Pilot Operated Proportional Directional Control Valve - Series D30FP
Parker's series of pilot operated control valves D30FP enables higher product quality and shorter cycle times due to its outstanding dynamics. The high-precision control valve with VCD® technology closes the gap between the direct operated D3FP valve and the conventional pilot operated D31FP valve. It provides high flow capacity and practically no flow limits like the D31FP in the envelope size of the D3FP. The valve works with the hydraulic follower principle, with a moving sleeve as main spool.
Version with EtherCAT interface
The DFplus valve series D30FP with EtherCAT (NG10) interface fulfills the requirements of modern communication between valve and main control. Due to high data transmission speed and short cycle times, the high dynamics of the DFplus valves can be also utilized within the fieldbus system.
Markets:
• Industrial
• Machine tools
• Molding
Features/Benefits:
• Compact design due to hydraulic follower principle - reduces valve footprint, for easier integration
• Exceptional dynamic performance from Parker's VCD® technology - optimized cycle times for continuous high productivity
• Very good repeatability - improved process and product accuracy
• Robust valve design - minimized failure
• Digital electronics - can be easily adapted to the application, resulting in flexible use
• Short delivery time - no warehousing necessary
• Defined spool positioning at power-down - optional P-A / B-T or P-B / A-T or center position (for overlapped spools)
• With EtherCAT interface upon request - high data speeds, short cycle times
Applications:
• Injection molding
• Machine tools
Technical specification EtherCAT version
The valve is actuated and monitored by the EtherCAT interface. Actual value (spool position), temperature, operating hours and different error messages are available as diagnostic signals. The valve parameters are factory set and can be adapted with the Parker ProPxD software via the parametrizing interface.
In addition to the fieldbus communication, the valves provide the range of functions of the standard version including analogue command signal and diagnostic spare stroke. Thus they can be operated independent of the fieldbus control, particularly during commissioning and maintenance.
Version with EtherCAT interface
The DFplus valve series D30FP with EtherCAT (NG10) interface fulfills the requirements of modern communication between valve and main control. Due to high data transmission speed and short cycle times, the high dynamics of the DFplus valves can be also utilized within the fieldbus system.
Markets:
• Industrial
• Machine tools
• Molding
Features/Benefits:
• Compact design due to hydraulic follower principle - reduces valve footprint, for easier integration
• Exceptional dynamic performance from Parker's VCD® technology - optimized cycle times for continuous high productivity
• Very good repeatability - improved process and product accuracy
• Robust valve design - minimized failure
• Digital electronics - can be easily adapted to the application, resulting in flexible use
• Short delivery time - no warehousing necessary
• Defined spool positioning at power-down - optional P-A / B-T or P-B / A-T or center position (for overlapped spools)
• With EtherCAT interface upon request - high data speeds, short cycle times
Applications:
• Injection molding
• Machine tools
Technical specification EtherCAT version
The valve is actuated and monitored by the EtherCAT interface. Actual value (spool position), temperature, operating hours and different error messages are available as diagnostic signals. The valve parameters are factory set and can be adapted with the Parker ProPxD software via the parametrizing interface.
In addition to the fieldbus communication, the valves provide the range of functions of the standard version including analogue command signal and diagnostic spare stroke. Thus they can be operated independent of the fieldbus control, particularly during commissioning and maintenance.
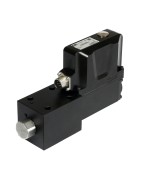