Servo Drives and Servo Drive/Controllers
Parker controllers provide up to sixteen axes of coordinated motion control for complete electromechanical, hydraulic and pneumatic motion systems. Products include stand alone multi-axis motion controllers, integrated control and drive pac
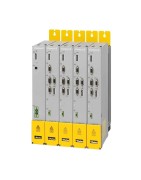
-
M300D6 / Compax3M Multi-Axis Servo Drive/Controller : 30A /...
Compax3 is Parker's global servo drive platform - offering a range of high performance single and multi-axis servo drive modules, as well as hydraulic controllers. The 'C3M' series of multi-axis servo drives and servo drive/controllers offer output power ratings from 3 to 20kVA, a 3*400/480VAC input power supply and a common PSU and DC bus connection permitting energy exchange between drives. Furthermore C3M-series drives offer a cost reduction for multi-axis applications thanks to their space-saving compact panel footprint, reduced cabling requirements and the use of centralised shared components.
Based on scalable technology functions, Compax3 drives can solve a wide range of application types - from basic analogue torque/velocity and step/direction control up to intelligent drives with advanced electronic CAM control and PLCopen function modules, programmable in accordance with IEC 61131-3 using the CoDeSys development environment. Compax3 series drives supports synchronous-, asynchronous-, linear- and torque-motor technologies, plus a wide range of feedback options including resolver, rotary and linear incremental encoders, single/multi-turn Sine-Cosine absolute encoders (EnDat & Hiperface interfaces) and analogue/digital hall sensors.
Compax3 M300D6 Hardware:
• Power Output Rating : 20kVA
• PSU Input Supply : 3*230-400/480VAC
• Drive Input Supply : 325...680 VDC
• 1 Encoder Output / 1 Encoder Input
• 8 Digital Inputs /4 Digital Outputs*
• 2 Analog Inputs (14 Bit)*
• 2 Analog Outputs (8 Bit)*
• Multiple Fieldbus Options
• Extensive Safety Technology
• Suitable for installation in 300mm control cabinets
• CE + UL/cUL Listed
*expandable via fieldbus-based expansion IO modules
Technology Functions:
• I10T10: Drive control via analog velocity/torque command, step/direction input, encoder input
• I12T11: Positioning via digital I/Os, RS232/RS485, absolute/incremental positioning,
registration mark related positioning, electronic gearbox, dynamic positioning
• T30: Programming based on IEC 61131-3 with CoDeSys
- PLCopen function modules
- IEC 61131-3 standard modules
- C3 specific function modules
• T40: as per T30 features, plus advanced electronic cam functionality
• C20: Technology controller with integrated Motion PLC (Compax3 powerPLmC-C20)
Interface/Fieldbus Options:
• RS232/485
• Ethernet
• CANopen
• DeviceNET
• PowerLink
• Profibus
• ProfiNET
• EtherCAT
Powerful multi-axis support software tool "Parker Integrated Engineering Tool", with the "Compax3 ServoManager":
- Guided configuration, with easy-to-use setup wizards
- Integrated 4-channel oscilloscope function
- Setup support
- Diagnostics/maintenance/service
- MotorManager
- Integrated CamDesigner for cam creation
ServoSignalAnalyzer for Compax3: PC-based signal analysis for mechatronic system optimisation
• Analysis and optimisation of the mechanical system
- Simple measurement of the mechanics dynamic behavior
- Vibration analysis of the mechanic construction
• Analysis and optimization of the control system
- Better and faster controller optimization
- Specific suppression of disturbances at the mechanic resonance points
Functional Safety with Compax3M
- Please refer to the "Product Support" tab for related safety information and downloads -
ViX250 Compact Servo Drive/Controller : 2.5A / 24-80VDC (250VA)
The freely-programmable, intelligent ViX servo drive delivers high levels of functionality and flexibility in programmable motion control. With outputs in the 250-500 VA power range, ViX uses field-oriented digital control technology, to give enhanced dynamic performance with improved efficiency. Housed within an extremely compact case, ViX is suitable either for direct panel mounting or for attachment to a standard DIN rail.
