closed, and internally or externally piloted.
Type 1: _ _SLC2-A and R_ _E3 series are normally closed, external pilot to close cartridges that flow from port 1 to port 2. This simply means that the spool normally blocks flow from port 1 to port 2 due to the internal bias spring. If no external pilot source is applied to the bias spring chamber, via port 3, then flow will pass from port 1 to port 2 at the bias spring pressure setting. When pilot pressure is applied to port 3 it becomes additive to the bias spring setting. Pilot pressure at port 3 needs to be supplied and/or controlled from an external source. Typical high flow functions for these logic elements include pressure reliefs, sequence valves, priority compensation, unloading and load-sense unloading.
Type 2: _ _SLC2-B and R_ _F3 series are identical to Type 1, with the exception of an orifice drilled in the spool allowing pressure from port 1 into the bias spring chamber and port 3, thus providing an internal pilot supply.
Type 3: _ _SLC3-A and R_ _H3 series are normally open, external pilot to open cartridges that flow from port 2 to port 1. This simply means that the spool normally allows flow from port 2 to port 1. If no external pilot source is applied to the bias spring chamber, via port 3, flow from port 2 to port 1 will begin to meter and restrict flow at the bias spring pressure setting. When pressure is applied to port 3 it becomes additive to the spring setting helping to hold the valve open. Pilot pressure at port 3 needs to be supplied and controlled from an external source. Typical high flow functions for these logic elements include restrictive flow control, pressure compensation, and pressure reducing.
Type 4: _ _SLC3-B and R_ _G3 series are identical to Type 3, with the exception of an orifice drilled in the spool allowing pressure from port 1 into the bias spring chamber and port 3, thus providing an internal pilot supply.
Parker’s extensive high flow spool-type logic elements allow for application specific solutions in the most demanding applications and markets including: Power Units, Oil and Gas, Material Handling, Construction, Drills, Presses, Mixers, Agriculture, Balers, Combines, Priority Steering, Priority Braking, High Flow Pressure Compensation, Fixed Pump Unloading, Load-Sense Unloading, Priority Flow Control, etc. -
3 Way Flow Control Proportional Valves
Parker’s proportional flow control valves provide electronically variable flow control. Varying coil current will create a proportional flow out to an actuator allowing control of speed, acceleration, and deceleration. AC and DC coil options are available, along with a wide range of connection types. Current Controlled Pulse Width Modulation (PWM) valve drivers are preferred as they adjust for variations in coil temperature and also provide the ability to apply a dither frequency.
Priority Bypass is the last type of proportional flow control manufactured by Parker. Two sizes are available and the largest version is capable of flows up to 20 GPM (75 LPM.) Priority bypass flow controls are 3-way spool-type valves that consist of an inlet port, a priority port, and a bypass port. When no current is applied to the coil, all inlet flow exits the bypass port. As current is increased the spool shifts allowing a proportional amount of pressure compensated flow to the priority port while bypassing any remaining flow to the bypass port. Bypass flow is not allowed unless the priority ports has achieved the commanded proportional flow rate based on the input current. This allows for a priority of flow to one part of a circuit regardless of varying load conditions in both parts of the circuit. Typical priority applications include braking and steering.
Combined with Parker’s wide range of Coil options, the extensive proportional flow control offering allows for application specific solutions in the most demanding applications and markets including: Power Units, Oil and Gas, Material Handling, Construction, Drills, Presses, Mixers, Agriculture, Balers, Combines, Double Acting Cylinder Control, Bi-Direction Motor Control, Circuit Selectors, Skid-Steers, etc. -
Pressure Reducing Proportional Valves
Parker’s proportional pressure reducing valves provide electronically variable reduced pressure to protect system components and assist in force and torque control. Pressure reducing relieving valves are of spool-type design and consist of an inlet port, a reduced pressure port, and a tank port. Varying coil current will create a proportionally lower output pressure in the reduced pressure port when supplied a higher pressure at the inlet port. When no current is applied the reduced pressure port is vented to tank and the inlet port is blocked by the spool. Once current is applied the spool shifts and meters flow from the inlet port to the reduced pressure port and maintains a constant pressure at the reduced pressure port. Higher current results in a higher reduced pressure. The reduced port pressure is relieved to tank if it exceeds the valves input command pressure. AC and DC coil options are available, along with a wide range of connection types. Current Controlled Pulse Width Modulation (PWM) valve drivers are preferred as they adjust for variations in coil temperature and also provide the ability to apply a dither frequency.
