Sterowniki
Kontrolery Parker zapewniają wieloosiowe, skoordynowane sterowanie ruchem w układach elektromechanicznych i hydrauliczno-pneumatycznych. Grupa produktów obejmuje wolnostojące kontrolery ruchu, inteligentne napędy, sterowniki przenośne oraz
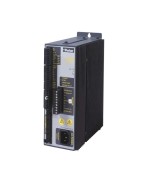
-
IQAN-XC10 expansion controller modules
The IQAN-XC10 module is one of a collection of expansion/slave controllers that can be added to an IQAN system. The IQAN expansion module communicates with an IQAN master display or controller over a CAN bus. The module has addressing in the wiring harness through use of grounded pins; the addressing of the IQAN-XC10 allows up to 3 modules of this type on the bus.
The IQAN-XC10 expansion module has 16 digital inputs for connection to switches. The IQAN-XC10 has 10 analog inputs for connection to 0-5 Vdc sensors from resistive or Hall-effect sensors and joysticks. The sensors can be powered from the 5 V reference voltage supply on the module. For flexibility, all of the analog voltage inputs can also be configured as digital inputs. There are 4 frequency inputs for active sensors, such as Hall-effect speed sensors. The XC10's inputs are configured as voltage inputs, digital inputs or frequency inputs using IQAN software tools.
The IQAN-XC10 has 16 digital outputs designed for driving on-off solenoids in a hydraulic system. The outputs can also be used for driving other types of loads, such as LEDs. Some of the outputs can also be configured as PWM outputs, for less demanding proportional functions when temperature compensation is not needed. The PWM outputs are configured in pairs, where each pair is intended for one valve section. These outputs are monitored, and use a combination of high-side and low-side switches to make it possible to shut down in the event of wiring faults.
The IQAN-XC10 is designed for use on mobile machinery. It uses two keyed 35-pin Ampseal connectors.
The XC10 module provides diagnostics by monitoring its voltage reference, input voltages, output status, and temperature. This is sent on CAN and easily viewed on the IQAN master module. It also has two LEDs for aiding diagnostics when it is connected to a master without a display. -
IQAN-XA2 expansion controller module
The IQAN-XA2 module is one of a collection of expansion/slave controllers that can be added to an IQAN system. The IQAN expansion module communicates with an IQAN master display or controller over a CAN bus. The module has addressing in the wiring harness through use of an IDtag; the addressing of the IQAN-XA2 allows up to 8 modules of this type on the bus.
The IQAN-XA2 expansion module has up to 8 voltage inputs for connection of 0-5 Vdc signals, up to 20 digital inputs for on-off signals, up to 2 frequency or 2 quadrature inputs. Inputs are multi-purpose and share pins for flexibility. The inputs are configured as voltage inputs, digital inputs, frequency inputs or as directional frequency (quadrature) inputs using IQAN software tools.
The IQAN-XA2 has 6 dedicated on-off outputs that are high-side power outputs. The expansion module also has up to 6 double proportional outputs for controlling proportional valves. These outputs can control bi-directional valve sections or single solenoid devices (i.e. proportional cartridge valves). The proportional outputs can be used in two different modes. Either Current mode (current closed loop PWM) or PWM mode (voltage open-loop PWM) signals can be selected and the parameters configured using IQAN software. For flexibility these outputs may also be configured as on/off outputs or on/off inputs. For flexibility, the proportional outputs, on-off outputs and on-off inputs share pin positions and are configured using IQAN software tools.
The IQAN-XA2 aluminum housing is designed to be rugged, but light and has a sealed, automotive connector. The unit has a membrane to prevent condensation inside the housing. The IQAN-XA2 expansion controller is designed for the outdoor environment.
IQAN-XA2 expansion modules execute a self-test during start up and cyclic operation. An internal watch dog checks for software errors and will interrupt outputs if errors are detected. The XA2 is made using selected components and conforms to strict international requirements. For diagnostics: If an error is detected an LED on the top of the controller flashes a sequence to indicate the nature of the error and assist in troubleshooting. -
Sterowniki rozszerzeń — IQAN-XC21/XC22/XC23
Moduły rozszerzające IQAN-XC21/XC22/XC23 firmy Parker stanowią podzbiór sterowników rozszerzających/podrzędnych, które można dodać do systemu IQAN. Forma obudowy umożliwia układanie modułów w wieżę, co pozwala uzyskać dużą gęstość wejść/wyjść na niewielkiej powierzchni.
Moduł IQAN-XC21 jest przeznaczony do użytku w kabinach maszyn mobilnych. Dzięki wyjątkowo małemu rozmiarowi idealnie nadaje się do stosowania w elementach sterujących zamontowanych w podłokietnikach. Wykorzystuje cztery konektory Molex Micro-fit o różnej gęstości upakowania styków, co zapobiega pomyleniu przewodów.
Moduły IQAN-XC22 i IQAN-XC23 są przeznaczone do użytku na zewnątrz maszyn mobilnych. Uszczelniona obudowa jest wyposażona w 2 lub 3 konektory Deutsch DTM z wpustem, co zapobiega pomyleniu przewodów.
