Kołnierze hydrauliczne
Hydraulic flange connections are used in the most demanding applications, as they are well suited for high pressure, shock and vibration, especially in larger sizes. Flanges allow easy connection between hose and tube/pipe where flexibility
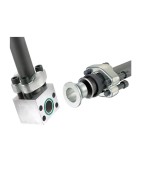
-
Dual Seal Subsea Flange Adapters
Parker’s innovative Dual Seal Flange Adapters improve the reliability of high-vibration, high-shock hydraulic four-bolt connections in critical oil and gas applications. Incorporating both radial and face seal technologies, which reduces the potential for system leakage and air or water ingression caused by side loading of traditional flange face seal connections.
Markets:
• Oil & Gas
Features/Benefits:
• NACE (National Association for Corrosion Engineers) MR0175 Compliant, and tested to 1 million impulse cycles for proven reliability.
• Designed to conform to bolt thread and bolt pattern dimensions of ISO 6162-2 or SAE J518 Code 62.
• Over 28 port configurations available: SAE Straight Thread, Triple-Lok, Seal-Lok, Pipe, Weld Socket and Plugs.
• Available in 316/316L stainless steel with full heat code traceability in sizes ½”, 1” and 1 ½” with working pressures up to 7500 psi and 515 bar
Applications:
• Subsea
• BOP Stacks -
O-ring Face Seal, 37° Flare and Flareless Code 61 and 62...
Parker's flange adapters with 4-bolt flange connections conform SAE J518 and ISO 6162-1 and -2. These proven leak-free connections adapt to Parker's Seal-Lok™ O-ring Face Seal (ORFS), Triple-Lok® 37° flare, Ferulok® inch flareless fittings, and socket pipe weld, and have achieved world-wide acceptance.Markets:• Construction• Agriculture• Oil & Gas• Transportation• Mining• ForestryFeatures/Benefits:• Adapts to Parker's Seal-Lok O-ring Face Seal (ORFS), Triple-Lok 37° flare, Ferulok inch flareless fittings, and socket pipe weld.• Lower tightening torque required compared to that required for equivalent size threaded port, therefore smaller wrenches and wrench swing clearances needed--providing ease of assembly in tight quarters.• 13 configurations available, with custom designs available on request.• Ease of disassembly with use of split clamps.• Available in steel in sizes ¾” through 1 ½” with working pressures up to 5000 psi.Applications:• Hydraulic fluid and gas handling connections -
4-Bolt Hydraulic Flanges and Components
Parker's hydraulic flanges and components conform to SAE J518 and ISO 6162-1 and -2. These proven leak-free connections are suited for tube and pipe in larger sizes, and have achieved world-wide acceptance.
Markets:
• Construction
• Agriculture
• Oil & Gas
• Transportation
• Mining
• Forestry
Features/Benefits:
• Adapts BSPP, SAE Straight thread and NPTF, as well as tube and pipe weld connections.
• Lower tightening torque required compared to that required for equivalent size threaded port, therefore smaller wrenches and wrench swing clearances needed--providing ease of assembly in tight quarters.
• Ease of disassembly with use of split clamps.
• Over 60 configurations available, with custom designs available on request.
• Available in steel and stainless steel in flange sizes ½” through 3” with working pressures up to 6000 psi.
Applications:
• Hydraulic fluid and gas handling connections -
HPF - High Performance Flange System Flange Connection...
HPF is generally applicable for working pressures up to 420 bar. But the design opens the door to go even beyond this pressure rating: by choosing a suitable combination of flange, insert and tube the pressure rating can be increased to 500 bar.
The System is adjusted to standard tube dimensions with diameters from 25 to 150 mm and wall thickness up to 20 mm. It is designed for flange patterns according to ISO 6162-1 (SAE J518, code 61), ISO 6162-2 (SAE J518, code 62) and ISO 6164.
Markets:
• Environment
• Industrial
• Machine Tools
• Materials Handling
• Mobile
• Oil and Gas
• Power Generation
• Process
Applications:
• Suitable for general hydraulic and industrial applications.