Combined with Parker’s wide range of Coil options, proportional pressure reducing / relieving valves allow for application specific solutions in the most demanding applications and markets including: Power Units, Oil and Gas, Material Handling, Construction, Drills, Presses, Mixers, Agriculture, Balers, Combines, Double Acting Cylinder Control, Bi-Direction Motor Control, Circuit Selectors, Skid-Steers, etc. -
Pressure Compensated Proportional Poppet Valves
Parker Hydraulic Cartridge Systems Division combines Parker’s precision ground poppet and SuperCoil technology with a newly patented integral compensator design, bringing you a flow control product with best in class repeatability and a truly exceptional level of control.
In conditions of varying load, the FAPC series maintains predictable and repeatable performance through the introduction of our new fully integrated compensator. Built directly into the FAPC series valves, the innovative new compensator maintains a tight seal for load holding without any requirement for additional sealing. When open, the compensator responds to changing load conditions independently. With no seal friction to overcome, the FAPC valve maintains the repeatable and predictable performance customers can rely on. This additional feature eliminates the need for complex programming algorithms, and any requirement for an external compensator to improve the operator’s control.
• Excellent metering capability and control throughout the full flow range
• Reduced drift
• Low leak control (less than 5 dpm)
• Modular solution to applied problem
• Low leak compensator, requiring no additional seals, results in very low hysteresis (< 10%)
• Maintains constant flow regardless of load condition
• Patented integrated low leak compensator
How it works:
The FAPC utilizes a control current to proportionally raise and lower a poppet creating a variable orifice allowing flow to pass through from the inlet to the outlet. There is also a low leak integral compensator that responds to load changes in the hydraulic circuit by varying the outlet orifice, metering the flow rate that can be passed through and maintaining constant flow independent of load conditions.
The fully compensated FAPC is rated to flows up to 115 LPM (22 GPM).
Common markets and applications include the aerial markets (boom raise/lower), fork lift (lift/lower) and vehicle lift. -
Pressure Relieving Proportional Valve
Parker offers direct and pilot operated proportional relief valves. Two styles are available; increasing pressure with increasing current, and decreasing pressure with increasing current. All styles offered normally opened or normally closed.
Normally Closed Proportional Relief Valve
Normally closed proportional relief valves are used to electronically control the system pressure. These valves are ideal for circuits with varying system pressures demands. A small flow pilot version of the normally closed proportional relief is also offered for piloting a larger logic element or vented relief valve. The normally closed relief defaults to a maximum pressure setting (i.e. 3000 psi) when there is no current applied.
OPERATION - With the solenoid coil de-energized, the pilot dart is held closed by the spring. As current is applied to the coil, the pilot dart is moved creating less restriction of the pilot flow. As this restriction is reduced with the increasing current, the pressure setting also decreases. Once a constant electronic signal is given, the pilot dart is held in a given position, holding the pressure setting. This is maintained by the balance between the electronic spring force and the inlet pressure.
Normally Open Proportional Relief Valve
Normally open proportional relief valves are used to electronically control the system pressure. These valves are ideal for circuits with varying system pressure demands. A small flow pilot version of the normally open proportional relief is also offered for piloting a larger logic element or vented relief valve. The normally open relief defaults to minimum system pressure (i.e. 150 psi) when there is no current applied. Normally closed versions are also available upon request.
OPERATION - With the solenoid coil de-energized, the pilot dart is held open by the spring. This allows the main spool to open at minimum pressure 10.4 Bar (150 psi). As current is applied to the coil, the pilot dart is moved towards the pilot seat restricting pilot flow. This restriction raises the effective pressure setting of the valve. Once a constant electronic signal is given, the pilot dart is held in a given position, holding the pressure setting. This is maintained by a balance between electronic spring force and inlet pressure. As the electronic signal is reduced, the pilot dart is moved away from the pilot seat. This lowers the effective pressure setting of the valve.
