Kołnierze
Celem firmy Parker jest zapewnienie idealnego dopasowania do wszystkich węży i rurek, dlatego oferujemy kołnierze pasujące do każdej konfiguracji i każdego podłoża. Kołnierze firmy Parker spełniają lub przewyższają wszystkie normy i specyfi
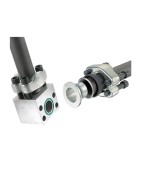
-
Flange / Flare Adapters
Parker's Flange and Flare Adapters assist with making challenging routing situations easier by providing different connection types for hydraulic systems. We offer flanges that accommodate numerous end configurations. Our Flanges and Flare Adapters meet and/or exceed all industry standards and specifications, and only Parker can provide the most efficient and appropriate flange for every hose product.
Markets:
• Transportation
• RV & Bus
• Military
• Construction
• Agriculture
• Grounds & Building Maintenance
• Forestry
• Railroad
• Utility Equipment
• Personal Lift Equipment
• Machine Tool
• Oil Field Service
• Waste & Refuse
• Material Handling
• Marine
• Paving & Road Maintenance
• Ground Support Equipment
• Industrial
• Mining
• Automotive
Features/Benefits:
• Numerous end configurations available
• Unique connection types to make tough routing situations easier
• Meets and/or exceeds industry standards
Applications:
• Petroleum base hydraulic fluids and lubricating oils -
Flange Halves
Parker's Flange Halves are a four bolt, split flange system with numerous end configurations available to meet your specific needs. The majority of our flanges are manufactured from forged steel with a limited amount machined from bar stock. The forged construction provides higher strength and durability to provide long lasting performance in the application. Parker flanges and flange kits are designed to meet or exceed SAE J518 and ISO 6162.
Markets:
• Transportation
• RV & Bus
• Military
• Construction
• Agriculture
• Grounds & Building Maintenance
• Forestry
• Railroad
• Utility Equipment
• Personal Lift Equipment
• Machine Tool
• Oil Field Service
• Waste & Refuse
• Material Handling
• Marine
• Paving & Road Maintenance
• Ground Support Equipment
• Industrial
• Mining
• Automotive
Features/Benefits:
• Forged steel construction for durability and longer life
• Numerous end configurations available
Applications:
• Petroleum base hydraulic fluids and lubricating oils -
Flange Kits
Parker's Flange Kits contain four bolts, a split flange and an O-ring developed to provide long-lasting performance and durability. The Flange Kits come in numerous end configurations to meet your specific needs. The majority of our flanges are manufactured from forged steel with a limited amount machined from bar stock. The forged construction provides higher strength and durability to the flange.
Markets:
• Transportation
• RV & Bus
• Military
• Construction
• Agriculture
• Grounds & Building Maintenance
• Forestry
• Railroad
• Utility Equipment
• Personal Lift Equipment
• Machine Tool
• Oil Field Service
• Waste & Refuse
• Material Handling
• Marine
• Paving & Road Maintenance
• Ground Support Equipment
• Industrial
• Mining
• Automotive
Features/Benefits:
• Contains four bolts, a split flange, and an O-ring to make a complete flange assembly
• Flange Kits can be installed after fitting has been crimped
Applications:
• Petroleum base hydraulic fluids and lubricating oils -
Full Flange System
Parker's one-piece Full Flange option, for Code 61 and Code 62 connections, enables the flange to be attached to the hose after the fitting has been crimped onto the hose, making installation easier and faster. Installation of the Full Flange to the port is easy - no more fumbling with flange halves, and the flange can be rotated for ease of assembly to the port. The Full Flange system can be used repeatedly thanks to its attachment design - the flange is not permanently locked onto the fitting.
Markets:
• Transportation
• RV & Bus
• Military
• Construction
• Agriculture
• Grounds & Building Maintenance
• Forestry
• Railroad
• Utility Equipment
• Personal Lift Equipment
• Machine Tool
• Oil Field Service
• Waste & Refuse
• Material Handling
• Marine
• Paving & Road Maintenance
• Ground Support Equipment
• Industrial
• Mining
• Automotive
Features/Benefits:
• One piece flange for quick installation
• Full Flange system can be installed after fitting has been crimped
Applications:
• Petroleum base hydraulic fluids and lubricating oils -
4-Bolt Hydraulic Flanges and Components
Parker's hydraulic flanges and components conform to SAE J518 and ISO 6162-1 and -2. These proven leak-free connections are suited for tube and pipe in larger sizes, and have achieved world-wide acceptance.