The ViX drive is produced in two versions having continuous current ratings of 2.5 A and 5 A at motor bus voltages up to 80VDC. A peak current capability of three times the continuous rating provides an outstanding acceleration performance. The device offers the choice of either resolver or encoder feedback (user selectable). To assist with initial commissioning, the drive can correct most motor and feedback wiring errors automatically.
ViX250 Servo Drive/Controller Features:
• Power Output Rating : 250 VA
• Drive Input Supply : 24...80VDC
• Output Current : continuous 2.5 Arms / peak 7.5 Arms for 2 seconds
• Analog Control or Built-in Controller (using Parker's proven EASI code)
• Powerful EASI-V Front-End Software
• Programmable Resolution
• Encoder and Resolver Feedback Supported
• High-Resolution Sine-Cosine Feedback Option (for use with Parker MX Linear Motor Positioners)
• Optional CANopen/RS485 Interface
• Field-oriented control for improved dynamic performance
• Panel or DIN rail mounting
• Compatible with Parker servo motors
A powerful front-end software package is supplied with the drive and permits straightforward, rapid configuration and tuning. When used with Parker servo motors, only the motor type number is required for full configuration. ViX intelligent drives incorporate a powerful controller using Parker's wellproven EASI command language. As well as carrying out all basic motion control functions, the controller performs more advanced operations such as external encoder following and registration moves. All necessary configuration is performed by software. In addition to an RS232C interface which is included in the standard drive, an optional factory-installed fieldbus module allows for both CANopen and RS485 communication. The base version of the drive can be controlled by step-direction signals in addition to an analog velocity or torque demand. ViX forms part of a new, fully-integrated system of motion control components which includes digital servo and stepper drives, power supplies, operator panels and extension I/Os. These components complement Parker's range of mechanical positioning systems which includes precision tables, electric cylinders and linear actuators. -
ViX500 Compact Servo Drive/Controller : 5.0A / 48-80VDC (500VA)
The freely-programmable, intelligent ViX servo drive delivers high levels of functionality and flexibility in programmable motion control. With outputs in the 250-500 VA power range, ViX uses field-oriented digital control technology, to give enhanced dynamic performance with improved efficiency. Housed within an extremely compact case, ViX is suitable either for direct panel mounting or for attachment to a standard DIN rail.
The ViX series servo drive is produced in two versions having continuous current ratings of 2.5 A and 5 A at motor bus voltages up to 80VDC. A peak current capability of three times the continuous rating provides an outstanding acceleration performance. The device offers the choice of either resolver or encoder feedback (user selectable). To assist with initial commissioning, the drive can correct most motor and feedback wiring errors automatically.
ViX500 Servo Drive/Controller Features:
• Power Output Rating : 500 VA
• Drive Input Supply : 48...80VDC
• Output Current : continuous 5.0 Arms / peak 15 Arms for 2 seconds
• Analog Control or Built-in Controller (using Parker's proven EASI code)
• Powerful EASI-V Front-End Software
• Programmable Resolution
• Encoder and Resolver Feedback Supported
• High-Resolution Sine-Cosine Feedback Option (for use with Parker MX Linear Motor Positioners)
• Optional CANopen/RS485 Interface
• Field-oriented control for improved dynamic performance
• Panel or DIN rail mounting
• Compatible with Parker servo motors
A powerful front-end software package is supplied with the drive and permits straightforward, rapid configuration and tuning. When used with Parker servo motors, only the motor type number is required for full configuration. ViX intelligent drives incorporate a powerful controller using Parker's wellproven EASI command language. As well as carrying out all basic motion control functions, the controller performs more advanced operations such as external encoder following and registration moves. All necessary configuration is performed by software. In addition to an RS232C interface which is included in the standard drive, an optional factory-installed fieldbus module allows for both CANopen and RS485 communication. The base version of the drive can be controlled by step-direction signals in addition to an analog velocity or torque demand. ViX forms part of a new, fully-integrated system of motion control components which includes digital servo and stepper drives, power supplies, operator panels and extension I/Os. These components complement Parker's range of mechanical positioning systems which includes precision tables, electric cylinders and linear actuators. -
IPA04-HC Single-Axis Servo Drive/Controller : 3.0A /...