Parker’s normally open series of Proportional Relief Valves include the following product families:
Series Flow Pressure Ranges
AP02B2YP .35 gpm-1.4 gpm 1000 psi – 5000 psi
AP04G2YP 25 gpm 1500 psi – 5000 psi
Parker’s normally closed series of Proportional Relief Valves include the following product families:
Series Flow Pressure Ranges
AP02B2YR 0.5 gpm-1.4 gpm 1000 psi – 5000 psi
AP04G2YR 25 gpm 1500 psi – 5000 psi
Proportional relief valves are used in conjunction with larger valves to achieve high flow, proportional pressure control, or with the AP04G2YP can be used as a stand-alone pressure control valve.
Commonly found markets include, but are not limited to mobile construction equipment, aerial devices, industrial specialty machinery, and hydraulic power units. -
Directional Control Proportional Valves
Parker’s 4-way, 3-position spool-type proportional directional control valves allow for actuator speed and direction control in a single cartridge. Varying current to one of two coils will create a proportional flow out to one of the actuator ports allowing control of speed, acceleration, and deceleration. The second coil controls proportional flow in the opposite direction. AC and DC coil options are available, along with a wide range of connection types. Current Controlled Pulse Width Modulation (PWM) valve drivers are preferred as they adjust for variations in coil temperature and also provide the ability to apply a dither frequency.
GP02 proportional valves are designed to fit in a common C08-4 cavity and they are available in low, standard, or high flow versions. The High flow cylinder spool configuration is capable of flows up to 5.5 GPM (21 LPM). A high flow motor spool is available for flows up to 4.5 GPM (17 LPM.) Standard and low flow versions are offered to allow for greater resolution depending on the maximum flow rate of the application. All GP02 versions are capable of pressures as high as 5000 PSI (350 BAR) and are available with manual overrides.
DSP105 proportional valves are designed to fit in a common C10-4 cavity and they are capable of flows up to 8.5 GPM (32 LPM) and pressures up to 3000 PSI (210 BAR.) Motor and cylinder spool configurations are available and manual overrides are optional.
Combined with Parker’s wide range of Coil options, the 4-way proportional spool valve offering allows for application specific solutions in the most demanding applications and markets including: Power Units, Oil and Gas, Material Handling, Construction, Drills, Presses, Mixers, Agriculture, Balers, Combines, Double Acting Cylinder Control, Bi-Direction Motor Control, Circuit Selectors, etc. -
2 Way Flow Control Proportional Valves
Parker’s selection of 2-way flow control proportional valves provide repeatable and precise controls to circuits requiring proportional flow control through a single line in a normally-open or normally-closed configuration. These valves are capable of handling flows up to 227 lpm (60 gpm) and pressures as high as 210 bar (3000 psi). These valves can achieve pseudo pressure compensation in both normally-open and normally-closed versions due to the pressure drop across the spool orifices, but an external compensator can also be used if finer control is required, making these valves ideal for variable applications that need exact control and do not demand the exact same flow every time a function is operated. Parker’s 2-way flow control proportional valves pair well with any Current Controlled Pulse Width Modulation (PWM) valve driver and can be used on a variety of mobile and industrial applications within the agriculture, construction, and manufacturing markets.
Markets:
• Agriculture
• Construction
• Material Handling
• Miscellaneous Industrial
• Miscellaneous Manufacturing
• Miscellaneous Mobile
Features/Benefits:
• Low hysteresis
• Hardened working parts for maximum durability
• All external parts zinc plated
Applications:
• Applications requiring precise controls
• Variable flow applications
Additional Technical Insight:
Recommended to be used with a Current Controlled Pulse Width Modulation (PWM) valve driver. -
4 Way 3 Position Spool Type Solenoid Valve
Parker’s readily available Winners Circle line includes a common cavity C10-4 direct acting 4-way, 3-position spool valve capable of flows up to 7 GPM (26 LPM) and pressures as high as 3600 PSI (250 BAR). The DSL105 cartridge valve is available with multiple spool variations including Cylinder/Blocked-Center, Open-Center, Tandem-Center, and Motor-Center. Direct acting spool valves are fast to respond to coil voltage and can quickly re-direct or block flow to actuator ports. Some leakage will be present due to spool clearances.
In addition to the Winners Circle product, Parker also offers the direct acting 4-way, 3-position 4.5 GPM (17 LPM) GS02 and 11 GPM (42 LPM) GS04 series of valves which are both capable of pressures as high as 5000 PSI (350 BAR.) Both series are available with multiple spool variations including Cylinder/Blocked-Center, Open-Center, Tandem-Center, and Motor-Center. All versions are available with optional manual overrides.
