Parflange 170 flaring machines and tooling
The machine is available in 2 versions:
• Parflange® 170 ECO for use on work bench and
• WorkCenter Parflange® 170 WCM which is mounted on a movable tool cabinet.
Two hydraulic cylinders operated by a hand pump generate the axial feed movement. Gas springs move the flaring unit back after the valve on the hand pump is opened. The tubes are mechanically clamped between a set of dies. The machine features an adjustable tube stop for tube positioning (Tube Stop), and an adjustable stop for the tube depth to be flared (Spindle Stop). Parflange® machines are delivered ready for use. Tools have to be ordered separately. Clamping die sets and flanging pins are available for common tube sizes. The machine can be moved by crane or forklift.
Applications:
• Workshop use
• Project work
• Plant maintenance
• On-site assembly
Industries:
The F37 system is an alternative to conventional welding of flanges in
• Shipbuilding
• Oil & Gas exploration
• Similar Industries
Features/ Benefits:
• Cost saving – Compared to welding or brazing, orbital flaring is much less time consuming. Special tube preparation and finishing are not necessary. Flaring uses only a fraction of the energy needed for brazing or welding.
• Zinc plated tubing – The Parflange® process allows the use of zinc plated tubing. The cost for cleaning, post process plating or painting is saved.
• Superior sealing performance – The orbital flaring process achieves a sealing surface of superior surface quality and mechanical strength.
• Process/Product concept – Parflange® machines are especially designed to match Parker F37 flange standards. Machines, tools and products are fine-tuned for reliable performance.
• Workshop use – The rigid machine design allows project work in on site piping workshops.
• Short clamping length – Clamping dies for 37° flaring are optimized for minimum straight tube length.
• Easy to use – All operational devices are obvious so that machine operation is intuitive.
• Quality – Consistent quality results are achieved by recommended values for machine setting.
• Constant flare diameter – The diameter of the 37° flare is given by the tool contour and the Tube Stop adjustment. A chart on the machine indicates recommended Tube Stop setting.
• Prevention of over-flaring – The shape of the 37° flare is given by the tool contour and the Spindle Stop adjustment. This prevents difficulties to fit the insert into the flare.
• Flexible – Different tube material and quality might require special setting of Tube Stop, Spindle Stop, flanging feed and flanging force. For best results, these parameters can be manually adjusted based on operators experience.
• Clean – The Parflange® process is environmentally clean and safe. As no heat or chemicals are used, hazards from fumes or heat do not occur.
• Perfect for on site work – The machine has special attachments for transportation by fork lift and crane. The wide base provides a safe stand. This is particularly useful for on site pipe installation in shipyards or in oil and gas exploration.
• Parflange® 170 ECO for use on work bench and
• WorkCenter Parflange® 170 WCM which is mounted on a movable tool cabinet.
Two hydraulic cylinders operated by a hand pump generate the axial feed movement. Gas springs move the flaring unit back after the valve on the hand pump is opened. The tubes are mechanically clamped between a set of dies. The machine features an adjustable tube stop for tube positioning (Tube Stop), and an adjustable stop for the tube depth to be flared (Spindle Stop). Parflange® machines are delivered ready for use. Tools have to be ordered separately. Clamping die sets and flanging pins are available for common tube sizes. The machine can be moved by crane or forklift.
Applications:
• Workshop use
• Project work
• Plant maintenance
• On-site assembly
Industries:
The F37 system is an alternative to conventional welding of flanges in
• Shipbuilding
• Oil & Gas exploration
• Similar Industries
Features/ Benefits:
• Cost saving – Compared to welding or brazing, orbital flaring is much less time consuming. Special tube preparation and finishing are not necessary. Flaring uses only a fraction of the energy needed for brazing or welding.
• Zinc plated tubing – The Parflange® process allows the use of zinc plated tubing. The cost for cleaning, post process plating or painting is saved.
• Superior sealing performance – The orbital flaring process achieves a sealing surface of superior surface quality and mechanical strength.
• Process/Product concept – Parflange® machines are especially designed to match Parker F37 flange standards. Machines, tools and products are fine-tuned for reliable performance.
• Workshop use – The rigid machine design allows project work in on site piping workshops.
• Short clamping length – Clamping dies for 37° flaring are optimized for minimum straight tube length.
• Easy to use – All operational devices are obvious so that machine operation is intuitive.
• Quality – Consistent quality results are achieved by recommended values for machine setting.
• Constant flare diameter – The diameter of the 37° flare is given by the tool contour and the Tube Stop adjustment. A chart on the machine indicates recommended Tube Stop setting.
• Prevention of over-flaring – The shape of the 37° flare is given by the tool contour and the Spindle Stop adjustment. This prevents difficulties to fit the insert into the flare.
• Flexible – Different tube material and quality might require special setting of Tube Stop, Spindle Stop, flanging feed and flanging force. For best results, these parameters can be manually adjusted based on operators experience.
• Clean – The Parflange® process is environmentally clean and safe. As no heat or chemicals are used, hazards from fumes or heat do not occur.
• Perfect for on site work – The machine has special attachments for transportation by fork lift and crane. The wide base provides a safe stand. This is particularly useful for on site pipe installation in shipyards or in oil and gas exploration.
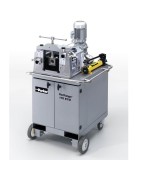