Offline Hydraulic Filtration Systems
Parker’s offline hydraulic filtration systems are the most economical way to recondition hydraulic and lube oils in your system. Our diverse portfolio of stand-alone products remove equipment-damaging contaminants like solid partic
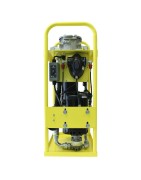
-
Portable Filtration System Guardian Series
New fluid is not necessarily clean fluid. Most new fluids (right out of the drum) are unfit for use due to high initial contamination levels. Contamination, both particulate and water, may be added to a new fluid during processing, mixing, handling and storage.
The bottom line - fluid should always be filtered before being put into use. The Parker Guardian Portable Filtration System offers a unique pump/motor/filter combination, designed for conditioning and transferring petroleum-based and water emulsion fluids. This unit protects systems from contamination added by new fluid. The Guardian also circulates and “polishes” existing fluid in systems to reduce the contamination to an acceptable level.
The Guardian is lightweight, compact, and hand-held, making it easy to carry and reach difficult areas. Fitting easily on a 55 gallon drum, this convenient unit and only requires one person to operate – saving labor costs.
There are literally hundreds of applications that the Guardian is suited for, with more being discovered each day. If your system is sensitive to the harmful effects of contamination, then the Guardian may be ideal for you.
Possible Applications:
• Ground Support
• Hydraulic Service
• Mining
• Mobile
• Industrial
• Marine
Features and Benefits:
• Lightweight, Hand Held, Compact Design that fits easily on 55 gallon drums, Which is Easy to Carry, Capable of Getting Into Hard to Reach Areas, and Only Requires One Person Operation
• A Flow Rate up to 4 GPM that Filters and Transfers Simultaneously Provides One Step Operation
• The Powerful Pump/Motor/Combination with Carboxylated Nitrile Seals are Standard, and Handles Fluids up to 16,000 SUS Viscosity, Providing Reliable Performance in a Wide Variety of Operating Conditions
• Built-in Relief Valve with no Downstream Fluid Bypass Ensures that Only 100% Filtered Fluid Reaches Downstream Components – Even When Unattended
• Wide Variety of Filter Elements Available, including High Capacity 2 Micron Absolute Disposable Microglass and 74 Micron Cleanable Wire and Water Removal, Which Maximizes Element Life Between Changes
• Clear, Wire-Reinforced Hose Assemblies with Wand Attachments, Requiring No Extra Hardware, Easy to Maneuver and Is Ready to Use
• Optional Quick Disconnect Hose Connections are Fast, Easy to Setup/Tear-Down, Which Eliminates Messy Drips
• Heavy-Duty Motor with Thermal Overload Protection, is UL Recognized and CSA Listed, Offering Safe, Reliable Performance, and is Field Serviceable
• Geroter Pump with Visible Serviceable Inlet Strainer Offers a Dirt Tolerant Design with Added Protection, Reliable in Highly Contaminated Fluids
• Its Quiet Operation (Less than 70dB Noise level at 3 ft.) Can be Used Almost Anywhere with Minimal Disturbance
• Convenient Inlet-to-Outlet Hose Connection Contains Fluids when Transporting, Offers Clean and Safe Operation
• Low Center of Gravity Provides Stability and Runs Reliably Unattended
• Dual Motor Seals Offers Added Motor Protection and Longer Motor Life
• Auxiliary Inlet/Outlet Ports Offer Flexibility – Able to be Used in Place of, or in Addition to, Standard Ports; Outlet can also be Used as a Sampling Port -
Submicronic Removal Fluid Purification Systems
The Parker SMR Series Submicronic Removal Fluid Purification System is the smart purification solution for fluid flow around 10 GPM (38 LPM). The SMR contains Parker patented Balanced Charge Agglomeration (BCA™) technology, which maintains hydraulic and lubricating fluids in optimum condition while preventing/removing the build-up of sludge and varnish.
Balanced Charge Agglomeration (BCA™) technology does not remove water, however with the removal of thousands of submicron particles; the majority of sites where water can readily attach are mitigated. Water is more easily separated and removed, improving demulsibility, or the ability to release water.