Markets:
• Construction
• Agriculture
• Oil & Gas
• Transportation
• Mining
• Forestry
Features/Benefits:
• Adapts BSPP, SAE Straight thread and NPTF, as well as tube and pipe weld connections.
• Lower tightening torque required compared to that required for equivalent size threaded port, therefore smaller wrenches and wrench swing clearances needed--providing ease of assembly in tight quarters.
• Ease of disassembly with use of split clamps.
• Over 60 configurations available, with custom designs available on request.
• Available in steel and stainless steel in flange sizes ½” through 3” with working pressures up to 6000 psi.
Applications:
• Hydraulic fluid and gas handling connections -
HPF - High Performance Flange System Flange Connection...
HPF is generally applicable for working pressures up to 420 bar. But the design opens the door to go even beyond this pressure rating: by choosing a suitable combination of flange, insert and tube the pressure rating can be increased to 500 bar.
The System is adjusted to standard tube dimensions with diameters from 25 to 150 mm and wall thickness up to 20 mm. It is designed for flange patterns according to ISO 6162-1 (SAE J518, code 61), ISO 6162-2 (SAE J518, code 62) and ISO 6164.
Markets:
• Environment
• Industrial
• Machine Tools
• Materials Handling
• Mobile
• Oil and Gas
• Power Generation
• Process
Applications:
• Suitable for general hydraulic and industrial applications.
Features/ Benefits of Parker High Performance Flanges:
• The Parker High Performance Flange System stands for total cost reductions! Compared to conventional welding, the High Performance Flange System leads to several time and cost benefits: The pipework fabrication is very fast and the installation time shorter compared to welding. X-ray is not necessary and there are no post-welding cleaning costs. The flushing costs are reduced as well.
• The Parker High Performance Flange System is worldwide available through the Parker distribution network.
• In addition to the product range, Parker offers value added service, because Parker is able to engineer your hydraulic application.
Learning from nature
The best solutions for complex design problems can often be
found in nature. The flaring of the HPF tube is similar to the shape of a branch where it joints the trunk of a tree: The tube is flared by hydraulic axial pressure giving it a parabolic shaping, increasing from 10° up to 37°. The initial gentle incline of the shaping guarantees additional safety against strong system vibrations. The DGUV confirms the capability of this unique, patented system especially for the use in hydraulic and mechanical presses as well as in hydraulic power systems for injection moulding machines. Beside that, the system is an ideal solution for marine and offshore applications. It is type approved by various classification societies like DNV/GL, BV and LR.
The HPF Connector - Strong teamwork for the toughest demands
HPF flanges are equipped with a specially designed and hardened inner grip contour, providing excellent additional tear-off safety for the connection. Optionally some sizes are equipped with special lockrings. A shaped insert is placed into the flared end of the tube. On the port side the sealing is guaranteed by a F37 Seal - which is a special profile seal - or an O-ring seal, on the tube side by an O-ring seal.
The F37 Seal was developed especially for the use with SAE
flanges. These special seals guarantee a high form stability.
Compared to standard O-Rings, their mechanical properties
prevent gap extrusion, even when the flanges “breathe” under
pressure. The special profile of the F37 Seal is ideally adapted to higer pressures or unsuitable surface finish of the flanges.
The application of these soft-sealing elements both on the port
side and tube side guarantees the gas leak tightness of the HPF
connector. As the insert does not have a toothed profile, it can
be easily assembled repeatedly.
Tube forming
The tube forming is performed by the Parflange® HPF machines; they can either be purchased or rented for a certain period of time. If required, assembly of ready-to-install straight or manipulated HPF tube lines can be carried out by a Parker CPS Piping Center.
Flanging instead of welding: Error-free and riskless assembly
Nowadays many tube connections are welded. However, as even the best welding operator may make a mistake, each welding seam has to be tested, leading to an enormous loss of time and a significant increase of costs. Even finding trained staffed may be critical. Apart from enormous time savings for the joint preparation itself, HPF offers various advantages compared to the welding solution:
• Welding galvanic zinc-plated tubes is always critical. With
HPF zinc-plated tubes can be used, there is no further painting
necessary.
• Welding seams must be descaled and often be stained. Dealing with this process and substances is an environmental
risk.