Moduły IQAN-XC21, XC22 oraz XC23 mają wejścia cyfrowe do podłączenia przełączników. Te elastyczne wejścia można skonfigurować jako wejścia częstotliwościowe lub wejście kodera do pomiarów prędkości i położenia. Moduły XC21 i XC23 mają również wejścia napięciowe do podłączenia czujników Halla i joysticków.
Wyjścia cyfrowe małej mocy w modułach IQAN-XC21, XC22 i XC23 są przeznaczone do sterowania obciążeniami o małej mocy, takimi jak przekaźniki, diody LED lub brzęczyki alarmowe. Funkcjonalność definiuje się w programie jednostki głównej IQAN za pomocą łatwych w obsłudze narzędzi programistycznych IQAN.
Sterowniki rozszerzeń IQAN-XC21/XC22/XC23 są doskonałym dodatkiem umożliwiającym rozszerzanie wejść/wyjść na potrzeby dowolnego zastosowania w maszynach mobilnych.
Rynki:
• Sprzęt budowlany
• Transport
• Maszyny rolnicze
• Sprzęt do transportu materiałów
Cechy i korzyści:
• Monitorowanie do 20 wejść — analogowych, cyfrowych lub częstotliwościowych
• Niewielkie wymiary umożliwiające montaż w podłokietnikach lub innych ciasnych przestrzeniach
• Jednostka podrzędna niewymagająca programowania
• Wersje uszczelnione do użytku na zewnątrz
• Komunikacja CAN
Zastosowania:
• Adaptacja wielu wejść tablicy rozdzielczej do magistrali CAN
• Sterownik przekaźnika
• Sterowanie hydrauliką pomocniczą -
IQAN-XS2 expansion controller module
The IQAN-XS2 module is one of a collection of expansion/slave controllers that can be added to an IQAN system. The IQAN expansion module communicates with an IQAN master display or controller over a CAN bus. The module has addressing in the wiring harness through use of an IDtag; the addressing of the IQAN-XS2 allows up to 8 modules of this type on the bus.
The IQAN-XS2 expansion module has up to 8 voltage inputs for connection of 0-5 Vdc signals and up to 20 digital inputs for on-off signals. Inputs are multi-purpose and share pins for flexibility. The inputs are configured as voltage or digital inputs using IQAN software tools.
The IQAN-XS2 has 12 dedicated on-off outputs that are high-side power outputs.
The IQAN-XS2 aluminum housing is designed to be rugged, but light and has a sealed, automotive connector. The unit has a membrane to prevent condensation inside the housing. The IQAN-XS2 expansion controller is designed for the outdoor environment.
IQAN-XS2 expansion modules execute a self-test during start up and cyclic operation. An internal watch dog checks for software errors and will interrupt outputs if errors are detected. The XS2 is made using selected components and conforms to strict international requirements. For diagnostics: If an error is detected an LED on the top of the controller flashes a sequence to indicate the nature of the error and assist in troubleshooting. -
Vansco Multiplexing Module VMM0604
The VMM0604 is a general purpose controller for vehicle and other applications with a steady voltage of less than or equal to 32 Vdc. VMM0604 has a 6 inputs and 4 outputs as well as a CAN/J1939 communication port. The VMM0604 is 100% compatible with other Parker Vansco multiplexing modules.
The VMM0604 has 6 general purpose inputs capable of being configured for active high or active low signals. Additionally they may be used for reading analog voltages, or as 6 frequency inputs (2 AC coupled and 4 DC coupled). The VMM0604 has 4 high-side outputs with a max PWM frequency of 500 Hz, and 4 low-side outputs capable of current sensing. Outputs can drive any type of vehicle load including relays, solenoids, fans, etc.
Built to meet stringent SAE J1455/EP455 environmental standards, the system advances multiplexing technology through enhanced diagnostics and Windows-based ladder logic programming. The unit can be used alone or with other multiplexing modules. The multiplexing system was designed to simplify and reduce electrical system troubleshooting, maintenance, and file management time. The modules are self-programming and have status LEDs that indicate the condition of inputs, outputs, power, and network activity.
The VMM0604 monitors its outputs continuously for fault information. Detected faults include short circuits (to ground or power), over currents and open load.
The VMM0604 allows systems to reduce the number of fuses by allowing the outputs to protect themselves electronically. In the event of a fault, the unit will disable the output(s) that are faulted. The VMM0604 has 12 red diagnostic LEDs that can be used to indicate the status of inputs, outputs, power and the Controller Area Network (CAN).
On-board diagnostics facilitate easier troubleshooting, and modules like the VMM0604 that can be auto-programmed relieve time and maintenance costs by keeping module and program inventory to a minimum. VMM users appreciate the module's robust design as well as its adherence to stringent industry environmental requirements and communications (SAE J1939) standards. All of these features make the controller easy to integrate into any on-highway or off-highway vehicle. -
Vansco Multiplexing Module VMM1615
The VMM1615 is a general purpose controller for vehicle and other applications with steady state voltages less than or equal to 32 Vdc. It has 16 inputs and 15 outputs as well as two CAN/J1939 communication ports. This module is 100% compatible with other Parker Vansco multiplexing modules.