The new Intelligent Parker Amplifier, or IPA, is a 1.5 axis servo drive/controller based on the ACR control platform. Available in two power levels, 400W and 1500W, the IPA can drive a wide range of rotary and linear motors and supports a number of industry standard feedback protocols. The IPA provides a dual port Ethernet interface which gives the machine builder the flexibility needed to create cost effective motion control solutions. The IPA operates as a fully programmable stand-alone motion controller with on-board I/O and virtual axis capability or can be integrated into a PLC or PC-based machine control solution. Software tools are included to optimize motion performance and efficiently monitor and manage the application.
At the core of the IPA is outstanding servo performance for the most demanding applications. The IPA can be paired with a wide range of Parker rotary and linear servo motors, utilizing cost effective incremental encoders or absolute feedback devices based on high speed serial protocols.
IPA04-HC Drive Hardware:
• Maximum Shaft Power : 400W (continuous current @240VAC)
• Power Output Rating : 1.1kVA
• Drive Input Supply : 1*100-240VAC
• Feedback Options: Incremental Encoder, Heidenhain EnDat 2.2 Absolute Encoder
• Secondary Encoder Input: Incremental Encoder (1.6 MHz, differential, A/B signals)
• Digital Inputs: 7 programmable inputs, 5-24 VDC (3 high-speed 1us capture, 4 standard)
• Digital Outputs: 4 programmable outputs, 5-24 VDC
• Analog Inputs: 2 @ 12-bit resolution
• Communications: 100 Base-T, Dual RJ-45 connectors - supports TCP/UDP and EtherNet/IP
• Development Software: ACR-View 6.4 and higher
• API: Libraries for C++,C#, VB.net, etc
• Programming Language: AcroBASIC with 1Mb of user memory
• Standards: UL Recognized 508c, CE (LVD), CE (EMC), RoHS, EtherNet/IP Conformance Tested
• Environmental: 0-45 C , 0-95% Humidity
Motion : The IPA is built on the proven and powerful AcroBASIC programming language used in the Parker ACR family of motion controllers. Project development is managed with the ACR-View development software that provides the user with the tools to program, commission, tune and debug applications. Motion and machine control features include:
• Multitasking of up to 16 different tasks
• Incremental, absolute and continuous moves
• Trapezoidal and S-Curves profiles
• High speed (1 ms) position captures
• Registration moves
• Electronic gearing and camming
Visualization : Combined with Parker's Interact Xpress HMI platform the IPA becomes an affordable machine solution. Xpress supports connections to multiple IPA and other PLCs at the same time, with an easy to use development environment and award winning graphics.
Communications : EtherNet/IP gives IPA users a popular connectivity option to PLCs for easy integration of servo motion in larger machine control application. The IPA is an EtherNet/IP adapter device supporting both I/O and Explicit Messaging. Add-On Instructions are available for seamless integration with Logix controllers. Users can also take full advantage of the IPA programming language and to create complex, custom routines called by the PLC. -
IPA15-HC Single-Axis Servo Drive/Controller : 6.3A /...
The new Intelligent Parker Amplifier, or IPA, is a 1.5 axis servo drive/controller based on the ACR control platform. Available in two power levels, 400W and 1500W, the IPA can drive a wide range of rotary and linear motors and supports a number of industry standard feedback protocols. The IPA provides a dual port Ethernet interface which gives the machine builder the flexibility needed to create cost effective motion control solutions. The IPA operates as a fully programmable stand-alone motion controller with on-board I/O and virtual axis capability or can be integrated into a PLC or PC-based machine control solution. Software tools are included to optimize motion performance and efficiently monitor and manage the application.