• Welded tubes need to be intensively cleaned inside. HPF tube
assemblies do not require any special cleaning, reducing flushing time and costs during initial system startup.
• The flanging process does not cause noxious gases, thus eliminating explosion risks and fire hazards.
• The HPF tube forming is a machined cold forming process.
Therefore there is no need for X-raying the connection.
Cr(VI)-free corrosion protection
All components do of course have surfaces which are free of
Cr(VI) platings. Parker is highly aware of its responsibility for
the environment and human health. Therefore Parker has completely renounced the use of Cr(VI) containing surfaces.
Personnel and environment-friendly
By comparing the individual operations for a welded line with
Parker flanges connected lines, significant cost savings opportunities become immediately obvious. No vapours putting health at risk are released, in contrast to conventional welding processes. Consequently, usage is possible in locations with high requirements such as, for example, offshore oil platforms.
In addition to this, flaring machine design errors in the preparation of flanges are virtually unknown. Stress corrosion cracking generated during welding operations is history and the life of the finished tubing system is increased. Cold formed Parflange® technologies save power and energy compared to welding and require neither degreasers nor anti-corrosion agents. When galvanized tubes are used, post-galvanization can be omitted because the zinc-coating is not impaired by flaring. Parker flange connector components are delivered in state of the art Cr(VI)-free surfaces. -
ISO 6162-1/2 SAE Full Flanges for Threaded and Cutting Ring...
4 bolt flange connection ISO 6162-1/2 (SAE J518 Code 61/62) and ISO 6164 is a proven leak-free connection, especially suited for larger sizes. As a result, it has achieved worldwide acceptance. The connection’s success is in its simplicity. The static O-ring seal is compressed between the bottom of the groove in the flange head and the flat surface of the port or flange pad, providing a reliable soft seal. High grade bolts ensure the holding power for dynamic applications up to 420 bar.
Markets:
• Environment
• Industrial
• Machine Tools
• Marine
• Materials Handling
• Mobile Industries
• Power Generation
• Press Building
Applications:
• Suitable for general hydraulic and industrial applications.
This simple design provides several advantages over threaded port connections, such as NPT, SAE, BSPP, ISO 6149 etc., in larger sizes:
• Ability to connect tube fittings connection systems to SAE port systems
• Much lower tightening torque required from the four bolts compared to equivalent fitting assembly torques
• Less tightening torque means smaller wrenches and wrench swing clearances – providing ease of assembly in
tight working environment.
• Single seal point between tube/pipe/hose assembly and the port -
ISO 6162-1/2 SAE Butt and Socket Weld Adapters
4 bolt flange connection ISO 6162-1/2 (SAE J518 Code 61/62) and ISO 6164 is a proven leak-free connection, especially suited for larger sizes. As a result, it has achieved worldwide acceptance. The connection’s success is in its simplicity. It is a static face seal using a high durometer O-ring for the seal and clamps and bolts for holding power. The O-ring seal is compressed between the bottom of the groove in the flange head and the flat surface of the port or flange pad, providing a reliable soft seal.
Markets:
• Environment
• Industrial
• Machine Tools
• Marine
• Materials Handling
• Mobile Industries
• Power Generation
• Press Building
Applications:
• Suitable for general hydraulic and industrial applications.
This simple design provides several advantages over threaded port connections, such as NPT, SAE, BSPP, ISO 6149 etc., in larger sizes:
• Ability to connect tube fittings connection systems to SAE port systems
• Much lower tightening torque required from the four bolts compared to equivalent fitting assembly torques
• Less tightening torque means smaller wrenches and wrench swing clearances – providing ease of assembly in
tight working environment.
• Single seal point between tube/pipe/hose assembly and the port
• Ease of disassembly through use of split clamps possible -
SAE Flange Clamps according to ISO 6162-1/2
Flange clamps are used for providing the holding power to the 4 bolt flange connection. They are offered in split and captive (one-piece) versions. The captive ones are also offered with either drilled or tapped bolt holes. The captive flange clamp with tapped holes is used while connecting a tube to another tube or a hose.
The split clamps make it easy to assemble the connection in close quarters. They also enable an easy removal of the flange head component, such as a hose assembly, by loosening all four bolts and removing one clamp half.
Markets:
• Environment
• Industrial
• Machine Tools
• Marine
• Materials Handling
• Mobile Industries
• Power Generation
• Press Building
Applications:
• Suitable for general hydraulic and industrial applications.