Demulsibility is an important factor to consider when hydraulic equipment operates in an atmosphere that is wet or humid. Food-processing operations, such as cooking oil, for example, provide significant exposure to water-based process fluids.
Because oil is hygroscopic, or able to absorb water, it is quite easy for water to saturate the oil. Water enters through any number of ways, and must be removed in order to protect a system’s operation. When demulsibility is diminished, the oil will become contaminated by the water, causing quick wear to the system’s components.
Maintaining a hydraulic system’s oil cleanliness level will increase the life of the critical wear components, and reduce system downtime. Portable purification units are ideal for systems in applications demanding on-site decontamination. With several models to choose from, the Parker SMR Series is an ideal solution for many hydraulic system’s needs.
This system is available in a PLC or simplified control version. Please contact a Parker Representative for assistance.
Balanced Charge Agglomeration (BCA™) - How the Technology Works:
Contaminated fluid is passed over a series of high-voltage electrodes, inducing a charge on the submicron particles of (+) and (-), then the particles continue down separate paths. (Note that particulate contamination as small as 0.1 microns are able to amass this charge). Oil, a non-conducting fluid, remains neutral. The two oppositely charged particle fluid streams are then re-combined. The oppositely charged particles are then mixed and are attracted to each other, forming larger particle clusters, growing in size as they agglomerate, or join together. Submicron particles grow into multiple micron-sized particle clusters. Once larger in size, the particle clusters are more efficiently filtered. Finally, the particle clusters are then sent through the system’s high efficiency filter to be removed.
Applications:
• Power Generation (such as: Steam/Gas Turbine, and Hydraulics/Lubrication)
• Oil & Gas (such as: Compressor/Turbine Hydraulics and Lubrication)
• Pulp & Paper (such as: Lube Oil and Hydraulics)
• Manufacturing (such as: Hydraulics, Lubrication, EDM, and Injection Molders)
• Others (such as: Cooking Oil, Gear Oil, Fuels, Bio Fuels, Steel, and Military)
Features:
• Contaminant Removal to the Sub-Micron Level
• Prevention and Removal of Sludge and Varnish
• Removal of Oxidation Byproducts and Biological Contamination
• Removal of Ferrous and Non-Ferrous Contaminants
The Parker SMR Benefit:
• Unmatched Fluid Purification and System Polishing
• Proven Varnish Removal
• PLC Control & Data Tracking
• OEM Approvals -
Portable Purification Systems PVS Series
Water is one of the most common contaminants in a fluid system and one of the most damaging. When water contaminates a system, it can cause many serious problems such as: corrosion, fluid breakdown, reduction of lubricating properties, additive precipitation, oil oxidation, reduced dielectric strength, and abrasive wear in hydraulic components.
Whether dissolved water (water which is absorbed into the oil) or free water (occurring when oil is too saturated* to hold any more water), solid particulate, or air/gasses, contaminated oil can be purified on-site using Parker's PVS Series Portable Purification System.
* Please Note that Temperature and Fluid type determines the saturation point for your
system (Please Refer to Brochure).
Maintaining a hydraulic system's oil cleanliness level will increase the life of the critical wear components, and reduce system downtime. Portable purification units are ideal for systems in applications demanding on-site decontamination. With several models to choose from, the Parker PVS Series is an ideal solution for many hydraulic system's needs.
Principles of Operation:
Contaminated oil is drawn into the Parker PVS Series Portable Purification System by a vacuum. The contaminated oil is then subjected to optimum vacuum, temperature, and increased surface area exposure. The optimum temperature is achieved using an in-line, low watt density heater. Afterward, the oil enters the distillation column, where it is exposed to the vacuum through the use of special dispersal elements, achieving the increased surface area exposure. This process converts water into water vapor, which is then drawn through the condenser by the vacuum pump.
The water-free oil falls to the bottom of the distillation column and is removed by a heavy duty lube oil pump. This pump forces the dry oil through a final particulate removal filter. Clean oil passes out of the unit, back to the reservoir, and then back into the system.
Why PVS (Vacuum Dehydration) Techonology Out-performs Other Technologies?
• Centrifuge units – Removes free water only; has difficulty breaking stable emulsions; larger envelope dimensions but lower flows; higher initial and operating costs.
