Locomotive Crankcase Ventilation
Contaminated crankcase emissions are a serious problem for engine owners and the environment! The EPA strictly regulates these types of harmful emissions.
The crankcase of an internal combustion engine houses all the components that come in contact with engine lubrication oil. It is extremely important to have a crankcase ventilation system in place for gases to escape in a controlled manner.
When some of the gases from the combustion leak past the piston rings, and end up inside the crankcase, causing pressure, they are commonly referred to as “blow-by” gases. These Crankcase emissions (“blow-by”) are the gases and hydrocarbons that are pushed out of the crankcase during engine operation. A Crankcase Ventilation (CCV) system is necessary because this is the location where blow-by aerosols and particles are created.
As these blow-by gases pass though the crankcase, they become contaminated with oil mist. In enclosed areas like generator sets or engine rooms, contaminated blow-by gas coats and damages the surrounding equipment, resulting in hazardous conditions, equipment fouling, and expensive clean up maintenance. Uncontrolled blow-by oil mist also coats engine after coolers and turbochargers, reducing cooling capacity, reducing the ability to transfer heat, causing power loss, reduced fuel economy and engine efficiency. Parker CCV systems remove the mist and contamination before it can do damage, offering an effective solution.
How The Parker CCV Works:
The Parker CCV filter can be properly adapted to most engines, air compressors and other industrial equipment which requires clean intake air. The uniqueness of CCV filtration versus industrial coalescing applications is the intolerance for internal pressures. These high velocity filters from Parker are designed to withstand severe operating conditions and are engineered to assure peak filtration performance.
Media saturated with oil is very different than media plugged with dust or dirt. Here is where the CCV filter departs from any similarity with air filters. Although the fluid that flows through a CCV media is gaseous and mostly air, the CCV filter is primarily a coalescing filter, not a particle trap like an air filter.
The process of growing small particles into droplets and shedding them is the act of coalescing. CCV filters must coalesce aerosols to collect an amount of liquid downstream. When oil is in aerosol form, it is still a liquid. As aerosol particles join together in the media, they pool together. The pools are formed into droplets, and the droplets eventually are pushed to the downstream side of the media. As the droplets grow, they are shed out of the media and trickle off of the outer surface.
Once the oil has collected in the media, it must be released. Blow-by gasses are not allowed to vent into the atmosphere. Instead, the cleaned and filtered gases are routed back to the inlet of the turbocharger to be burned in the engine, to prevent polluting the environment.
The Parker coalescer elements use metallic filter media based solutions for durability. Crankcase ventilation elements should be inspected and replaced according to locomotive manufacturers' guidelines. Typical Tier 3 crankcase ventilation solutions include a pressurized air assist for evacuating the vent gas.
Features/Benefits
• Keeps engine compartments and components clean
• Prevents clogging of engine intakes, turbochargers, and intercoolers
• Improves reliability and maintainability of engines
• Reduces environmental pollution from crankcase emissions
Applications
• Locomotive
• Marine
• Stationary
The crankcase of an internal combustion engine houses all the components that come in contact with engine lubrication oil. It is extremely important to have a crankcase ventilation system in place for gases to escape in a controlled manner.
When some of the gases from the combustion leak past the piston rings, and end up inside the crankcase, causing pressure, they are commonly referred to as “blow-by” gases. These Crankcase emissions (“blow-by”) are the gases and hydrocarbons that are pushed out of the crankcase during engine operation. A Crankcase Ventilation (CCV) system is necessary because this is the location where blow-by aerosols and particles are created.
As these blow-by gases pass though the crankcase, they become contaminated with oil mist. In enclosed areas like generator sets or engine rooms, contaminated blow-by gas coats and damages the surrounding equipment, resulting in hazardous conditions, equipment fouling, and expensive clean up maintenance. Uncontrolled blow-by oil mist also coats engine after coolers and turbochargers, reducing cooling capacity, reducing the ability to transfer heat, causing power loss, reduced fuel economy and engine efficiency. Parker CCV systems remove the mist and contamination before it can do damage, offering an effective solution.
How The Parker CCV Works:
The Parker CCV filter can be properly adapted to most engines, air compressors and other industrial equipment which requires clean intake air. The uniqueness of CCV filtration versus industrial coalescing applications is the intolerance for internal pressures. These high velocity filters from Parker are designed to withstand severe operating conditions and are engineered to assure peak filtration performance.
Media saturated with oil is very different than media plugged with dust or dirt. Here is where the CCV filter departs from any similarity with air filters. Although the fluid that flows through a CCV media is gaseous and mostly air, the CCV filter is primarily a coalescing filter, not a particle trap like an air filter.
The process of growing small particles into droplets and shedding them is the act of coalescing. CCV filters must coalesce aerosols to collect an amount of liquid downstream. When oil is in aerosol form, it is still a liquid. As aerosol particles join together in the media, they pool together. The pools are formed into droplets, and the droplets eventually are pushed to the downstream side of the media. As the droplets grow, they are shed out of the media and trickle off of the outer surface.
Once the oil has collected in the media, it must be released. Blow-by gasses are not allowed to vent into the atmosphere. Instead, the cleaned and filtered gases are routed back to the inlet of the turbocharger to be burned in the engine, to prevent polluting the environment.
The Parker coalescer elements use metallic filter media based solutions for durability. Crankcase ventilation elements should be inspected and replaced according to locomotive manufacturers' guidelines. Typical Tier 3 crankcase ventilation solutions include a pressurized air assist for evacuating the vent gas.
Features/Benefits
• Keeps engine compartments and components clean
• Prevents clogging of engine intakes, turbochargers, and intercoolers
• Improves reliability and maintainability of engines
• Reduces environmental pollution from crankcase emissions
Applications
• Locomotive
• Marine
• Stationary
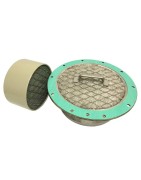