Napędy DC
Parker offers a full range of drives including stepper, compact and high performance servo, AC variable speed, high current output DC and panel mounted drives. Parker industry leading drives include Sensorless, Vector and Microstepping opti
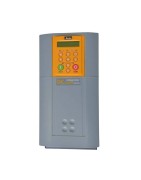
-
DC Motor Speed Controllers - DC506/507/508 Series
The 506, 507 and 508 series 1-quadrant DC drives break new ground in cost-effective DC motor control. Available in 3, 6 or 12 A armature ratings, with power ratings up to 2HP, the feature packed minimum footprint design is ideal for speed or torque control of permanent magnet or shunt wound DC motors fed from single phase supplies. Typical applications include conveyors, basic speed control and packaging machinery
Features:
• Low-cost / high-featured design
• IP20 protected covers
• Compact footprint and DIN rail mounting
• Selectable 110 VAC or 230 VAC supply
• Selectable tacho or armature voltage feedback
Standards:
• CE Marked to EN50178 (Safety, Low Voltage Directive)
• CE Marked to EN61800-3 (EMC Directive) with external filter
• NRTL Listed to US Standard UL508C
• NRTL listed to Canadian standard C22.2#14
Technical Specifications:
Power Supply:
Single Phase
110-120 VAC ± 10 %, 50-60 Hz ± 5%
220-240 VAC ± 10 %, 50-60 Hz ± 5%
Output Current Ratings:
3A (506) / 6A (507) / 12A (508)
Available Field Current:
up to 2A DC
Environment:
0-45°C / 32-113°F
Up to 1000m ASL (derate 1% per 100m to 2000m maximum)
Protection:
IP20
Speed Feedback:
- Tachogenerator / - Armature Voltage Feedback
Control Signals:
- Zero Speed / - Drive Healthy / - Speed Feedback
Motor Protection:
- Stall condition 15 seconds internal
- Electronic Overload Protection
Potentiometers:
- Maximum Speed
- Minimum Speed
- Acceleration Rate (1-15s)
- Deceleration Rate(1-15s)
- Stability
- I.R. Compensation
- Current Limit (0-100%)
Options:
- EMC filters
- Line reactors for European and North American markets (UL-CSA) -
DC Motor Speed Controllers - DC512C Series
Isolated control circuitry, a host of user facilities and extremely linear control loop makes the 512C series 2-quadrant DC drives ideal for single motor or multi-drive low power applications. Designed for use on single phase supplies, the 512C is suitable for controlling permanent magnet or field wound DC motors in speed or torque control. It can be used “open loop” with armature voltage feedback or with DC tacho feedback for enhanced regulation and speed range. Chassis mount IP00 rated, with output ratings up to 32A/10HP, typical applications include centrifugal fans and pumps, extruders and mixers, plus small paper converting machines.
Features:
• Fully isolated control circuits
• 110 V ... 415 V supply selection by jumpers
• CE marked and EMC compliant
• Multiple input speed and current setpoints
• Zero speed and drive healthy outputs
• Extremely linear control loops
Standards
• CE Marked to EN50178 (Safety, Low Voltage Directive)
• CE Marked to EN61800-3 (EMC Directive) with external filter
• NRTL Listed to US Standard UL508C
• NRTL listed to Canadian standard C22.2#14
Technical Specifications:
Power Supply:
Single Phase
110-120VAC ± 10 %, 50-60 Hz ± 5%
220-240VAC ± 10 %, 50-60 Hz ± 5%
380-415VAC ± 10 %, 50-60 Hz ± 5%
Output Current Ratings:
4A / 8A / 16A / 32A
Overload:
150% for 60 seconds
Available Field Current:
up to 3A DC.
Environment:
0-40°C / 32-104°F
Up to 1000m ASL
Protection:
IP00
Speed Feedback:
- Tachogenerator / - Armature Voltage Feedback
Analogue Inputs:
- Speed Reference / - Auxiliary Speed Reference / - Tachometer Feedback Option
- Current Limit / - Minimum Speed
Analogue Outputs:
- Speed / - Load / - Ramp Output / - Total Reference / - Reference Voltage ±10V
Digital Inputs:
- Run (Active) / - Stall Enable
Digital Outputs:
- Zero Speed / - Health
Potentiometers:
- Maximum Speed
- Minimum Speed
- Acceleration Rate (1-40s)
- Deceleration Rate(1-40s)
- Stability
- I.R. Compensation -
DC Motor Speed Controllers - DC514C Series
The regenerative 514C DC thyristor drive offers full four quadrant control of DC motors from single phase supplies. As such it is ideal for applications involving overhauling loads or where rapid and accurate deceleration is required. Together with the non-regenerative 512C they offer the perfect solution for lower power single motor and multi-drive applications. The 514C can be used “open loop” with armature voltage feedback, or with DC tach feedback for enhanced regulation and speed range. Chassis mount IP00 rated, with output ratings up to 32A/10HP, typical applications include machine tool spindles, wire drawing machines and winders/reelers.