The VMM1615 has Wake on CAN functionality. It has 7 digital inputs; 5 of the inputs are used for reading active high/low signals, 1 input is used for reading active high signals, and 1 input is used for active high power control. In addition, it has 8 inputs capable of reading analog voltages, and 1 DC coupled frequency input.
The VMM1615 has 12 high-side outputs with a max PWM frequency of 500 Hz, 4 of which are capable of accurate current sensing. It also has 1 low-side output that is capable of current sensing with a max PWM frequency of 1500 Hz, and 2 solid state relay outputs. These outputs can drive a variety of load types.
Built to meet and exceed SAE J1455 environmental standards, the system advances multiplexing technology through enhanced diagnostics and Windows-based ladder logic programming. The VMM1615 can be used alone or with other multiplexing modules. The multiplexing system was designed to simplify and reduce electrical system troubleshooting, maintenance, and file management time. The module is plug and play configurable, and has status LEDs that indicate the condition of inputs, outputs, power, and network activity.
The VMM1615 monitors its 15 outputs continuously for fault information. Detected faults include short circuits (to ground or power), over currents and open load. The VMM1615 allows systems to reduce the number of fuses by allowing the outputs to protect themselves electronically. In the event of a fault, the unit will disable the output(s) that are faulted.
On-board diagnostics facilitate easier troubleshooting, and modules that can be auto-programmed relieve time and maintenance costs by keeping module and program inventory to a minimum. VMM users appreciate the module's robust design as well as its adherence to stringent industry environmental requirements and communications (SAE J1939) standards. All of these features make the controller easy to integrate into any on-highway or off-highway vehicle. -
Vansco Multiplexing Module VMM2404
The VMM2404 is a general purpose controller for vehicle and other applications with a steady voltage of less than or equal to 32 Vdc. VMM2404 has a 24 inputs and 4 high-side outputs as well as a CAN/J1939 communication port. The VMM2404 is 100% compatible with other Parker Vansco multiplexing modules.
The VMM2404 has 9 dedicated digital inputs, and 15 general purpose inputs capable of being configured for active high or active low signals. Additionally the general purpose inputs may be used for reading analog voltages, or as frequency inputs (2 AC coupled and 13 DC coupled).The VMM2404 has 4 high-side outputs with a max PWM frequency of 500 Hz, and 4 low-side outputs capable of current sensing. Outputs can drive any type of vehicle load including relays, solenoids, fans, etc.
Built to meet stringent SAE J1455/EP455 environmental standards, the system advances multiplexing technology through enhanced diagnostics and Windows-based ladder logic programming. The unit can be used alone or with other multiplexing modules. The multiplexing system was designed to simplify and reduce electrical system troubleshooting, maintenance, and file management time. The VMM modules are self-programming and have status LEDs that indicate the condition of inputs, outputs, power, and network activity.
The VMM2404 monitors its outputs continuously for fault information. Detected faults include short circuits (to ground or power), over currents and open load.
The VMM2404 allows systems to reduce the number of fuses by allowing the outputs to protect themselves electronically. In the event of a fault, the unit will disable the output(s) that are faulted. The VMM2404 has 30 red diagnostic LEDs that can be used to indicate the status of inputs, outputs, power and the Controller Area Network (CAN).
On-board diagnostics facilitate easier troubleshooting, and modules like the VMM2404 that can be auto-programmed relieve time and maintenance costs by keeping module and program inventory to a minimum. VMM users appreciate the module's robust design as well as its adherence to stringent industry environmental requirements and communications (SAE J1939) standards. All of these features make the controller easy to integrate into any on-highway or off-highway vehicle. -
Vansco Multiplexing Module VMM3120
The VMM3120 is a general purpose controller for vehicle and other applications with steady state voltages less than or equal to 32 Vdc. It has 31 inputs and 20 outputs as well as two CAN/J1939 communication ports. This module is 100% compatible with other Parker Vansco multiplexing modules.
The VMM3120 has 17 digital inputs. The digital inputs are used for reading active high signals. Two of the inputs may be used for power control. In addition, it has 10 inputs capable of reading analog voltages, and 4 frequency inputs (2 AC coupled and 2 DC coupled).
The VMM3120 has 16 high-side outputs with a max PWM frequency of 500 Hz, and 4 low-side outputs capable of current sensing. Outputs can drive any type of vehicle load including relays, solenoids, fans, etc.
Built to meet stringent SAE J1455 environmental standards, the system advances multiplexing technology through enhanced diagnostics and Windows-based ladder logic programming. The unit can be used alone or with other multiplexing modules. The multiplexing system was designed to simplify and reduce electrical system troubleshooting, maintenance, and file management time. The modules are self-programming and have status LEDs that indicate the condition of inputs, outputs, power, and network activity.