At the core of the IPA is outstanding servo performance for the most demanding applications. The IPA can be paired with a wide range of Parker rotary and linear servo motors, utilizing cost effective incremental encoders or absolute feedback devices based on high speed serial protocols.
IPA15-HC Drive Hardware:
• Maximum Shaft Power : 1500W (continuous current @240VAC)
• Power Output Rating : 2.5kVA
• Drive Input Supply : 1*100-240VAC
• Feedback Options: Incremental Encoder, Heidenhain EnDat 2.2 Absolute Encoder
• Secondary Encoder Input: Incremental Encoder (1.6 MHz, differential, A/B signals)
• Digital Inputs: 7 programmable inputs, 5-24 VDC (3 high-speed 1us capture, 4 standard)
• Digital Outputs: 4 programmable outputs, 5-24 VDC
• Analog Inputs: 2 @ 12-bit resolution
• Communications: 100 Base-T, Dual RJ-45 connectors - supports TCP/UDP and EtherNet/IP
• Development Software: ACR-View 6.4 and higher
• API: Libraries for C++,C#, VB.net, etc
• Programming Language: AcroBASIC with 1Mb of user memory
• Standards: UL Recognized 508c, CE (LVD), CE (EMC), RoHS, EtherNet/IP Conformance Tested
• Environmental: 0-45 C , 0-95% Humidity
Motion : The IPA is built on the proven and powerful AcroBASIC programming language used in the Parker ACR family of motion controllers. Project development is managed with the ACR-View development software that provides the user with the tools to program, commission, tune and debug applications. Motion and machine control features include:
• Multitasking of up to 16 different tasks
• Incremental, absolute and continuous moves
• Trapezoidal and S-Curves profiles
• High speed (1 ms) position captures
• Registration moves
• Electronic gearing and camming
Visualization : Combined with Parker's Interact Xpress HMI platform the IPA becomes an affordable machine solution. Xpress supports connections to multiple IPA and other PLCs at the same time, with an easy to use development environment and award winning graphics.
Communications : EtherNet/IP gives IPA users a popular connectivity option to PLCs for easy integration of servo motion in larger machine control application. The IPA is an EtherNet/IP adapter device supporting both I/O and Explicit Messaging. Add-On Instructions are available for seamless integration with Logix controllers. Users can also take full advantage of the IPA programming language and to create complex, custom routines called by the PLC. -
PD-04C Single-Axis Servo Drive with EtherCAT interface : 3.0A...
The new Parker P-Series servo systems combine compact, flexible, advanced functionality drives with high performance motors for a superior servo system, providing unique value to machine builders. Available in three power levels, from 0.4 to 3.5kW, the P-Series drives operate with a variety of machine control architectures and offer sophisticated servo capability. A number of different feedback types are supported to drive a wide range of linear and rotary servo motors. The best matches are the P-Series motors, which include absolute encoders and automatically populate motor nameplate data back to the drives for simplified commissioning. Accurate and easy to use inertia detection leads to fast set-up of tuning parameters and minimal settling time. Advanced filtering and vibration suppression features can be used to increase throughput and improve positioning performance. For high speed, real-time network applications, the PD-C series servo drive/controllers are available with EtherCAT, the fastest growing, most flexible industrial Ethernet-based motion bus.
PD-04C EtherCAT Servo Drive/Controller Overview:
• Maximum Shaft Power : 400W (at cont current) / 1200W (at peak current)
• Power Output Rating : 1.1kVA
• Drive Input Supply : 1*100-120VAC, 1/3*230VAC
• Feedback Options: Incremental Encoder, Absolute Encoder (BiSS-C, Heidenhain EnDat 2.2)
• EtherCAT Interface :
- Supported Protocols: CoE, EoE, FoE
- Drive Modes: Position/Velocity/Torque Profile, Interpolated Position, Homing, Cyclic Synchronous Position, Velocity and Torque
• Digital Inputs : 8-channel, +24V common, user selectable functions
• Digital Outputs : 4-channel, Differential (Isolated), user selectable functions
• Safety : Safe Torque Off (STO) IEC61508
• Communications : USB 2.0
• Standards: UL/cUL Recognized, CE (EMC, LVD)
• Environmental: 0-50 C , 0-95% Humidity
• Display : 7 Segment LED, 5 digits for Status and Alarms
• Dynamic Braking : Built-in, user selectable reaction -
PD-04P Single-Axis Standard (Pulse) Servo Drive/Controller :...