Parker also offers a 15 GPM (57 LPM) 5000 PSI (350 BAR) direct acting 4-way, 3-position spool valve for applications that require higher flow rates. DSH125 cartridge valves are available with multiple spool variations including Cylinder/Blocked-Center, Open-Center, Tandem-Center, and Motor-Center. All versions come standard with manual overrides.
Combined with Parker’s wide range of Coil options which include AC and DC voltages and extensive termination options, the 4-way direct acting spool valve offering allows for application specific solutions in the most demanding applications and markets including: Power Units, Oil and Gas, Material Handling, Construction, Drills, Presses, Mixers, Agriculture, Balers, Combines, Double Acting Cylinder Control, Bi-Direction Motor Control, Circuit Selectors, etc. -
Directional Control Valve - D1VW Series
Series D1VW directional control valves are high performance on/off direct operated hydraulic valves. These are wet armature design solenoid valves in either 2 position or 3 position configurations. The valve can be used as either a 3 way or 4 way The D1VW valve conforms to D03 (NG6) mounting pattern. There are 15 solenoid voltage options including DC, DC rectified and true AC voltages. There are 9 basic termination options including DIN, Deutsch, conduit box with wires and conduit box with plug-in coils. The conduit box with plug-in coils also allows for connections including terminal strip, Manaplug (Brad Harrison) and micro connection (M12 connector). D1VW valves are available with other options such as soft shift tubes (4 orifice size options), monitor switches, extended manual over rides and surge suppression diodes. DIN connector and Conduit box connections provide an IP65 (NEMA 4) ingress rating
The D1VW valve is well suited for both the industrial and mobile applications. Painted bodies and Deutsch connectors are offered for tough environment applications.
• Soft shift available
• 19 standard spool styles are available (for others please check with the factory)
• Proportional spools for added soft shift capability.
• Explosion proof solenoids are available in ATEX, and CSA/UL
• Extended manual over ride option
• Nitrile or Fluorocarbon seals are offered.
• AC and DC lights are available
• CSA Approval -
Kierunkowy zawór regulacyjny z czujnikiem obciążenia — seria...
Model VP120 firmy Parker zapewnia dokładność, możliwość sterowania, gęstość mocy, wytrzymałość i wszechstronność wszędzie tam, gdzie wydajność i efektywność są koniecznością. Może być stosowany jako system podziału przepływu z wykrywaniem obciążenia, a także jako system wykorzystujący pompy nieskompensowane i pompy o stałym wydatku z wykrywaniem obciążenia.
Rynki:
• Podnośniki osobowe
• Sprzęt budowlany
• Maszyny leśne
• Sprzęt do transportu materiałów
• Przemysł kolejowy
• Inne urządzenia mobilne
Cechy/zalety:
• Podział przepływu z kompensacją końcową.
• Uruchamianie ręczne, pilotem hydraulicznym i za pomocą EH.
• Różnorodne suwaki standardowe i niestandardowe.
• Ograniczanie ciśnienia z podziałem przepływu.
• Wbudowany układ generowania ciśnienia sterującego.
• Zwiększona ochrona antykawitacyjna.
Zastosowania:
• Żuraw kopiący
• Leśny ciągnik zrywkowy
• Żurawie chwytakowe leśne
• Sprzęt do konserwacji torowisk
• Miniładowarki
• Pojazdy do odśnieżania i odladzania
• Układy kierownicze
• Ładowarki teleskopowe -
Pressure Compensated Directional Control ValveSeries VP/VPO
The VP/VPO Series is a stackable, multi-section, load-sensing, pressure-compensated directional valve for mobile machines such as digger derricks, drill rigs, forklift trucks, continuous miners, platform trucks, and pumpers.
The valve can be given excellent simultaneous-operating characteristics, which enable several machine functions to be operated at the same time, regardless of the sizes of individual loads.
To facilitate precise customization for different applications, the VP/VPO Series is of wholly modular construction.
• The total modularity of the VP/VPO Series gives unique opportunities to integrate a wide range of normally external functions into the valve. Such functions can be common or specific to individual spool-sections, so that widely differing criteria for individual machine functions can be met in just one valve.
This enables compact, tailored logical, pre-tested, service-friendly system solutions to be created for many different types of machines.
• The spools in the VP/VPO Series can be actuated directly by means of levers or remotely by hydraulic or electro-hydraulic remote control.