The VMM3120 monitors its 20 outputs continuously for fault information. Detected faults include short circuits (to ground or power), over currents and open load. The VMM3120 allows systems to reduce the number of fuses by allowing the outputs to protect themselves electronically. In the event of a fault, the unit will disable the output(s) that are faulted.
On-board diagnostics facilitate easier troubleshooting, and modules that can be auto-programmed relieve time and maintenance costs by keeping module and program inventory to a minimum. VMM users appreciate the module's robust design as well as its adherence to stringent industry environmental requirements and communications (SAE J1939) standards. All of these features make the controller easy to integrate into any on-highway or off-highway vehicle. -
Vansco Multiplexing Module VMM1210
The VMM1210 is a general purpose controller for vehicle and other applications with steady state voltages less than or equal to 32 Vdc. It has 31 inputs and 20 outputs as well as a CAN/J1939 communication port. This module is 100% compatible with other Parker Vansco multiplexing modules.
The VMM1210 has 8 programmable digital inputs, all of which are capable of doing power control, and reading active high, or active low inputs. In addition, it has 4 inputs capable of reading analog voltages, frequency values or digital active low inputs. The VMM1210 has 8 high current (10 A max) high-side outputs. It also has two low current (3 A max) outputs capable of driving either high-side or low-side loads, and can also be arranged in an H-Bridge configuration. Outputs can drive any type of vehicle load including lights, relays, solenoids, fans, etc.
The VMM1210 processes ladder logic written using VMMS software. The ladder logic defines which inputs or arrangement of inputs turns on outputs on the module. The inputs and outputs in the ladder logic can be from one or more modules connected together in a system via the CAN/J1939 network.
The multiplexing system was designed to simplify and reduce electrical system troubleshooting, maintenance, and file management time. The module has status LEDs that indicate the condition of inputs, outputs, power, and network activity.
The VMM1210 monitors its 10 outputs continuously for fault information. Detected faults include short circuits (to ground or power), over currents and open load. The VMM1210 allows systems to reduce the number of fuses by allowing the outputs to protect themselves electronically. In the event of a fault, the unit will disable the output(s) that are faulted.
On-board diagnostics facilitate easier troubleshooting, and modules that can be auto-programmed relieve time and maintenance costs by keeping module and program inventory to a minimum. VMM users appreciate the module's robust design as well as its adherence to stringent industry environmental requirements and communications (SAE J1939) standards. All of these features make the controller easy to integrate into any on-highway or off-highway vehicle. -
CM0711 Controller Module, semi-custom
The CM0711 is a rugged CAN controller. It is mainly intended for applications such as powertrain control (e.g. power shift transmissions), implementing single features on a vehicle (like auxiliary hydraulics control), or to act as an additional controller in systems where the existing main controller does not provide enough I/O for the system.
The CM0711 main focus is on high-end output control with closed loop current control, but it also is capable of measuring analog and digital input signals. Several modules on the system can be identified using addressing IDtag inputs built into the wire harness.
The CM0711 has a software development kit (SDK) that allows customers to develop their own software. The CM0711R is able to be programmed using the Raptor software tool.
The CM0711 can control proportional valves using current mode (current closed-loop) or PWM mode (voltage open-loop) signals. The module has 7 high-side outputs with error detection, and 4 low-side outputs. The analog inputs accept 0-5V signals from input devices or sensors. Digital inputs can also be configured to measure 2 frequency or 1 directional frequency (quadrature) inputs. High-side outputs may alternatively be used as digital inputs for switches.
The aluminum housing is designed to be rugged, and has 2 environmentally-sealed, 18-pin Deutsch DT14-18 type of connector. This controller is designed for the outdoor environment.
An internal watch dog checks for software errors and will interrupt outputs if errors are detected. The outputs have diagnostics i.e. open load, current feedback. The reference output voltage, used for sensor supply, can be diagnosed. Also supply voltage can be monitored, as well as some of the internal signals. The module has an internal temperature sensor for protecting the module and system devices. A diagnostics LED is situated in the top of the module. -
IQAN-TOC2 standalone valve driver modules
The IQAN-TOC2 is a task oriented controller in the IQAN product group. The IQAN-TOC2 replaces valve driver modules and cards for a wide variety of proportional valves or other devices.
The IQAN-TOC2 is a general purpose unit that can control two bi-directional valve sections or two cartridge solenoids simultaneously. The IQAN-TOC2 communicates with a variety of input and output devices. It has regulated current mode (current closed-loop) or PWM mode (voltage open-loop) output for proportional valve control. The analog inputs accept signals from joysticks or potentiometers. Two digital inputs can be used to read switches.
The IQAN-TOC2 has a simple mechanical interface for calibration. With a preloaded personality from the factory, setup can be easily performed on the machine using a screwdriver. Adjustments possible include threshold, maximum output and slopes. The IQAN-TOC2 may also be connected to a PC and programmed using IQANdevelop software to change the functionality of the controller. This advanced feature allows the IQAN-TOC2 to be used in more demanding applications.