4 bolt flange connection ISO 6162-1/2 (SAE J518 Code 61/62) and ISO 6164 is a proven leak-free connection, especially suited for larger sizes. As a result, it has achieved worldwide acceptance. The connection’s success is in its simplicity. It is a static face seal using a high durometer O-ring for the seal and clamps and bolts for holding power. The O-ring seal is compressed between the bottom of the groove in the flange head and the flat surface of the port or flange pad, providing a reliable soft seal.
This simple design provides several advantages over threaded port connections, such as NPT, SAE, BSPP, ISO 6149 etc., in larger sizes:
• Ability to connect up to 5 inch O.D. tube (ISO 6162-1 only)
• Much lower tightening torque required from the four bolts compared to equivalent threaded size port.
• Less tightening torque means smaller wrenches and wrench swing clearances – providing ease of assembly in
tight working environment.
• Up to 6000 psi capability through 3“ size (ISO 6162-2 only)
• Use up to 420 bar at the ISO 6164 flange sizes from 3/8" to 4".
• Single seal point between tube/pipe/hose assembly and the port
• Ease of disassembly through use of split clamps -
ISO 6162-1/2 SAE Flange to Tube Fittings Adapters
4 bolt flange connection ISO 6162-1/2 (SAE J518 Code 61/62) and ISO 6164 is a proven leak-free connection, especially suited for larger sizes. As a result, it has achieved worldwide acceptance. The connection’s success is in its simplicity. It is a static face seal using a high durometer O-ring for the seal and clamps and bolts for holding power. The O-ring seal is compressed between the bottom of the groove in the flange head and the flat surface of the port or flange pad, providing a reliable soft seal.
Markets:
• Environment
• Industrial
• Machine Tools
• Marine
• Materials Handling
• Mobile Industries
• Power Generation
• Press Building
Applications:
• Suitable for general hydraulic and industrial applications.
This simple design provides several advantages over threaded port connections, such as NPT, SAE, BSPP, ISO 6149 etc., in larger sizes:
• Ability to connect tube fittings connection systems to SAE port systems
• Much lower tightening torque required from the four bolts compared to equivalent fitting assembly torques
• Less tightening torque means smaller wrenches and wrench swing clearances – providing ease of assembly in
tight working environment.
• Single seal point between tube/pipe/hose assembly and the port
• Ease of disassembly through use of split clamps possible -
ISO 6162-1/2 SAE Full Flanges for Butt and Socket Weld...
4 bolt flange connection ISO 6162-1/2 (SAE J518 Code 61/62) and ISO 6164 is a proven leak-free connection, especially suited for larger sizes. As a result, it has achieved worldwide acceptance. The connection’s success is in its simplicity. The static O-ring seal is compressed between the bottom of the groove in the flange head and the flat surface of the port or flange pad, providing a reliable soft seal. High grade bolts ensure the holding power for dynamic applications up to 420 bar.
Markets:
• Environment
• Industrial
• Machine Tools
• Marine
• Materials Handling
• Mobile Industries
• Power Generation
• Press Building
Applications:
• Suitable for general hydraulic and industrial applications.
This simple design provides several advantages over threaded port connections, such as NPT, SAE, BSPP, ISO 6149 etc., in larger sizes:
• Ability to connect tube fittings connection systems to SAE port systems
• Much lower tightening torque required from the four bolts compared to equivalent fitting assembly torques
• Less tightening torque means smaller wrenches and wrench swing clearances – providing ease of assembly in
tight working environment.
• Single seal point between tube/pipe/hose assembly and the port -
Parflange 170 flaring machines and tooling
The machine is available in 2 versions:
• Parflange® 170 ECO for use on work bench and
• WorkCenter Parflange® 170 WCM which is mounted on a movable tool cabinet.
Two hydraulic cylinders operated by a hand pump generate the axial feed movement. Gas springs move the flaring unit back after the valve on the hand pump is opened. The tubes are mechanically clamped between a set of dies. The machine features an adjustable tube stop for tube positioning (Tube Stop), and an adjustable stop for the tube depth to be flared (Spindle Stop). Parflange® machines are delivered ready for use. Tools have to be ordered separately. Clamping die sets and flanging pins are available for common tube sizes. The machine can be moved by crane or forklift.