Features:
• Four quadrant regenerative control
• 110...500 VAC AC supply selection by jumpers
• CE marked and EMC compliant
• AC power contactor logic and supply
• Many system features
• Extremely linear control loops
User Facilities:
• Four quadrant regenerative control
• Seperate AC auxiliary supply
• AC supply contactor logic
• Torque or speed control
• Three setpoint and torque limit inputs
• Buffered analogue current output (10V, 10mA)
• +10V and -10V analogue reference supplies
• +24V digital reference supply
• Drive healthy output
• Buffered speed & ramp output (10V, 10mA)
• Buffered total setpoint output (10V, 10mA)
• Zero speed / zero setpoint output
Potentiometer Adjustments:
• Maximum speed / Current limit
• Acceleration time and Deceleration time (0...40 s)
• IR Compensation
• Speed loop gain - proportional and integral
• Current gain - proportional and integral
• Zero speed offset or threshold
Standards:
• CE Marked to EN50178 (Safety, Low Voltage Directive)
• CE Marked to EN61800-3 (EMC Directive) with external filter
• NRTL Listed to US Standard UL508C
• NRTL listed to Canadian standard C22.2#14
Technical Specifications:
Power Supply:
Single Phase
110-120VAC ± 10 %, 50-60 Hz ± 5%
220-240VAC ± 10 %, 50-60 Hz ± 5%
380-415VAC ± 10 %, 50-60 Hz ± 5%
Output Current Ratings:
4A / 8A / 16A / 32A
Overload:
150% for 60 seconds
Available Field Current:
up to 3A DC.
Environment:
0-40°C / 32-104°F
Up to 1000m ASL
Protection:
IP00
Motor Protection:
- Stall Condition 15 sec Internal / - Electronic Overload Protection
Speed Feedback:
- Tachogenerator / - Armature Voltage Feedback -
DC Motor Speed Controller - DC590PR Series
The DC590PR is a newly developed compact DC motor drive. With its state-of-the-art advanced 32-bit control architecture, the DC590PR drive delivers highly functional and flexible control suited to a whole host of industrial applications. It has a range of interface options which are compatible with the most common feedback devices, enabling simple motor control through to the most sophisticated multi-motor system. Armature voltage feedback is standard without the need for any interface option.
• The best flexibility for application development:
The best flexibility for application development, DC590PR inherits from over 40 years of DC motor application knowledge and motor control experience, simplify the operation by typical application block and offers more flexible program blocks.
• Latest technology & algorithm:
New introduced USB interface offers more friendly connection. With its self-tuning algorithm, the DC590PR can be configured Q/4Q and frame size within minutes.
• 590PR higher performance:
High resolution current feedback (0.06%) supplies more stable control performance. The operator interface allows easy monitoring of machine operation and simplifies maintenance.
Standardize with DC590P the same powerful function block programming software DSElite and the same feedback options and communication fieldbus: Profibus-DP, CANopen, Modbus+, Ethernet and DeviceNet.
• Keep I/O same as DC590P • Input voltage is upto 500V • Provide internal field current • Keep external field current connectors
-
598G/599G DC Drive External Stack Controller
External Stack Controller-598G/599G could build up to 1440A External DC Drive in one frame size. The equipment described is intended for an industrial (non-consumer) user, for the control of an external thyristor controlled bridge. The design assumes that a 2-phase field semi-controlled Rectifier Bridge and a fully controlled 3-phase Six Pulse Converter exists, which is complete with Thyristor Suppression, Current Feedback, Temperature Monitoring and suitable fusing.
The External Stack Controller Module provides:
• Thyristor Firing Signals and Pulse Transformers
• Field Power Thyristor Firing Signals and Pulse Transformers
• ACCT Feedback Rectification and Scaling
• Field CT Feedback Rectification and Scaling
• Armature Voltage Feedback Interface
• Field Voltage Feedback Interface
• Mains Present Monitoring
• Heatsink Over-temperature Input
• All Standard 590C I/O Terminations