The housing is designed to be rugged, but light and has a sealed, automotive AMP junior-power timer connector. The IQAN-TOC2 has a membrane to prevent condensation inside the housing. This controller is designed for the outdoor environment.
The IQAN-TOC2 is made using selected components and conforms to strict international requirements.
Diagnostics: If an error is detected an LED on the top of the controller flashes a sequence to indicate the nature of the error. -
CM0410 Controller Module, J1939 slave
The CM0410 is a general purpose input / output controller that includes a single CAN interface, 4 inputs, 1 high side current measurement pass-through, and 10 high side outputs with error checking. The main function of the module is to provide a means of controlling mechanical relays or low current loads via J1939 messages on the CAN bus. The CM0410 can support things like open bulb detection and some limited solenoid PWM control.
The CM0410 is a CAN slave module only and does not support standalone operation. The CM0410 does have limited configurability using a PC tool, to specify things like input configurations, and update rates for the messages presented on the CAN bus. -
CM2115 controller module, semi-custom
The CM2115 controller module is a general purpose input/output controller that monitors digital, analog, and frequency inputs, and controls solid-state switched outputs. The principal benefit of the CM2115 is that it can be configured to meet many system requirements through custom software.
The CM2115 is designed to communicate through a J1939-based Controller Area Network (CAN). Custom CAN messaging can be created in software, and the CM2115 can be used in any CAN 2.0B application, including ISO 11783.
The software offered with the CM2115 is a low-level framework that uses the Parker Vansco Software Development Kit (SDK), which is a tool that enables you to create custom application software for your product. The CM2115R is programmed using the Raptor software tool.
The CM2115 has many features, including the following:
• The CM2115 has 21 inputs; analog, frequency and digital inputs.
• The CM2115 has 15 outputs; 8 x High Side (6 x 10A and 2 x 5A), 2 x High Side 5A with accurate current sense, 2 x High Side 2.5A with accurate current sense, 1 x Low Side 2.5A with accurate current sense, 2 x solid state relay 1A.
• The CM2115 can provide a sensor power supply output rated at up to 300 mA.
• The CM2115 has 2 CAN busses, one with wake-on CAN function.
• The CM2115 has four 12-pin Deutsch DT connectors. -
CM3620 Controller Modules, semi-custom
The CM3620 is a general purpose input/output controller that monitors digital, analog and frequency inputs, and controls solid-state switched outputs.
The principal benefit of the CM3620 is the high I/O count and that it can be configured to meet many system requirements through custom software.
The CM3620 is designed to communicate through a J1939-based Controller Area Network (CAN). Custom CAN messaging can be created in software, and the CM3620 can be used in any CAN 2.0B application, including ISO 11783. The software offered with the CM3620 is a low-level framework that uses the Parker Vansco Software Development Kit (SDK), which is a tool that enables you to create custom application software for your product.
The CM3620 can monitor up to 36 inputs:
• 22 digital inputs
• 10 analog inputs
• 4 frequency inputs
The CM3620 analog inputs, frequency inputs, and high-side outputs can be configured to function as digital inputs
The CM3620 can control up to 20 outputs:
• 16 high-side outputs
• 4 low-side outputs
The CM3620 low-side outputs can be used for current feedback if a high-side output is used for pulse-width modulation (PWM) control.
The CM3620 can provide a sensor power supply output rated at up to 300 mA.
The CM3620 has two 35-pin Ampseal connectors that are used to interface with the inputs, outputs, and CAN communication. -
CM3626 Controller Module, semi-custom
The CM3626 is a general purpose input/output controller that can be used to monitor digital, analog and frequency inputs, and drive system loads. It is intended to be used in a range of vehicles including agricultural, on highway trucks, on highway buses, and off-road construction equipment. It can be used in systems where hydraulic control, lighting control, or general electrical control is required.
The CM3626 is designed to communicate through a J1939-based Controller Area Network (CAN). Custom CAN messaging can be created in software, and the CM3626 can be used in any CAN 2.0B application, including ISO 11783. The CM3626 is programmable in C using the CM3626 non-SIL Platform Framework API. The CM3626R is programmed using Raptor software tools.
The CM3626 can monitor up to 36 inputs:
• 32 analog inputs
• 4 frequency inputs
The CM3626 analog inputs and frequency inputs can be configured to function as digital inputs
The CM3626 can control up to 26 outputs:
• 18 high-side outputs (2 x 5A, 16 x 2 A)
• 8 low-side outputs (6 x 5A, 2 x 10A)
The CM3626 can provide a 5V or 8V sensor power supply output rated at up to 1A.
The CM3626 has 5 Deutsch DT series, 18 pin connectors for interfacing with system wire harnesses. -
Sterowniki główne — IQAN-MC41/MC42/MC43
IQAN-MC41, -MC42 i -MC43 firmy Parker to wytrzymałe sterowniki główne, zaprojektowane jako idealne rozwiązanie do hydraulicznych systemów sterowania w pojazdach i mobilnych maszynach hydraulicznych. Sterowniki główne Parker IQAN® umożliwiają optymalizację architektury systemów, przyspieszając prace rozwojowe, co przekłada się na zwiększenie przychodów producentów OEM.