The new Parker P-Series servo systems combine compact, flexible, advanced functionality drives with high performance motors for a superior servo system, providing unique value to machine builders. Available in three power levels, from 0.4 to 3.5kW, the P-Series drives operate with a variety of machine control architectures and offer sophisticated servo capability. A number of different feedback types are supported to drive a wide range of linear and rotary servo motors. The best matches are the P-Series motors, which include absolute encoders and automatically populate motor nameplate data back to the drives for simplified commissioning. Accurate and easy to use inertia detection leads to fast set-up of tuning parameters and minimal settling time. Advanced filtering and vibration suppression features can be used to increase throughput and improve positioning performance.
PD-04P Standard (pulse) Servo Drive/Controller Overview:
• Maximum Shaft Power : 400W (at cont current) / 1200W (at peak current)
• Power Output Rating : 1.1kVA
• Drive Input Supply : 1*100-120VAC, 1/3*230VAC
• Feedback Options: Incremental Encoder, Absolute Encoder (BiSS-C, Heidenhain EnDat 2.2), Encoder Output (RS-422)
• Control Methods:
- Indexer Function: 64 user defined profiles, relative/absolute moves, registration, sequences and I/O selection
- External Position Control: Step and direction, CW and CCW
- External Speed Control: +/- 10V, 1:5000
- External Torque Control: +/- 10V
• Digital Inputs : 16-channel, +24V common, user selectable functions
• Digital Outputs : 8-channel, Differential (Isolated), user selectable functions
• Analog Inputs : 2-channel, +/- 10V, 12-bit resolution
• Analog Outputs : 2-channel, +/- 10V, selectable, 12-bit resolution
• Communications : USB 2.0 (firmware upload, drive configuration), RS-422 (PC/HMI interface), MODBUS-RTU
• Standards: UL/cUL Recognized, CE (EMC, LVD)
• Environmental: 0-50 C , 0-95% Humidity
• Display : 7 Segment LED, 5 digits for Status and Alarms
• Node Selection : 3 dip switches, 1 rotary for address 0-31
• Dynamic Braking : Built-in, user selectable reaction -
PD-10C Single-Axis Servo Drive with EtherCAT interface : 6.75A...
The new Parker P-Series servo systems combine compact, flexible, advanced functionality drives with high performance motors for a superior servo system, providing unique value to machine builders. Available in three power levels, from 0.4 to 3.5kW, the P-Series drives operate with a variety of machine control architectures and offer sophisticated servo capability. A number of different feedback types are supported to drive a wide range of linear and rotary servo motors. The best matches are the P-Series motors, which include absolute encoders and automatically populate motor nameplate data back to the drives for simplified commissioning. Accurate and easy to use inertia detection leads to fast set-up of tuning parameters and minimal settling time. Advanced filtering and vibration suppression features can be used to increase throughput and improve positioning performance. For high speed, real-time network applications, the PD-C series servo drive/controllers are available with EtherCAT, the fastest growing, most flexible industrial Ethernet-based motion bus.