The wide range of actuating options gives the machine designer great freedom in terms of control criteria and component location.
• 9 standard flow ratings with adjustable compensators to tailor exact actuator speeds.
• Pressure Limiters provide greater efficiency reducing heat saving horsepower.
• The VP/VPO Series has several Explosion Proof solenoids to adapt to your harsh environments; MSHA, CSA, IECEx
• The VP/VPO Series can be supplied in combination of 1 – 12 spool sections. The maximum recommended flow rate per spool section is 208 lpm.
• Transition adapters allow VP/VPO Series to be combined with VPL Series to simplify plumbing and reduce envelope size. -
Pressure Compensated Directional Control Valve Series VPL
The valve can be given excellent simultaneous-operating characteristics, which enable several machine functions to be operated at the same time, regardless of the sizes of individual loads.
To facilitate precise customization for different applications, the VPL Series is of wholly modular construction.
• The total modularity of the VPL Series gives unique opportunities to integrate a wide range of normally external functions into the valve. Such functions can be common or specific to individual spool-sections, so that widely differing criteria for individual machine functions can be met in just one valve.
This enables compact, tailored logical, pre-tested, service-friendly system solutions to be created for many different types of machines.
• The spools in the VPL Series can be actuated directly by means of levers or remotely by hydraulic or electro-hydraulic remote control.
The wide range of actuating options gives the machine designer great freedom in terms of control criteria and component location.
• 8 standard flow ratings with adjustable compensators to tailor exact actuator speeds.
• The VPL Series has several Explosion Proof solenoids to adapt to your harsh environments; MSHA, CSA, IECEx
• The VPL Series can be supplied in combination of 1 – 14 spool sections. The maximum recommended flow rate per spool section is 114 lpm. -
Mobile Directional Control ValvesSeries VP170
The VP170 series is a high performance, high durability product which lends itself to applications in which long life and accuracy are inherent. This valve can be designed to fit into a load sense system application and can also be configured with post compensation to allow for flow sharing when pump over demand is required. The valve series is sectional in design and has a wide variety of options for maximum flexibility to fit the needs of the marketplace. There are a variety of actuation types available such as manual, hydraulic pilot, pneumatic and electro-hydraulic. Along with these options there is a large variety of spool and port accessory options to fit every need. The VP170 also comes well equipped with special features. The VP170 truly leads the market place with a high endurance design for maximum flow and minimum energy loss. -
Mobile Directional Control ValvesSeries PC55
The PC55 series is a high performance, high durability product which lends itself to applications in which long life and repeatability are required. This valve can be designed to fit into a load sense post compensated system application. With post compensation this valve series allows for flow sharing when pump over demand is required. The valve series is sectional in design there are a variety of actuation types available such as manual, hydraulic pilot, pneumatic and electro-hydraulic. Along with these options there is a large variety of spool and port accessory options to fit every need. For decades the PC55 leads the market place with a superior design. -
Cam Operated Directional Control Valve Series D1VC, D1VD, D1VG
Series D1VC, D1VD and D1VG directional control valves are high performance, 4-chamber, direct operated, cam controlled, 4-way valves. They are available in 2-position and conform to NFPA’s D03, CETOP 3 mounting patterns.
Features
• Choice of 2 cam roller positions (D1VC and D1VD)
• Two styles available (D1VC and D1VG)
• Short stroke option -
Air Operated, Directional Control Valve SeriesD101VA
Series D101VA directional control valves are 5-chamber, air pilot operated valves, which are available in 2 or 3-position styles. These valves are manifold or subplate mounted, and conform to NFPA's D10, CETOP 10 -
Air Operated Directional Control Valve Series D31DA, D31VA
Series D31*A directional control valves are 5-chamber, air pilot operated valves. The valves are suitable for manifold or subplate mounting.
Features
• World design – Available worldwide.
• Mounting bolts below center line of spool – Minimizes spool binding.
• Five chamber style – Eliminates pressure spikes in tubes, increasing valve life.
• High pressure and flow ratings – Increased performance options in a compact valve -
Lever Operated Directional Control Valve SeriesD31DL, D31VL
Series D31*L directional control valves are 5-chamber, pilot operated, lever controlled valves. The valves are suitable for manifold or subplate mounting.
Features
• World design – Available worldwide.
• Mounting bolts below center line of spool – Minimizes spool binding.