• Desiccant units – Have limited water removal capability due to absorbing material; only removes air ingressed particles; expensive compared to the volume of water removed.
• Coalescer units – Removes free water only; has difficulty breaking stable emulsions; does not work well in viscous fluids (>100 sus); much larger in size compared to PVS.
Designed for Use in The Following Markets:
• Power Generation
• Pulp and Paper
• Primary Metals
• Mining
• Plastic Injection Molding
• Oil Exploration
• Petrochemical
• Automotive
• Aerospace
• Refineries
• Transportation
Applications:
• Hydraulic Systems
• Lubrication Systems
• Turbine Oil
• Transformer Oil
• New Oil (oil storage)
• Seal Oil
• Explosion Proof Environments
Standard Unit Includes:
• Variable Flow Circuit
• Moisture Sensor
• Automatic Operation
• 316 Stainless Steel (Used for Primary Wetted Surfaces)
• 2-20 micron Ecoglass III Particulate Element
• Condensate Holding Tank with Optional Auto Drain
• Clear Plexiglas Covers on the Condensate Holding Tank and Vacuum Chamber
• Desiccant Breather
• Reverse Phase Switch
• Programmable Thermostat
• Forklift Guides and Lifting Eyes
• Coalescing or Packed Tower Oil Dispersing Elements
Features and Benefits:
• Allows Oil to Heat Quickly, Removing Water More Quickly, Saving Time
• Real-time Water Content Indication in % Saturation, Providing At-a-Glance Visual Confirmation
• Unattended Use, Reducing Labor Costs
• Designed for 24/7 Operation, Increasing System Operation Time
• No Corrosion, Increasing Product Reliability
• Able to View the Vacuum Dehydration Process, Providing Visual Verification of Water Removal
• Desiccant Breather Insures Dry, Clean Intake Air, Providing More Efficient Operation
• Easy-to-Change Motor Rotation, Providing Ease of Maintenance and Preventing Incorrect Rotation
• Provides Safe and Secure Method of Lifting the Unit, Ensuring Employee Safety
• Flexibility with Various Fluid Viscosities, Providing Greater Efficiency in Removing Moisture
• Phase reversal switch allows easy-to-change power phase, Providing Ease of Maintenance and Preventing Incorrect Rotation -
Auxiliary Filtration System
The AFS is the ideal way to prefilter and transfer fluids, on the ground or in the air.
Fluid should always be filtered prior to use. New fluid is not necessarily clean fluid. Most new fluids (directly from the container) are unfit for use, due to high initial contamination levels. Contamination, both particulate and water, may be introduced to a new fluid during processing, mixing, handling and storage.
The AFS uses a high capacity ModuFlow™ Plus filter for long element life and optimum filtration. The single element package provides a high level of filtration performance in a compact size. Free water is controlled by utilizing Parker’s Par-Gel™ element. Par-Gel™ elements have a very high affinity for free water.
Designed with functionality, space and durability in mind the AFS comes standard with a rated lifting eye. The optimized design and rugged steel construction allow service personnel access to the critical hydraulic systems through passageways as small as 12” x 16”.
The use of a Parker portable filtration system is the most efficient and economical way to extend fluid life and protect critical system components from harmful contaminants.
Applications
• Pre-clean hydraulic fluids prior to system fill
• Transferring fluid from drums or storage tanks to system reservoirs
• Conditioning fluid in use
• Complimenting existing system filtration
• Removing free and emulsified water from a system
Features
• Visual indicator
Tells you when to change element
• Single filter
Double length filtration for long element life
• Drip tray
Helps keep the work area safe and clean
• Smaller footprint
Fits into 12”x16” wind turbine hatch
• Heavy duty steel frame
Rugged and built to last
• 110V/220V AC motor
Industrial brand name
• Particle detection
Detects changes in contamination levels and alerts when oil is clean
• Element access cover
Top-accessible for easy changing of elements
• Hose
8 foot, kink-resistant hose prevents pump cavitation
• Lifting eye
Rated hoist ring not to exceed 250 lbs.
• Optional Concentric wand
Ready to use; no additional hardware needed