PD-10C EtherCAT Servo Drive/Controller Overview:
• Maximum Shaft Power : 1000W (at cont current) / 3000W (at peak current)
• Power Output Rating : 2.5kVA
• Drive Input Supply : 1/3*230VAC
• Feedback Options: Incremental Encoder, Absolute Encoder (BiSS-C, Heidenhain EnDat 2.2)
• EtherCAT Interface :
- Supported Protocols: CoE, EoE, FoE
- Drive Modes: Position/Velocity/Torque Profile, Interpolated Position, Homing, Cyclic Synchronous Position, Velocity and Torque
• Digital Inputs : 8-channel, +24V common, user selectable functions
• Digital Outputs : 4-channel, Differential (Isolated), user selectable functions
• Safety : Safe Torque Off (STO) IEC61508
• Communications : USB 2.0
• Standards: UL/cUL Listed, CE (EMC, LVD)
• Environmental: 0-50 C , 0-95% Humidity
• Display : 7 Segment LED, 5 digits for Status and Alarms
• Dynamic Braking : Built-in, user selectable reaction -
PD-10P Single-Axis Standard (Pulse) Servo Drive/Controller :...
The new Parker P-Series servo systems combine compact, flexible, advanced functionality drives with high performance motors for a superior servo system, providing unique value to machine builders. Available in three power levels, from 0.4 to 3.5kW, the P-Series drives operate with a variety of machine control architectures and offer sophisticated servo capability. A number of different feedback types are supported to drive a wide range of linear and rotary servo motors. The best matches are the P-Series motors, which include absolute encoders and automatically populate motor nameplate data back to the drives for simplified commissioning. Accurate and easy to use inertia detection leads to fast set-up of tuning parameters and minimal settling time. Advanced filtering and vibration suppression features can be used to increase throughput and improve positioning performance.
PD-10P Standard (pulse) Servo Drive/Controller Overview:
• Maximum Shaft Power :1000W (at cont current) / 3000W (at peak current)
• Power Output Rating :2.5kVA
• Drive Input Supply : 1/3*230VAC
• Feedback Options: Incremental Encoder, Absolute Encoder (BiSS-C, Heidenhain EnDat 2.2), Encoder Output (RS-422)
• Control Methods:
- Indexer Function: 64 user defined profiles, relative/absolute moves, registration, sequences and I/O selection
- External Position Control: Step and direction, CW and CCW
- External Speed Control: +/- 10V, 1:5000
- External Torque Control: +/- 10V
• Digital Inputs : 16-channel, +24V common, user selectable functions
• Digital Outputs : 8-channel, Differential (Isolated), user selectable functions
• Analog Inputs : 2-channel, +/- 10V, 12-bit resolution
• Analog Outputs : 2-channel, +/- 10V, selectable, 12-bit resolution
• Communications : USB 2.0 (firmware upload, drive configuration), RS-422 (PC/HMI interface), MODBUS-RTU
• Standards: UL/cUL Listed, CE (EMC, LVD)
• Environmental: 0-50 C , 0-95% Humidity
• Display : 7 Segment LED, 5 digits for Status and Alarms
• Node Selection : 3 dip switches, 1 rotary for address 0-31
• Dynamic Braking : Built-in, user selectable reaction -
PD-35C Single-Axis Servo Drive with EtherCAT interface : 16.7A...
The new Parker P-Series servo systems combine compact, flexible, advanced functionality drives with high performance motors for a superior servo system, providing unique value to machine builders. Available in three power levels, from 0.4 to 3.5kW, the P-Series drives operate with a variety of machine control architectures and offer sophisticated servo capability. A number of different feedback types are supported to drive a wide range of linear and rotary servo motors. The best matches are the P-Series motors, which include absolute encoders and automatically populate motor nameplate data back to the drives for simplified commissioning. Accurate and easy to use inertia detection leads to fast set-up of tuning parameters and minimal settling time. Advanced filtering and vibration suppression features can be used to increase throughput and improve positioning performance. For high speed, real-time network applications, the PD-C series servo drive/controllers are available with EtherCAT, the fastest growing, most flexible industrial Ethernet-based motion bus.