• Five chamber style – Eliminates pressure spikes in tubes, increasing valve life.
• High pressure and flow ratings – Increased performance options in a compact valve. -
Air Operated Directional Control Valve Series D3A
Series D3A directional control valves are high performance, 4-chamber, direct operated, air pilot controlled, 4-way valves. They are available in 2 or 3-position and conform to NFPA’s D05/CETOP 5 mounting patterns.
Features
• Low pilot pressure required – 4.1 Bar (60 PSI) minimum.
• High flow, low pressure drop design. -
Cam Operated Directional Control Valve Series D3C, D3D
Series D3C and D3D directional control valves are high performance, 4-chamber, direct operated, cam
controlled, 3 or 4-way valves. They are available in 2-position and conform to NFPA’s D05, CETOP 5
mounting patterns.
Features
• Choice of 2 cam roller positions (D3C and D3D).
• Short stroke option.
• High flow, low pressure drop design. -
Lever Operated Directional Control Valve Series D3L, D3LB
Series D3L directional control valves are high performance, 4-chamber, direct operated, lever controlled,
4-way valves. They are available in 2 or 3-position and conform to NFPA’s D05, CETOP 5 mounting patterns.
Features
• Spring return or detent styles available.
• High flow, low pressure drop design.
• Heavy duty handle design. -
Lever Operated Directional Control Valve Series D61VL
Series D61VL directional control valves are 5-chamber, lever operated valves, which are available in 2 and 3-position styles. They are manifold or subplate mounted valves, and conform to NFPA’s D08, CETOP 8 mounting patterns. -
Air Operated Directional Control Valve Series D81VA
Series D81VA directional control valves are 5-chamber, air pilot operated valves, which are available in 2 or 3-position styles. These valves are manifold or subplate mounted, and conform to NFPA’s D08, CETOP 8 mounting pattern. -
Lever Operated Directional Control Valve Series D101VL
Series D101VL directional control valves are 5-chamber, lever operated valves, which are available
in 2 or 3-position styles. These valves are manifold or subplate mounted, and conform to NFPA’s D10,
CETOP 10 mounting pattern. -
Lever Operated Directional Control Valve Series D81VL
Series D81VL directional control valves are 5-chamber, lever operated valves, which are available in 2 or 3-position styles. These valves are manifold or subplate mounted, and conform to NFPA's D08, CETOP 8 mounting pattern. -
Pilot Operated, Solenoid Controlled, Directional Control Valve...
Series D101V directional control valves are 5-chamber, pilot operated, solenoid controlled valves. They are available in 2 or 3-position styles. These valves are manifold or subplate mounted, and conform to NFPA’s D10, CETOP 10 mounting pattern.
Features
• Low pressure drop design.
• Hardened spools provide long life.
• Fast response option available.
• Wide variety of voltages and electrical connection options.
• Explosion proof availability.
• No tools required for coil removal. -
Oil Operated Directional Control Valve Series D10P
Series D10P directional control valves are 5-chamber, pilot operated valves. They are available in 2 or
3-position styles. These valves are manifold or subplate mounted, and conform to NFPA’s D10, CETOP 10 mounting pattern.
Features
• Low pressure drop design.
• Hardened spools provide long life. -
Solenoid Operated Directional Control Valve SeriesD3DW
Series D3DW directional control valves are high performance, 5-chamber, direct operated, wet armature, solenoid controlled, 3 or 4-way valves. They are available in 2 or 3-position and conform to NFPA’s D05, CETOP 5 mounting patterns.
Features
• 22 spools available including proportional.
• DC surge suppression available to protect electrical equipment.
• Easy access mounting bolts.
• CSA approved.
• No tools required for coil removal.
• High pressure tank line capability.
• Monitor switch available. -
Pilot Operated Directional Control Valve Series D61VW
Series D61VW directional control valves are 5-chamber, pilot operated, solenoid controlled valves.
They are available in 2 or 3-position styles. These valves are manifold or subplate mounted, and conform
to NFPA’s D08, CETOP 8 mounting patterns.
Features
• Low pressure drop design.
• Hardened spools provide long life.
• Fast response option available.
• Explosion proof availability.
• Wide variety of voltages and electrical connection options
• No tools required for coil removal. -
Oil Operated Directional Control Valve Series D6P
Series D6P directional control valves are 5-chamber, pilot operated valves. They are available in 2 or 3-position styles. These valves are manifold or subplate mounted, and conform to NFPA’s D08, CETOP 8 mounting patterns.