Features/ Benefits of Parker High Performance Flanges:
• The Parker High Performance Flange System stands for total cost reductions! Compared to conventional welding, the High Performance Flange System leads to several time and cost benefits: The pipework fabrication is very fast and the installation time shorter compared to welding. X-ray is not necessary and there are no post-welding cleaning costs. The flushing costs are reduced as well.
• The Parker High Performance Flange System is worldwide available through the Parker distribution network.
• In addition to the product range, Parker offers value added service, because Parker is able to engineer your hydraulic application.
Learning from nature
The best solutions for complex design problems can often be
found in nature. The flaring of the HPF tube is similar to the shape of a branch where it joints the trunk of a tree: The tube is flared by hydraulic axial pressure giving it a parabolic shaping, increasing from 10° up to 37°. The initial gentle incline of the shaping guarantees additional safety against strong system vibrations. The DGUV confirms the capability of this unique, patented system especially for the use in hydraulic and mechanical presses as well as in hydraulic power systems for injection moulding machines. Beside that, the system is an ideal solution for marine and offshore applications. It is type approved by various classification societies like DNV/GL, BV and LR.
The HPF Connector - Strong teamwork for the toughest demands
HPF flanges are equipped with a specially designed and hardened inner grip contour, providing excellent additional tear-off safety for the connection. Optionally some sizes are equipped with special lockrings. A shaped insert is placed into the flared end of the tube. On the port side the sealing is guaranteed by a F37 Seal - which is a special profile seal - or an O-ring seal, on the tube side by an O-ring seal.
The F37 Seal was developed especially for the use with SAE
flanges. These special seals guarantee a high form stability.
Compared to standard O-Rings, their mechanical properties
prevent gap extrusion, even when the flanges “breathe” under
pressure. The special profile of the F37 Seal is ideally adapted to higer pressures or unsuitable surface finish of the flanges.
The application of these soft-sealing elements both on the port
side and tube side guarantees the gas leak tightness of the HPF
connector. As the insert does not have a toothed profile, it can
be easily assembled repeatedly.
Tube forming
The tube forming is performed by the Parflange® HPF machines; they can either be purchased or rented for a certain period of time. If required, assembly of ready-to-install straight or manipulated HPF tube lines can be carried out by a Parker CPS Piping Center.
Flanging instead of welding: Error-free and riskless assembly
Nowadays many tube connections are welded. However, as even the best welding operator may make a mistake, each welding seam has to be tested, leading to an enormous loss of time and a significant increase of costs. Even finding trained staffed may be critical. Apart from enormous time savings for the joint preparation itself, HPF offers various advantages compared to the welding solution:
• Welding galvanic zinc-plated tubes is always critical. With
HPF zinc-plated tubes can be used, there is no further painting
necessary.
• Welding seams must be descaled and often be stained. Dealing with this process and substances is an environmental
risk.
• Welded tubes need to be intensively cleaned inside. HPF tube
assemblies do not require any special cleaning, reducing flushing time and costs during initial system startup.
• The flanging process does not cause noxious gases, thus eliminating explosion risks and fire hazards.
• The HPF tube forming is a machined cold forming process.
Therefore there is no need for X-raying the connection.
Cr(VI)-free corrosion protection
All components do of course have surfaces which are free of
Cr(VI) platings. Parker is highly aware of its responsibility for
the environment and human health. Therefore Parker has completely renounced the use of Cr(VI) containing surfaces.
Personnel and environment-friendly
By comparing the individual operations for a welded line with
Parker flanges connected lines, significant cost savings opportunities become immediately obvious. No vapours putting health at risk are released, in contrast to conventional welding processes. Consequently, usage is possible in locations with high requirements such as, for example, offshore oil platforms.
In addition to this, flaring machine design errors in the preparation of flanges are virtually unknown. Stress corrosion cracking generated during welding operations is history and the life of the finished tubing system is increased. Cold formed Parflange® technologies save power and energy compared to welding and require neither degreasers nor anti-corrosion agents. When galvanized tubes are used, post-galvanization can be omitted because the zinc-coating is not impaired by flaring. Parker flange connector components are delivered in state of the art Cr(VI)-free surfaces.