Applications:
• Workshop use
• Project work
• Plant maintenance
• On-site assembly
Industries:
The F37 system is an alternative to conventional welding of flanges in
• Shipbuilding
• Oil & Gas exploration
• Similar Industries
Features/ Benefits:
• Cost saving – Compared to welding or brazing, orbital flaring is much less time consuming. Special tube preparation and finishing are not necessary. Flaring uses only a fraction of the energy needed for brazing or welding.
• Zinc plated tubing – The Parflange® process allows the use of zinc plated tubing. The cost for cleaning, post process plating or painting is saved.
• Superior sealing performance – The orbital flaring process achieves a sealing surface of superior surface quality and mechanical strength.
• Process/Product concept – Parflange® machines are especially designed to match Parker F37 flange standards. Machines, tools and products are fine-tuned for reliable performance.
• Workshop use – The rigid machine design allows project work in on site piping workshops.
• Short clamping length – Clamping dies for 37° flaring are optimized for minimum straight tube length.
• Easy to use – All operational devices are obvious so that machine operation is intuitive.
• Quality – Consistent quality results are achieved by recommended values for machine setting.
• Constant flare diameter – The diameter of the 37° flare is given by the tool contour and the Tube Stop adjustment. A chart on the machine indicates recommended Tube Stop setting.
• Prevention of over-flaring – The shape of the 37° flare is given by the tool contour and the Spindle Stop adjustment. This prevents difficulties to fit the insert into the flare.
• Flexible – Different tube material and quality might require special setting of Tube Stop, Spindle Stop, flanging feed and flanging force. For best results, these parameters can be manually adjusted based on operators experience.
• Clean – The Parflange® process is environmentally clean and safe. As no heat or chemicals are used, hazards from fumes or heat do not occur.
• Perfect for on site work – The machine has special attachments for transportation by fork lift and crane. The wide base provides a safe stand. This is particularly useful for on site pipe installation in shipyards or in oil and gas exploration. -
ISO 6162-1/2 SAE Flange Accessory Components
4 bolt flange connection ISO 6162-1/2 (SAE J518 Code 61/62) and ISO 6164 is a proven leak-free connection, especially suited for larger sizes. As a result, it has achieved worldwide acceptance. The connection’s success is in its simplicity. The static O-ring seal is compressed between the bottom of the groove in the flange head and the flat surface of the port or flange pad, providing a reliable soft seal. High grade bolts ensure the holding power for dynamic applications up to 420 bar.
Markets:
• Environment
• Industrial
• Machine Tools
• Marine
• Materials Handling
• Mobile Industries
• Power Generation
• Press Building
Applications:
• Suitable for general hydraulic and industrial applications.
This simple design provides several advantages over threaded port connections, such as NPT, SAE, BSPP, ISO 6149 etc., in larger sizes:
• Ability to connect tube fittings connection systems to SAE port systems
• Much lower tightening torque required from the four bolts compared to equivalent fitting assembly torques
• Less tightening torque means smaller wrenches and wrench swing clearances – providing ease of assembly in
tight working environment.
• Single seal point between tube/pipe/hose assembly and the port -
ISO 6164 Flange Connections
4 bolt flange connection with ISO 6164 is a proven leak-free connection, especially suited for larger sizes ans high pressures. As a result, it has achieved worldwide acceptance. The connection’s success is in its simplicity. It is a static face seal using a high durometer O-ring for the seal and clamps and bolts for holding power. The O-ring seal is compressed between the bottom of the groove in the flange head and the flat surface of the port or flange pad, providing a reliable soft seal.
Markets:
• Environment
• Industrial
• Machine Tools
• Marine
• Materials Handling
• Mobile Industries
• Power Generation
• Press Building
Applications:
• Suitable for general hydraulic and industrial applications.
This simple design provides several advantages over threaded port connections, such as NPT, SAE, BSPP, ISO 6149 etc., in larger sizes:
• Single seal point between tube assembly and the port -
Parflange F37 Non-Weld Flare Flange Connection
The Parflange F37 flanged connector system is utilising the orbital tube forming technology for tubing assemblies from 16 to 273 mm (1/2" to 10" Flanges) outside diameter. It is intended for tube wall thickness up to 9 mm and pressure ratings up to 420 bar. For those connections without the possibility to assemble a pre-flared tube or where manufacturing is limited, Parker provides the F37 Retaining Ring System. This System utilizes a Retaining Ring for flange retention along with a highly-engineered seal carrier for leak free performance. It is available as a high pressure version from 1 1/2" to 10" and as a newly developed SAE 1000 (50-70 bar) version. The Parflange F37 system corresponds to hole patterns according to ISO 6162-1; SAE J518; bore pattern 3000 (code 61), ISO 6162-2; bore pattern 6000 (code 62) and also ISO 6164 bore pattern. It is type approved by DNV, ABS and other major classification companies.