Features
• Low pressure drop design.
• Hardened spools provide long life.
• Fast response option available. -
Pilot Operated Directional Control Valve SeriesD81VW
Series D81VW directional control valves are 5-chamber, pilot operated, solenoid controlled valves. They are available in 2 or 3-position styles. These valves are manifold or subplate mounted, and conform to NFPA’s D08, CETOP 8 mounting pattern.
Features
• Low pressure drop design.
• Hardened spools provide long life.
• Fast response option available.
• Wide variety of voltages and electrical connection options.
• Explosion proof availability.
• No tools required for coil removal. -
Oil Operated Directional Control Valve Series D8P
Series D8P directional control valves are 5-chamber, pilot operated valves. They are available in 2 or
3-position styles. These valves are manifold or subplate mounted, and conform to NFPA’s D08, CETOP 8 mounting pattern.
Features
• Low pressure drop design.
• Hardened spools provide long life. -
Pilot Operated Directional Control Valve Series D31DW, D31VW
Series D31 directional control valves are 5-chamber, pilot operated, solenoid controlled valves. The valves are suitable for manifold or subplate mounting.
Features
• World design – Available worldwide.
• Mounting bolts below center line of spool – Minimizes spool binding.
• Five chamber style – Eliminates pressure spikes in tubes, increasing valve life.
• High pressure and flow ratings – Increased performance options in a compact valve. -
Mobile Directional Control Valves Series V10
The V10 Series valves are sectional directional control valves that provide parallel or tandem circuit operation for open center and closed center systems. Work sections are offered in parallel and tandem with individual load (reverse flow) checks that are available for open center, closed center and power beyond applications.
Features
• 3-Way, 4-Way and 4-Way Float operation
• Numerous manual spool positioner options plus remote hydraulic or electric solenoid operation
• Work port relief valves and anti-cavitation check valves
• Single handle or dual function mechanical joystick control of manual sections
• Enclosed spool ends with handles
• Long life - low friction spool seals
• Low flow and high flow spool options available offering flows to 15 GPM (45 LPM)
• Continuous system operating pressures to 3500 PSI (Work port pressures to 5000 PSI) -
Mobile Directional Control Valves Series V20
The V20 Series valves is a stack type valve that allows versatility in porting using the various combinations of work sections. The V20 valve is available for use in open center, closed center and load-sensing type work sections. Manually operated, hydraulic remote operated and solenoid controlled may be intermixed in the same valve assembly. A manual lever option allows for full control of the valve and is ideal for applications where two control stations are required.
Features
• 3-Way, 4-Way and 4-Way Float operation
• Numerous positioner options, including remote hydraulic or electric solenoid operation
• Spools are hard, chrome plated for long life and resistance to corrosion
• Work port relief valves and anti-cavitation check valves
• Enclosed spool ends with handles
• Continuous system operating pressures to 3500 PSI
• Easy field conversion or section replacement -
Mobile Directional Control Valves - VA_VG35 Series
The VA/VG35 valves are sectional, stack type, construction assembled with one or more work sections capped by inlet and outlet sections. Working sections are offered in many functional types and are designed with large internal passages with uniform cross sections and smooth wall surfaces which provide flow paths free of abrupt angles. Work sections can be provided with full-flow relief valves in either or both work ports. Port relief valves can be pilot operated with anti-cavitation checks or differential area, full-flow relief valves without anti-cavitation checks. Crossover reliefs are also available.
Features
• Built-in full flow relief valves
• Parallel and series circuits in one bank
• Manual, hydraulic, electric, or pneumatic operation
• Sectional construction for maximum flexibility
• Spool changeover capability for right or left handed valve assemblies
• Low spool effort – improved metering -
Mobile Directional Control Valve Series V20EH
The V20EH is a sectional, open center, directional control valve for mobile machines.
• Offered in two work port sizes; SAE10 and SAE12
• A global solenoid (pwm) that can be used for proportional or on/off control. The coils have a molded on Amp Jr. or Deutsch connector.
• Work sections rated to 240 Bar (3500 PSI): 4-way, 3-position; and 3-way, 3-position
Benefit
The pressure required to move the spools is generated and regulated internal to the V20 valve
Minimal impact on open-center pressure drops when the main spools are in neutral
There is an option to have the mechanical buildup for full on-time operation
A dedicated solenoid drain to the reservoir optimizes solenoid performance.