PD-35C EtherCAT Servo Drive/Controller Overview:
• Maximum Shaft Power : 3500W (at cont current) / 10000W (at peak current)
• Power Output Rating : 6.4kVA
• Drive Input Supply : 1/3*230VAC
• Feedback Options: Incremental Encoder, Absolute Encoder (BiSS-C, Heidenhain EnDat 2.2)
• EtherCAT Interface :
- Supported Protocols: CoE, EoE, FoE
- Drive Modes: Position/Velocity/Torque Profile, Interpolated Position, Homing, Cyclic Synchronous Position, Velocity and Torque
• Digital Inputs : 8-channel, +24V common, user selectable functions
• Digital Outputs : 4-channel, Differential (Isolated), user selectable functions
• Safety : Safe Torque Off (STO) IEC61508
• Communications : USB 2.0
• Standards: UL/cUL Listed, CE (EMC, LVD)
• Environmental: 0-50 C , 0-95% Humidity
• Display : 7 Segment LED, 5 digits for Status and Alarms
• Dynamic Braking : Built-in, user selectable reaction -
PD-35P Single-Axis Standard (Pulse) Servo Drive/Controller :...
The new Parker P-Series servo systems combine compact, flexible, advanced functionality drives with high performance motors for a superior servo system, providing unique value to machine builders. Available in three power levels, from 0.4 to 3.5kW, the P-Series drives operate with a variety of machine control architectures and offer sophisticated servo capability. A number of different feedback types are supported to drive a wide range of linear and rotary servo motors. The best matches are the P-Series motors, which include absolute encoders and automatically populate motor nameplate data back to the drives for simplified commissioning. Accurate and easy to use inertia detection leads to fast set-up of tuning parameters and minimal settling time. Advanced filtering and vibration suppression features can be used to increase throughput and improve positioning performance.
PD-35P Standard (pulse) Servo Drive/Controller Overview:
• Maximum Shaft Power :3500W (at cont current) / 10000W (at peak current)
• Power Output Rating :6.4kVA
• Drive Input Supply : 1/3*230VAC
• Feedback Options: Incremental Encoder, Absolute Encoder (BiSS-C, Heidenhain EnDat 2.2), Encoder Output (RS-422)
• Control Methods:
- Indexer Function: 64 user defined profiles, relative/absolute moves, registration, sequences and I/O selection
- External Position Control: Step and direction, CW and CCW
- External Speed Control: +/- 10V, 1:5000
- External Torque Control: +/- 10V
• Digital Inputs : 16-channel, +24V common, user selectable functions
• Digital Outputs : 8-channel, Differential (Isolated), user selectable functions
• Analog Inputs : 2-channel, +/- 10V, 12-bit resolution
• Analog Outputs : 2-channel, +/- 10V, selectable, 12-bit resolution
• Communications : USB 2.0 (firmware upload, drive configuration), RS-422 (PC/HMI interface), MODBUS-RTU
• Standards: UL/cUL Listed, CE (EMC, LVD)
• Environmental: 0-50 C , 0-95% Humidity
• Display : 7 Segment LED, 5 digits for Status and Alarms
• Node Selection : 3 dip switches, 1 rotary for address 0-31
• Dynamic Braking : Built-in, user selectable reaction -
ACR7000 Servo Drive/Controller
The ACR7000 series multi-axis servo drive/controller combines performance, value and scalability that meets and exceeds OEM expectations. Built on the well-known ACR9000 platform, the 7000 series utilizes re-imagined hardware designs, well-suited for tabletop and laboratory style instruments and other compact machines. High performance servo drives are integrated with the multi-axis motion controller into a single package, saving space, cabling, and reducing installation complexity. Standard 4 to 8 axis systems are available. The ACR7000 series is a perfect building block for customer specific motion system solutions.
Markets:
• Industrial
• Semiconductor
• Lab/Diagnostic
• Factory Automation
Features/Benefits:
• Drive and controller in a single package, reducing wiring and installation time, and eliminating drive/controller compatibility issues.
• Multiple drive axes in a common enclosure provides a compact package that makes the most of panel space and reduces the amount of cabling and installation complexity.
• ACR7000 programs with Parker Motion Manager, a proven platform used for other Parker products.
• Generous number of digital and analog I/O points allow interfacing with the most complex machine logic.
Applications:
• Laboratory instruments
• Assembly and handling machines motion control systems
• Photonics and metrology applications