Sterowniki główne rodziny MC4x są dostępne w 3 rozmiarach, o różnej liczbie lokalnych wejść/wyjść do obsługi wejść/wyjść oraz różnych sterownikach magistrali CAN do diagnostyki i obsługi bramy CAN. Wytrzymała aluminiowa obudowa ma uszczelnione przyłącza samochodowe i jest przystosowana do użytku w trudnych warunkach zewnętrznych.
Zastosowania w maszynach dla sterowników głównych MC4x można w prosty sposób tworzyć dzięki łatwym w obsłudze narzędziom programistycznym IQAN. W rezultacie sterowniki główne IQAN-MC41, -MC42 i -MC43 doskonale sprawdzą się w dowolnym zastosowaniu w maszynie mobilnej.
Rynki:
• Sprzęt budowlany
• Maszyny rolnicze
• Górnictwo
• Sprzęt do transportu materiałów
Cechy i korzyści:
• Wersje bezpieczeństwa standardowe i SIL2
• 3 rozmiary sterowników na potrzeby wymagań dowolnych systemów, od małych do dużych
• Wyjścia sygnału z modulacją szerokości impulsów do sterowania proporcjonalnego zaworami hydraulicznymi
• Obsługa szerokiej gamy typów wejść: 0–5 V, 0–10 V, 4–20 mA, PWM, cyfrowych i częstotliwościowych
• Łatwe w obsłudze narzędzia programowania
• Uszczelnienie pod kątem użytku na zewnątrz
• Wiele magistral CAN
Zastosowania:
• Sterowanie żurawiem
• Sterowanie koparką
• Sterowanie ładowarką teleskopową
• Sprzęt do podziemnych kopalni skał twardych
Istnieją 2 wersje rodziny MC4x:
• Wersja Performance zoptymalizowana pod kątem szybkości obliczeń
• Wersja zakwalifikowana do poziomu SIL2 i oznaczona jako FS, przeznaczona do wdrażania bezpieczeństwa funkcjonalnego
Sterowniki IQAN-MC4xFS zostały zaprojektowane zgodnie z normą IEC 61508 dla poziomu SIL2. -
Servo Drive Series Compax3F
The Compax3F is a part of the servo drive family of Parker Hannifin. It is especially designed for the requirements of electrohydraulic systems and in particular for position and force control of electrohydraulic axis.
Position, velocity force/pressure control, synchronous run and cam function for up to 32 axes can be precisely adapted to specific use. Compax3F has been successfully established in the market and has proven best suitable in most sophisticated applications such as die casting, metal forming, blow molding, tube bending and many more.
Together with the electromechanical axis controller from the Parker Automation team, the Compax family opens new windows of opportunity for energy saving hybrid solutions. On top, the latest version of Compax3F is a big step ahead in easy, customer friendly axis control.
Main features and functions
• Technology function T11:
- Profile table
- No programming skills required
- Up to 31 motion profils, e.g. absolute/relative position, force/pressure control, reg-related positioning or electronic gearing
- Direct positioning via Profibus
- Synchronous run for up to 2 hydraulic axes possible with just one electrohydraulic controller C3F*T11
• EtherCAT (Option I31):
- Real-time Ethernet protocol
- Available for technology functions T30 and T40
• New force/pressure controller:
- Additional force forward and velocity feedback for optimal force/pressure control
• Controller pre-setting:
- Automatic controller set-up for position controlling
• Extended valve database:
- With latest update of all Parker valves
• Multi-axis tool:
- Database for multi-axis configurations
- Documentation of project related data feasible
Large drive range
• Valves:
- Proportional directional control valves
- Proportional pressure relief- and pressure reducing valves
- Flow valves
• Drives:
- Cylinders
- Rotary drives
- Motors
Range of applications
• Closed loop position and force control of linear cylinders and rotary drives
• Switching between position and force control
• Synchronous run with up to 64 axes
Typical applications
• Feeder axis
• Position and force control of press cylinders in material forming machines
• Roller clearance control in roller presses
• Die casting machines
• Custom-designed software packages on request -
PACIO Remote I/O System
Leveraging the power of the EtherCAT E-bus, PACIO is a modular IO system that seamlessly integrates with the Parker Automation Controller (PAC) to create a custom IO solution to fit any application need. PACIO modules use tool-less, snap-on connectors to build complete remote and local IO stacks within seconds. PACIO modules allow for combinations of digital and analog IO, temperature RTD sensors, and counter/encoder options.