An extended bonnet for screw-adjustable work port relief valves
Handle with manual override -
Mobile Directional Control Valve Series VG35EH
The VG35EH is a sectional, open center, directional control valve for mobile machines.
• It is rated at 3500 PSI inlet and 65 GPM maximum pump flow.
• The standard maximum workport size is SAE-16.
• The inlets are typically ported SAE-20 and the outlets SAE-24.
• Standard actuation method is EH electro-hydraulic, and can be proportional or On/Off. Traditional actuation methods can also be mixed with EH.
• A pilot source is necessary for solenoid actuation. If required, a pilot generation section is available to be placed after the inlet.
Feature
Outstanding pressure drop and balance
Differential area main relief valves
Long spool stroke @ 0.41”
Benefit
Minimizes heat generation especially when retracting cylinders
Dirt tolerant, quick response
Provides excellent feathering control and low spool forces -
Oil Operated Directional Control Valve - D3P Series
Parker’s D3P directional control valves are available in 2 or 3-position. They are manifold or subplate mounted valves which conform to NFPA’s D05, CETOP 5 mounting patterns.
Markets
• Entertainment Automation
• Factory Automation
• Lumber & Wood
• Machine Tools
• Marine
• Material Handling
• Miscellaneous Industrial
• Miscellaneous Manufacturing
• Miscellaneous Processing
• Molding
• Oil & Gas
• Other Natural Resources
• Packaging Machinery
• Plastic Packaging
• Power Generation
• Primary Metal Refining/Process
• Printing and Marking Equipment
• Rubber & Tire Processing
• Vehicle Assembly Facilities
Features/Benefits
• Low pressure drop design
• Hardened spools provide long life
Applications
• Suitable for general hydraulic applications -
Mobile Directional Control Valve - Serires FLV95
FLV95 has a wide range of selectable functions, offering great flexibility in terms of system structure in simple as well as advanced hydraulic system solutions. FLV95 is a result of Parker’s wide experience in mobile hydraulics, offering excellent performance, made with high grade materials and precision manufacturing. FLV95 can be equipped with manual spool actuators. Each valve section can be optimized for its particular function in the machinery.
The FLV95 hydraulic valve can be constructed in many different designs with different inlet sections and work sections which can afford multiple functions in dual flow divider, lift/tilt hydraulic lock and lowering flow regulation.
Markets:
–––• Material Handling Equipment
Features/Benefits:
–––• Precise control
–––• Productivity and energy efficiency
–––• Robust
–––• System valve-Designed for optimal system solutions . Also safety features such as inlet with power shut off.
Applications:
–––• Forklift -
Mobile Directional Control Valve - Serires KM300
KM300 control valve is designed for tough operating conditions and intended to be used in mobile hydraulic open center systems. KM300 is a monoblock valve with two or three main spools. KM300 is a result of Parker's wide experience in mobile hydraulics, offering excellent high grade materials and precision manufacturing.
Good machine design and the right hydraulic system gives a cost-effective installation, which in turn gives a competitive product. The pump and work ports in the KM300 are arranged in such a way that hosing and piping can be kept to an absolute minimum. The valve is equipped with double work ports at 180°, which eliminates T-connectors and gives the shortest and simplest path to the cylinders. This also enables dimensions to be kept small, since only half the flow passes through each work port.
The KM300 is of robust construction. Many of the components are of the cartridge or module types, which makes servicing easy.
KM300 can be actuated hydraulically and is equipped with possibility of forth position float function.
Markets:
–––Construction Equipment
Material Handling Equipment
Mining
Features/Benefits:
Good energy efficiency: low pressure drops for high function speeds; low energy consumption.
Easy to install: designed with simple installation in mind.
Optional float-position function: built-in, pressure-controlled float-position function.
Great precision: low hysteresis gives precise control and good operator comfort.
Easy to service
Long service life: efficient port-relief and anti-cavitation valves reduce the number of pressure peaks and cavitation in the system, thus prolonging the life of the machine.
Quality materials and great precision in manufacturing, assembly and test to ensure that you will get a quality product with low internal leakage and long service life.
Applications:
Wheel Loaders
Fork lift trucks
Mining Loaders
Reach stackers