Markets:
• Marine
• Offshore
• Industrial Heavy Machinery
• Machine Tools
• Materials Handling
• Mobile Industries
• Power Generation
• Press Building
• Environment
Innovative Sealing Solutions
The F37 seal was developed especially for use with SAE flanges. These special seals guarantee high stability of form. Compared to standard O-Rings, their mechanical properties prevent gap extrusion, even when the flanges ”breathe” under pressure. The special profile of the F37 seal is ideally adapted to higher pressures or unsuitable surface finish of the flanges. As an alternative, connectors can be equipped with bonded seal rings.
Complete range for virtually all diameters
The F37 system complements the EO-2 soft sealing technology for small tube diameters; it also complements the proven Parflange programme for the SAE product range. It offers the complete range of connectors, flange-to-flange, L-and T-Block connectors, flange-to-port, male and female thread flanges, flange bends, reducer flanges, ball valves, bulkhead flanges and manifolds on request.
The F37-Programme – a savings programme
F37 is the way to reduce manufacturing times enormously. By comparing welded connections with Parker flange connector systems, significant opportunities for cost savings become immediately obvious. The typical process of tube welding consist of the following steps:
1. Cutting and deburring tubes
2. Tube preparation for the connecting process
3. Welding and/or assembling
4. Inspection (X-ray) of welded connectors
5. Flushing the connected tubes
6. Applying corrosion protection
In comparison with this, weld-free tube forming save time and costs. Expensive cleaning and X-raying of the tube connector become immediately things of the past. The manufacturing time for a tube connector quickly reduces by more than half in comparison with conventional welding. Parker flange connector systems accommodate high requirements, especially those from the offshore industry, shipbuilding, heavy machinery construction and press manufacture, as well as from mining, recycling plants and mobile machinery; overall in power piping systems.
Personnel and environment-friendly
By comparing the individual operations for a welded line with Parker flanges connected lines, significant cost savings opportunities become immediately obvious. No vapours putting health at risk are released, in contrast to conventional welding processes. Consequently, usage is possible in locations with high requirements such as, for example, offshore oil platforms. In addition to this flaring machine design errors in the preparation of flanges are virtually unknown. Stress corrosion cracking generated during welding operations is history and the life of the finished tubing system is increased. Cold formed Parflange technologies save power and energy compared to welding and require neither degreasers nor anti-corrosion agents. When galvanized tubes are used, post-galvanization can be omitted because the zinc-coating is not impaired by flaring. Parker flange connector components are delivered in state of the art Cr(VI)-free surfaces.
Features, advantages and benefits
No welding
- Reduced preparation time per joint
- No costly inspection of welds (X-ray)
No post-weld cleaning
- No acid cleaning costs
- No waste cleaning costs
- No safety risk
- Environmentally friendly
No welding stress corrosion possible
- Maximum piping lifetime
- Reduced maintenance costs
No „hot work“ permit required
- Operation can take place in areas with fire risk without interruption of production
- Reduced downtime costs
- Higher level of safety
Work shop prefabrication
- High quality joints with better accuracy due to workshop conditions
- Minimized need for on-site work
- Shorter installation time
- Shorter maintenance/downtime
- Shorter total project time
Cleanliness
- Minimized need for repair and replacement of hydraulic system components such as pumps, cylinders,…
- Reduced overall flushing time and costs
Easy dismantling and reassembling
- Quicker, easier and more flexible installation
- Reduced downtime costs for maintenance and repair -
Gear Pump Flanges
Parker is offering a wide range of gear pump flanges for all typical tube connection methods: if it is cutting ring acc. ISO8434-1 / or O-Ring Face Seal (ISO 8434-3) or 60° Cone Connection (ISO 8434-6). Even Flanges for weld connections are available.
Gear Pump Flanges are available in steel material with Cr(VI)-free surface protection.
Markets:
• Environment
• Industrial
• Machine Tools
• Marine
• Materials Handling
• Mobile Industries
• Power Generation
• Press Building
Applications:
• Suitable for general hydraulic and industrial applications.