PACIO Remote I/O System - Features:
• Connections between PACIO made over an EtherCAT, E-bus network
• Short-circuit protection
• Easy to extend with additional modules
• Exceptionally compact design
• Great flexibility ensures optimal adaptability in different applications
• Error and status display (LED)
PACIO Technical Characteristics - Overview:
• Digital Inputs/Outputs :
24Vdc opto-isolated, PNP and NPN options
Up to 32 inputs/outputs per module
Up to 1 A per channel
• Analog Inputs :
Up to 8 single-ended or 4 differential per module
0-10V, ±10V, 0-20mA, 4-20mA, 12-bit
0-10V, ±10V, 13-bit
• Analog Outputs :
Up to 4 single ended or differential per module
0-10V, ±10V, 0-20mA 12-bit
• Temperature :
4-channels of 16-bit Pt/Ni RTD inputs
Pt100 Measuring Range: -75-670 C
Ni100 Measuring Range: -60-250 C
Options for 70-300Ω or 70-3000Ω
• High-Speed Counter/Encoder Module :
24Vdc PNP inputs
24Vdc outputs
Max count rate: 400kHz
Analog out, ±10V 12-bit
• Profibus Module
• Operating Temperature : 0-55°C / 32-131°F
• Enclosure Rating : IP20 -
High Current Controller Module - CM0504
The CM0504 Slave Control Module is a high current controller that includes a single CAN interface, 5 inputs and 4 outputs with error checking. The main function of the module is to provide a means of controlling high current loads through messages on the CAN bus. Each output is capable of 25 amps for a combined total of 100 amps continuous. The module outputs can be configured to support up to two full H-bridge motor drives to control directional motors. Using a PC tool, the user is able to define parameters such as high side, low side and H-bridge outputs. The CM0504 is only available as a CAN slave module.
Markets:
• Agriculture
• Construction equipment
• Forestry
• Material handling
• Transportation and on-highway vehicles
Features / Benefits:
The CM0504 has 5 analog inputs which are programmable as pull-up or pull-down
• 4 are capable of being frequency, analog (0-5V) or digital inputs.
• 1 is dedicated for wake-up
The CM0504 has 4 high current outputs rated to 25 Amp each, with configuration capabilities:
• high side: 25 Amp (each with PWM and current feedback), or
• low side: 25 Amp, or
• up to 2 H-bridge
Applications:
• Electric Actuators
• Electric Fans / Heaters
• High Current Work Lamps
• Electric Doors / Wipers -
Sterowniki rozszerzeń — IQAN-XC41/XC42/XC43/XC44
Moduły IQAN-XC41, -XC42, -XC43 i -XC44 firmy Parker to wytrzymałe sterowniki rozszerzające, zaprojektowane jako idealne rozwiązanie do rozbudowy wejść/wyjść hydraulicznych systemów sterowania w pojazdach i mobilnych maszynach hydraulicznych. Sterowniki IQAN® firmy Parker umożliwiają optymalizację architektury systemów, przyspieszając prace rozwojowe, co przekłada się na zwiększenie przychodów producentów OEM.
Sterowniki rozszerzające z rodziny XC4x są dostępne w 4 rozmiarach z różną liczbą lokalnych we/wy do obsługi wejść/wyjść oraz wielu sterowników magistrali CAN do diagnostyki i obsługi bramki CAN. Wytrzymała aluminiowa obudowa ma uszczelnione przyłącza samochodowe i jest przystosowana do użytku w trudnych warunkach zewnętrznych.
Dodawanie sterowników rozszerzających XC4x do zastosowań w maszynie jest proste dzięki łatwym w obsłudze narzędziom do programowania IQAN. Dzięki temu sterowniki rozszerzające IQAN-XC41, -XC42, -XC43 i -XC44 doskonale nadają się do wszelkich zastosowań w maszynach mobilnych.
Rynki:
• Sprzęt budowlany
• Maszyny rolnicze
• Górnictwo
• Sprzęt do transportu materiałów
Cechy i korzyści:
• 4 rozmiary sterowników na potrzeby wymagań dowolnych systemów, od małych do dużych
• Wyjścia sygnału z modulacją szerokości impulsów do sterowania proporcjonalnego zaworami hydraulicznymi
• Obsługa szerokiej gamy typów wejść: 0–5 V, 0–10 V, 4–20 mA, PWM, cyfrowych i częstotliwościowych
• Łatwe w obsłudze narzędzia programowania
• Uszczelnienie pod kątem użytku na zewnątrz
• Wiele magistral CAN
Zastosowania:
• Sterowanie żurawiem
• Sterowanie koparką
• Sterowanie ładowarką teleskopową
• Sprzęt do podziemnych kopalni skał twardych -
Electrohydraulic Control Module - Series PACHC
Parker’s PACHC is a control module for operation at a Parker Automation Controller (PAC) for high-dynamic and precise control of hydraulic axes. This real-time electrohydraulic axis controller enables position, force and pressure control as well as changeover control. In conjunction with a PAC120 or PAC320 it is used as EtherCAT slave. It features analogue as well as digital sensor inputs.
The PACHC is connected to local analogue sensors like pressure and force sensors and digital position feedback systems for recording actual values. Hydraulic valves are controlled via the analogue outputs. Due to its extremely compact dimensions and its modular design, the PACHC can be used in many different applications.
Markets:
• Industry
• Machine tools
• Molding
Features/benefits:
• Position, force, pressure and change-over control for 1-2 hydraulic axes – two or more valves with only one unit
• Sampling time 250 µs – extremely fast cycle times e.g. for die casting applications
• Modular system – can be optimally adapted to the respective application with additional modules
• Compact dimensions – requires less mounting space in the cabinet
• Free-of-charge preconfigured software modules (with PAC) – lower programming effort and faster commissioning
• Customized software solutions (with PAC) on request
• Hard- and software from a single source – simplifies purchasing and service
Applications:
• Suitable for general hydraulic applications
• Presses
• Die Casting
• Metal forming
• Machine tools
• Injection molding
Accessories:
Parker Automation Controller PAC120
The Parker Automation Controller PAC120 is a PLC with integrated, programmable software and EtherCAT master function. It was developed for the automation of fast and precise hydraulic processes. Together with the control module PACHC, it enables the position and force/pressure control of up to 40 hydraulic axes. In combination with the PACIO modules it can take over complete control. Through its compact dimensions and its modular design, it can be used in various applications.
Parker Remote I/O System PACIO
The PACIO System comprises a variety of modules for digital, analog and temperature signals as well as communication interfaces. The modules connect directly to the controller via the built-in EtherCAT bus for local architectures and are extended to remote locations via the extender and bus coupler modules, thus supporting both local and distributed I/O architectures. PACIO communicates natively on the EtherCAT bus, therefore it provides the full functionality and throughput of high-speed EtherCAT to meet the most demanding real-time requirements. -
Parker Automation Controller - Series PAC120
Parker’s Automation Controller PAC120 was developed for the automation of fast and precise hydraulic processes. Together with the control module PACHC, the compact PLC with integrated, programmable software and EtherCAT master function enables the position and force/pressure control of up to 40 hydraulic axes. In combination with the PACIO modules it can take over complete control.
Due to its extremely compact dimensions and its modular design, the PAC120 can be used in many different applications. Data exchange with other systems is firstly possible via the on-board Industrial Ethernet and OPC UA interfaces. In addition, further communication links can be realized by use of interface and bus modules. This also facilitates system integration in existing control architectures. Using an extender module enables to actuate external EtherCAT slaves.
Markets:
• Industry
• Machine tools
• MoldingFeatures/benefits:
• A single integrated development environment for programming logic, IO, visualization and motion – reduces time for application development
• Optimized for control of presses and die casting machines with two or more control valves
• IEC61131-3 and PLCopen Motion – standardized programming
• Modular system – can be optimally adapted to the respective application with additional modules
• Compact dimensions – requires less mounting space in the cabinet
• Free-of-charge preconfigured software modules – lower programming effort and faster commissioning
• Customized software solutions on request
• Hard- and software from a single source – simplifies purchasing and service
• OPC UA – IoT-ready, prerequisite for networking of machinesApplications:
• Suitable for general hydraulic applications
• Presses
• Die Casting
• Metal forming
• Machine tools
• Injection moldingAccessories:
Parker Control Module PACHC
The PACHC ist a control module for high-dynamic and precise control of 1-2 hydraulic axes. It was developed for operation at the Parker Automation Controller PAC120. The device is an EtherCAT slave and is operated at the Parker E-Bus. In conjunction with the bus coupler PACIO-400-00 it can be used in a standard EtherCAT network. The PACHC is connected to local analog sensors like pressure and force sensors and digital position feedback systems for recording actual values. Hydraulic valves are controlled via the analog outputs.Parker Remote I/O System PACIO
The PACIO System comprises a variety of modules for digital, analog and temperature signals as well as communication interfaces. The modules connect directly to the controller via the built-in EtherCAT bus for local architectures and are extended to remote locations via the extender and bus coupler modules, thus supporting both local and distributed I/O architectures. PACIO communicates natively on the EtherCAT bus, therefore it provides the full functionality and throughput of high-speed EtherCAT to meet the most demanding real-time requirements. -
Semi-custom Controller Module - CM2723
The CM2723 configurable mobile controller's I/O allows integration into multiple applications reducing your BOM spend. Parker’s CM2723 is a rugged CAN controller with a focus on compact design. Its inputs can measure analog, digital and frequency signals, while the PWM (pulse width modulated) capable outputs are ideally suited for hydraulic valve control. The CM2723 may serve as the main controller in a range of vehicle markets including agriculture and off-road construction equipment or may be combined with other modules in a large system. Equipped with plastic housing and 2 environmentally sealed, 35-pin keyed connectors, this controller is designed to stand up to outdoor environments.
The CM2723 has a software development kit (SDK) that allows customers to develop their own software making the CM2723 perfect for any application.
Markets:
• Construction equipment
• Transportation
• Agriculture machinery
• Material handling equipment
• Electric mobile equipment
Features/Benefits:
• Monitors up to 27 inputs - analog, digital or frequency
• 8 high-side 3.4 A outputs
• 8 high-side 300mA outputs
• 6 low-side 2.5A outputs
• Pulse Width Modulation for proportional valve control
Applications:
• Skid-Steers and Mini Excavator Machine Control
• Backhoe, Telehandler and Loader Machine Control
• Material Handling Machine Control